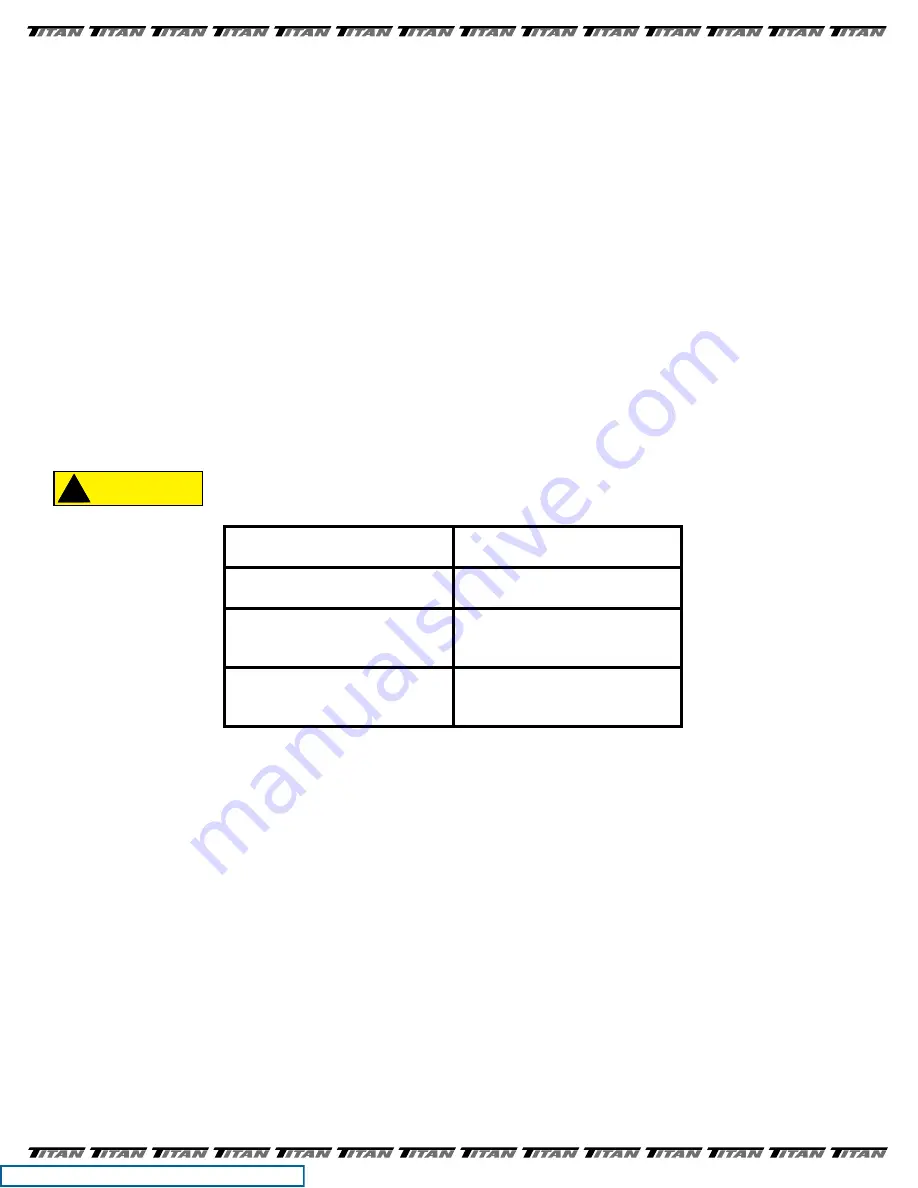
TM
N
CO
V EYORS
TM
N
CO
V EYORS
TM
N
CO
V EYORS
TM
N
CO
V EYORS
TM
N
CO
V EYORS
TM
N
CO
V EYORS
TM
N
CO
V EYORS
TM
N
CO
V EYORS
TM
N
CO
V EYORS
TM
N
CO
V EYORS
TM
N
CO
V EYORS
TM
N
CO
V EYORS
TM
N
CO
V EYORS
TM
N
CO
V EYORS
TM
N
CO
V EYORS
TM
N
CO
V EYORS
TM
N
CO
V EYORS
TM
N
CO
V EYORS
TM
N
CO
V EYORS
TM
N
CO
V EYORS
TM
N
CO
V EYORS
TM
N
CO
V EYORS
TM
N
CO
V EYORS
TM
N
CO
V EYORS
TM
N
CO
V EYORS
TM
N
CO
V EYORS
TM
N
CO
V EYORS
TM
N
CO
V EYORS
7/21
9
•
Too tight of a belt will usually pulsate as it moves through the frame. Another indication that
a belt is too tight is when there is an above normal ampere draw. Excessive tension causes
increased wear and reduced belt life.
•
Too loose of a belt buckles as it leaves the infeed sprockets and as it contacts the drive sprockets.
This condition often causes jamming and can easily damage the belt.
MOTORS
1. CLEANING
- All motors should be kept free of dirt and grease accumulations. Open motors should be periodically
vacuumed to remove dust and dirt fromthe windings.
2. VENTILATION
- For best results motors should be operated in an area where adequate ventilation is available.
3. TEMPERATURE
- Most of todays smooth body T.E.N.V. and T.E.F.C. motors run hot to the touch. As long as
maximum ambient temperatures are not exceeded, and more importantly, ampere draw is within the allowable
range, there should be no need to worry. (Both of these limits are found on the motor nameplate.)
4. LUBRICATION
- Most electric motors are lubricated for life and under normal conditions require no more lubrication.
Under severe conditions where additional lubrication is required, use the following chart as a guide.
The following chart is based on motors with grease lubricated bearings, running at
speeds of 1750 R.P.M. or less, and operating within an ambient temperature range of
between 0 degrees F.
to 120 degrees F.
Typical lubricants that can be used:
Chevron Oil Co. - SRI #2
Gulf Refining Co. - Precision #2 or #3
Shell Oil Co. - Alvania #2, Dolium R
Mobile Oil Co. - Mobilux Grease #2
Texaco Inc. - Premium RB
Sinclair Refining Co. - A.F. #2
REDUCERS
The following reducer information is concerned primarily with worm gear reducers. If your conveyor is equipped with another
type, refer to the manufacturer’s recommendations for installation and maintenance sent along at time of shipment.
1.
ASSEMBLE / DISASSEMBLE MOTOR TO REDUCER
- Because many of today's motor keyways are cut with
a sidemill cutter, the following assembly instructions should be followed to insure a trouble-free fit between motor
and reducer. First, place the key into the reducer keyway. Second, line up the motor keyseat with the key and
push the motor shaft into the reducer bore. Third, finish assembly by bolting themotor to the reducer flange.
This insures that the key does not slide back in the motor keyseat. See
FIGURE 5
.
CAUTION
!
CONDITION
LUBRICATING
FREQUENCY
Normal 8 hr. day
Light Loads
2 to 3 years
Heavy 24 hr. Day
Heavy Loads
Dirty Conditions
1 Year
Extreme
Shock Loads
High Temperatures
3 to 6 Months
Go to Table of Contents