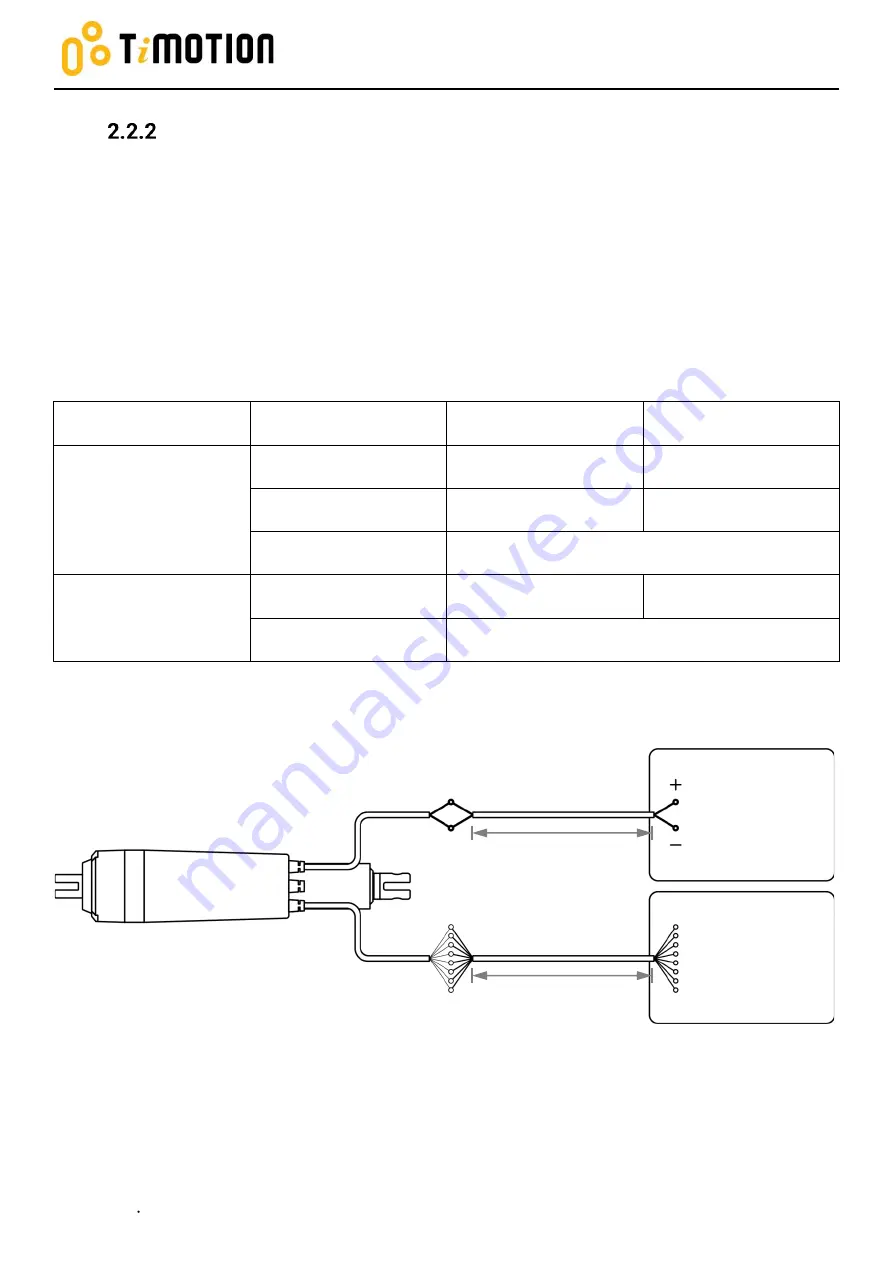
User Manual-MA2T
Version A August 2021
11 of 25
11
Extension power cable
The actuator is supplied with a power cable (and/or signal cable). The cable(s) has/have flying leads in one
end for the user’s equipment connections. On the other end of the actuator, the cable is integrated into the
connector cover. The plug-in connector allows the user to replace the actuator without disconnecting the
flying leads.
Using the extension power cable from the DC source with the proper size is important to avoid a significant
voltage drop. The further away the DC source is, the larger the extension cable may need to be. Please refer
to the following table for the recommendation of the extension power cable size.
Extension cable type
Length of cable (L)
Cross-section (X)
AWG
Power extension cable L1
0 - 4 m
2.08 mm2
AWG 14
4 - 10 m
3.31 mm2
AWG 12
>10 m
Check with your TiMOTION contact representative
Signal extension cable L3
<10 m
0.5 mm2
AWG 20
>10 m
Check with your TiMOTION contact representative
Power cable
L1
L3
12V DC
or
24V DC
Control Box
or
PLC
P1
P3
Signal cable
Power cable: 14AWG
Signal cable: 20AWG