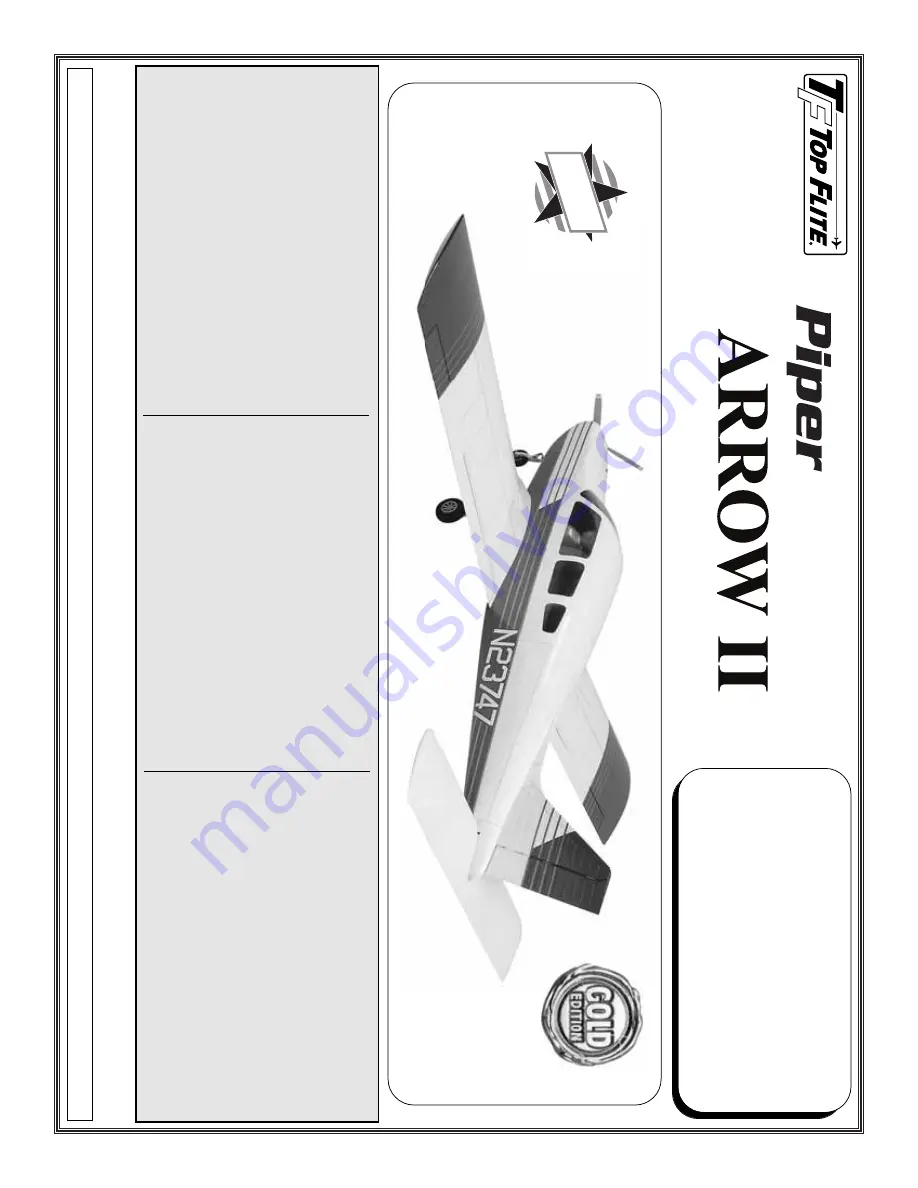
W
ARRANTY
:
T
op Flite Models guar
antees this kit
to be free from def
ects in both mater
ial and
w
o
rkmanship at the date of purchase
.
This
w
arr
anty does not co
v
er an
y component par
ts
damaged b
y
use or modification.
In no case shall
T
op Flite’
s liability e
xceed the or
iginal cost of the
purchased kit.
Fur
ther
,
T
op Flite reser
v
es the r
ight
to change or modify this w
arr
anty without notice
.
In
that
T
op Flite has no control o
v
er the final assemb
ly
or mater
ial used f
or final assemb
ly
, no liability shall
be assumed nor accepted f
or an
y damage
resulting from the use b
y
the user of the final user-
assemb
led product.
By the act of using the user-
assemb
led product, the user accepts all resulting
liability
.If the b
u
y
e
r is not prepared to accept the
liability associated with the use of this pr
oduct,
the b
u
y
er is ad
vised to return this kit
immediatel
y in ne
w and un
used condition to
the place of pur
c
hase
.
T
o
mak
e
a w
arr
anty claim
send the def
ectiv
e par
t or item to Hob
b
y
Ser
vices
at the address belo
w
.
Hobb
y Ser
vices
3002 N.
Apollo Dr
.
Suite 1
Champaign IL 61822
USA
Include a letter stating y
our name
, retur
n shipping
address
, as m
uch contact inf
or
mation as possib
le
(da
ytime telephone n
umber
, f
ax n
umber
address), a detailed descr
iption of the prob
lem and
a photocop
y of the purchase receipt.
Upon receipt
of the pac
kage the prob
lem will be e
v
aluated as
quic
kly as possib
le
.
T
op Flite Models • Champaign,
Illinois •
T
elephone (217) 398-8970 e
xt.
5 • F
ax (217) 398-7721 • pr
oductsuppor
t@top-flite
.com
READ
THR
OUGH
THIS INSTR
UCTION BOOK FIRST
.
IT CONT
AINS IMPOR
T
ANT INSTR
UCTIONS AND
W
ARNINGS CONCERNING
THE ASSEMBL
Y AND USE OF
THI
S MODEL.
AR
O6PO4
V1.0
Entire Contents © Cop
yr
ight 2004
Wingspan:
81 in [2060mm]
Wing Area:
1089 sq in [70.2 dm
2
]
W
eight:
12–14 lb [5440–6350 g]
Wing Loading:
25–30 oz/sq ft [76–92 g/dm
2
]
Fusela
g
e
Length:
61.5 in [1560mm]
Radio:
6-channel, 1 high-torque ser
v
o
, 5-7
standard ser
v
o
s
, 1 micro ser
v
o
(optional)
Engine:
.61–.91 cu in [10.0–15.0cc] tw
o-strok
e
,
.91 cu in [15.0cc] f
our-strok
e
T
op Flite Gold Edition Piper Arr
o
w II Assemb
ly
Instructions
USA
MADE
IN
™
Summary of Contents for Piper Arrow II
Page 8: ...8 DIE CUT DRAWINGS...
Page 9: ...9 DIE CUT DRAWINGS...
Page 77: ......
Page 78: ......
Page 79: ......