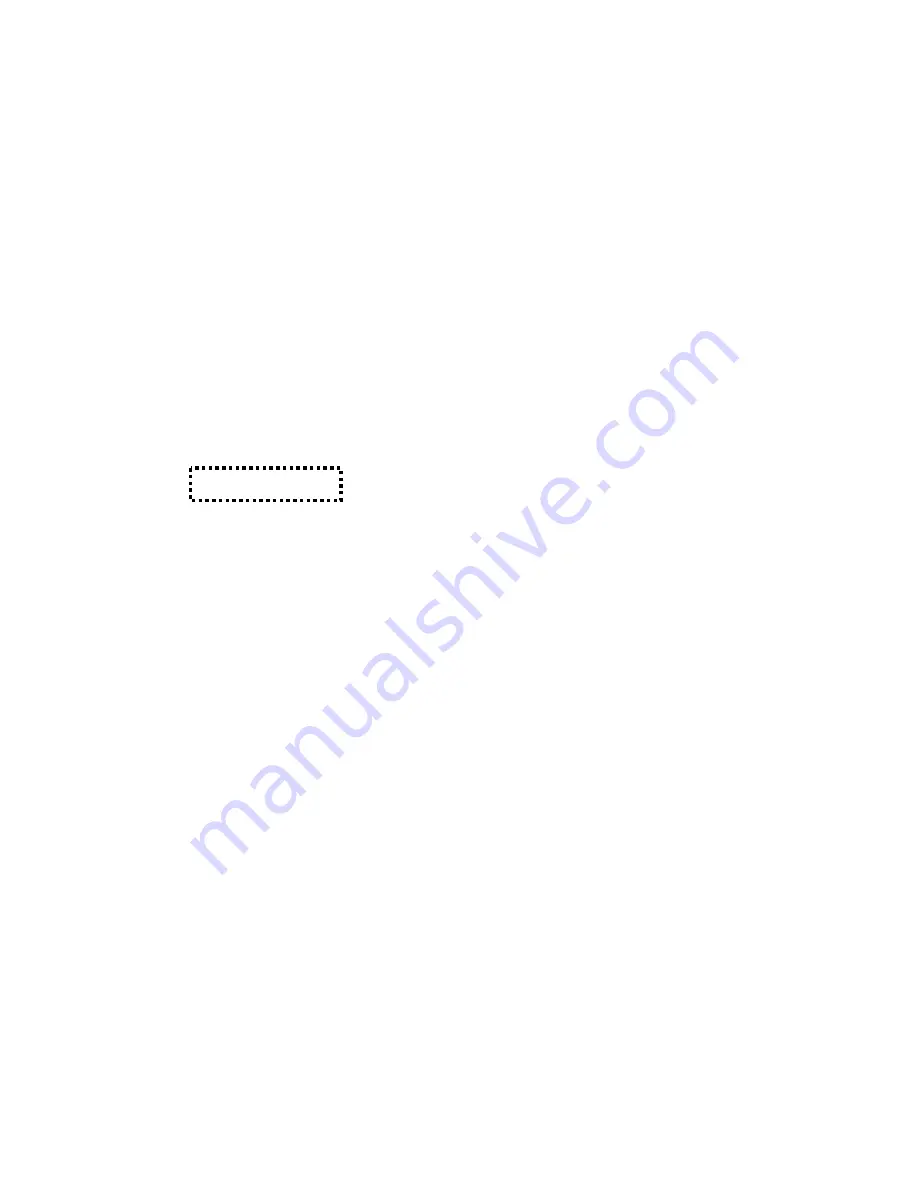
THRUSH AIRCRAFT, INC – MODEL S2R-R1340 THRUSH 600
AIRCRAFT MAINTENANCE MANUAL
Effective: 01/01/08
2-35
BATTERY MAINTENANCE
The 24-volt battery is installed in the
engine compartment between the engine
and firewall. Access is gained to the
battery by removal of the right side
cowling. Battery servicing involves adding
distilled water to maintain electrolyte level
of at least 3/16 inch over the separators,
checking the cable connections, and
neutralizing or cleaning any spilled
electrolyte or any corrosion. Use
bicarbonate of soda and clean water to
neutralize corrosion. Follow with a
thorough flushing of clean water and wipe
dry. Clean the cable and terminal
connections with a wire brush and coat
with petroleum jelly to minimize corrosion.
Do not allow the bicarbonate of
soda to enter the battery filler
openings, as it will neutralize the
electrolyte, which could
permanently damage the
batteries.
A hydrometer test of the battery’s solution
should be made each 50 hours of
operation, or more often in hot weather. If
the specific gravity tests 1.240, the battery
should be removed and recharged. The
solution levels should be examined and,
when necessary, add distilled water to
maintain the minimum level of 3/16 inch
over the separators. If distilled water is
added, do it just prior to recharging so that
the added water mixes with the solution.
When the recharging is completed, the
specific gravity should be between 1.275
and 1.300.
The battery should be checked for isolation
from the case. A voltmeter can be used to
check between the positive cell and the
case. A ground fault exists if there is a
reading on the voltmeter. A dated service
record shall be attached or stamped on the
terminal side of the battery to indicate that
the battery has been capacity tested.
AIRFRAME MAINTENANCE
CORROSION CONTROL
Cleanliness is the key to corrosion
control/prevention on the Thrush. Side
skins are attached with easily removable
quarter turn fasteners so the fuselage
interior can be made completely
accessible quickly. Daily cleaning of the
aircraft exterior and interior is highly
recommended. During the working season
cleaning intervals should never be more
than a week.
Clean the aircraft prior to performing any
inspections on the airframe or engine.
Before removal of detachable skins,
fairings, and cowlings wash all exterior
surfaces of the aircraft with plain water and
any commercial soap or detergent. Soap
and detergent are organic chemicals and it
is important that all traces be removed by
flushing with plain water.
*NOTE*
Certain chemicals cannot be
removed effectively by detergent
solutions. Special cleaning
agents are available for that
purpose. Be careful, however,
that they will not harm the
corrosion protection properties
of the finish. It is suggested that
chemical suppliers be contacted
for cleaning agents that are
suitable for those special needs.
A regular and thorough cleaning of both
the interior and exterior of the aircraft is a
major part of corrosion control. All areas of
the aircraft are accessible for cleaning by
removal of the panels. The cleaning
procedure that follows is recommended for
general purposes.
a. Wash all exterior surfaces of the
aircraft with plain water and any
commercial soap or detergent. Soap
and detergent are organic chemicals,
and it is important that all traces be
removed by flushing with plain water.
CAUTION