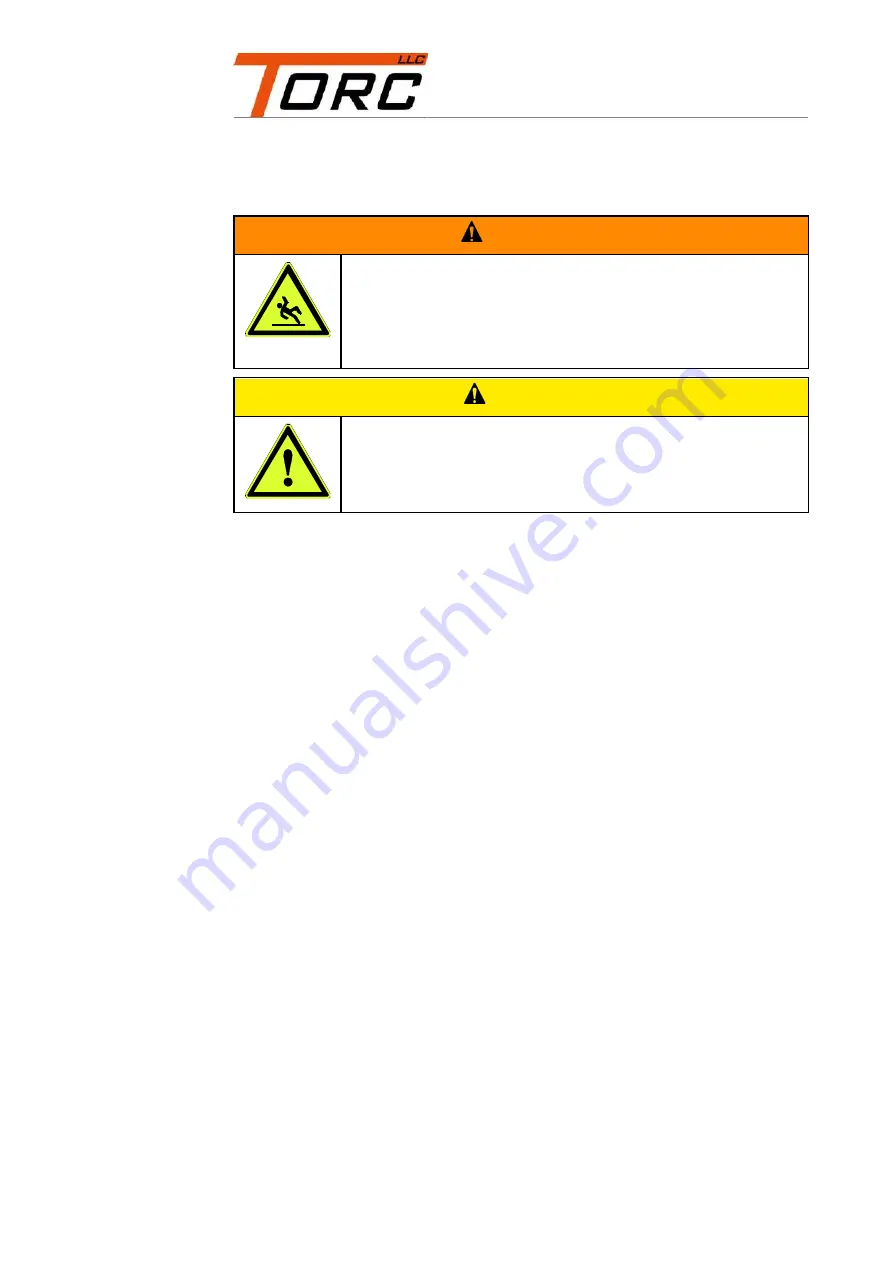
Carrying out maintenance tasks
17
Carrying out maintenance tasks
Changing the hydraulic oil
WARNING
Slipping hazard from leaked oil.
Bruising and bone fractures possible.
Clean up any leaked oil with a cloth or suitable binding
agents.
Wear safety shoes with non-slip soles.
CAUTION
Health hazard from contact with hydraulic oil.
Wear nitrile gloves and chemical-resistant protective
goggles during work that may include contact with
hydraulic oil.
To change the hydraulic oil, proceed as follows:
Switch off the unit.
Disconnect the mains plug.
Leave the hydraulic oil to cool until it is tepid.
Place a container under the oil drain plug which can hold the oil volume in
the unit, 8 l (2.1 gal).
Open the oil drain plug.
The hydraulic oil will flow into the container.
Check the seal of the drain plug for damage.
Replace the damaged seal if required.
After completely draining the hydraulic oil from the oil tank, seal the oil drain
opening with the oil drain plug.
Tighten the oil drain plug with a torque of 20 N m.
Open the filler opening of the unit.
Fill in fresh hydraulic oil (manufacturer's recommendation: Castrol Hyspin
HVI 32) until the oil level fills half of the upper sight glass.
Close the filler opening with the corresponding cap.
Dispose of the drained hydraulic oil in line with the environmental
regulations at the place of installation.