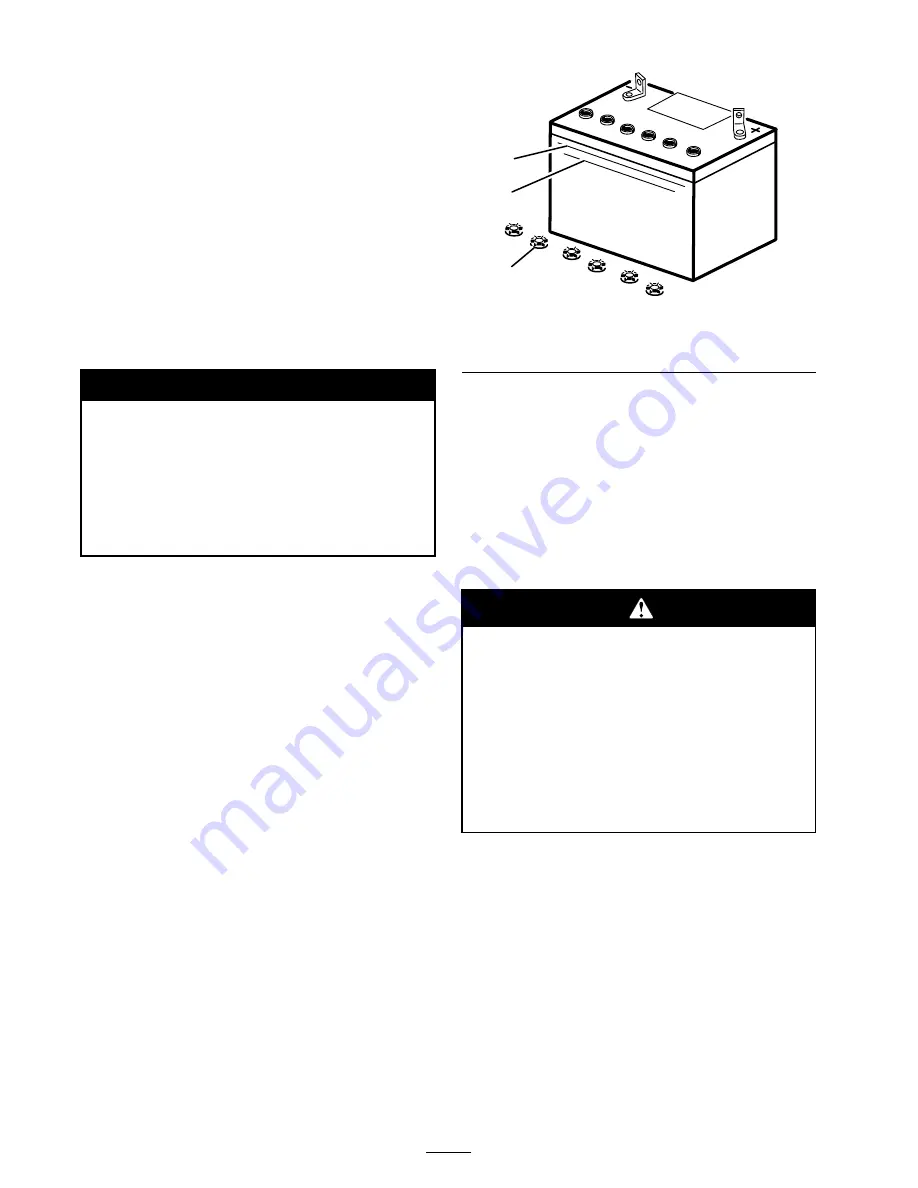
1. Lower the loader arms, stop the engine, and
remove the key.
2. Syphon the gasoline from the tank using a
pump type syphon.
Note:
Now is the best time to install a new fuel
filter because the fuel tank is empty.
Electrical System
Maintenance
Servicing the Battery
Warning
CALIFORNIA
Proposition 65 Warning
Battery posts, terminals, and related
accessories contain lead and lead
compounds, chemicals known to the State of
California to cause cancer and reproductive
harm. Wash hands after handling.
Important:
The following procedures
apply when servicing a (dry) battery that has
replaced the original battery. The original
(wet) battery does not require service.
Check the electrolyte level in the battery every 100
hours. Always keep the battery clean and fully
charged. Use a paper towel to clean the battery
case. If the battery terminals are corroded, clean
them with a solution of four parts water and one
part baking soda. Apply a light coating of grease
to the battery terminals to reduce corrosion.
Voltage: 12 v, 450 Cold Cranking Amps
Checking the Electrolyte Level
1. Stop the engine and remove the key.
2. Remove the 4 bolts securing the battery cover
and remove it from over the battery.
3. Look at the side of the battery. The electrolyte
must be up to the Upper line (Figure 34).
Do not allow the electrolyte to fall below the
Lower line (Figure 34).
2
3
1
G003794
Figure 34
1. Filler caps
3. Lower line
2. Upper line
4. If the electrolyte is low, add the required
amount of distilled water; refer to Adding
Water to the Battery.
Adding Water to the Battery
The best time to add distilled water to the battery
is just before you operate the traction unit. This
lets the water mix thoroughly with the electrolyte
solution.
Battery electrolyte contains sulfuric acid
which is a deadly poison and causes severe
burns.
•
Do not drink electrolyte and avoid
contact with skin, eyes or clothing. Wear
safety glasses to shield your eyes and
rubber gloves to protect your hands.
•
Fill the battery where clean water is
always available for flushing the skin.
1. Remove the battery from the traction unit.
Important:
Never fill the battery with
distilled water while the battery is installed
in the traction unit. Electrolyte could be
spilled on other parts and cause corrosion.
2. Clean the top of the battery with a paper towel.
3. Remove the filler caps from the battery
(Figure 34).
4. Slowly pour distilled water into each battery
cell until the electrolyte level is up to the Upper
line (Figure 34) on the battery case.
32
Summary of Contents for 22306
Page 8: ...Slope Chart 8...
Page 11: ...108 4670 108 4671 93 9084 1 Lift point 2 Tie down point 11...
Page 46: ...Schematics Electrical Schematic Rev A 46...
Page 47: ...Hydraulic Schematic Rev A 47...
Page 48: ......
Page 49: ......
Page 50: ......