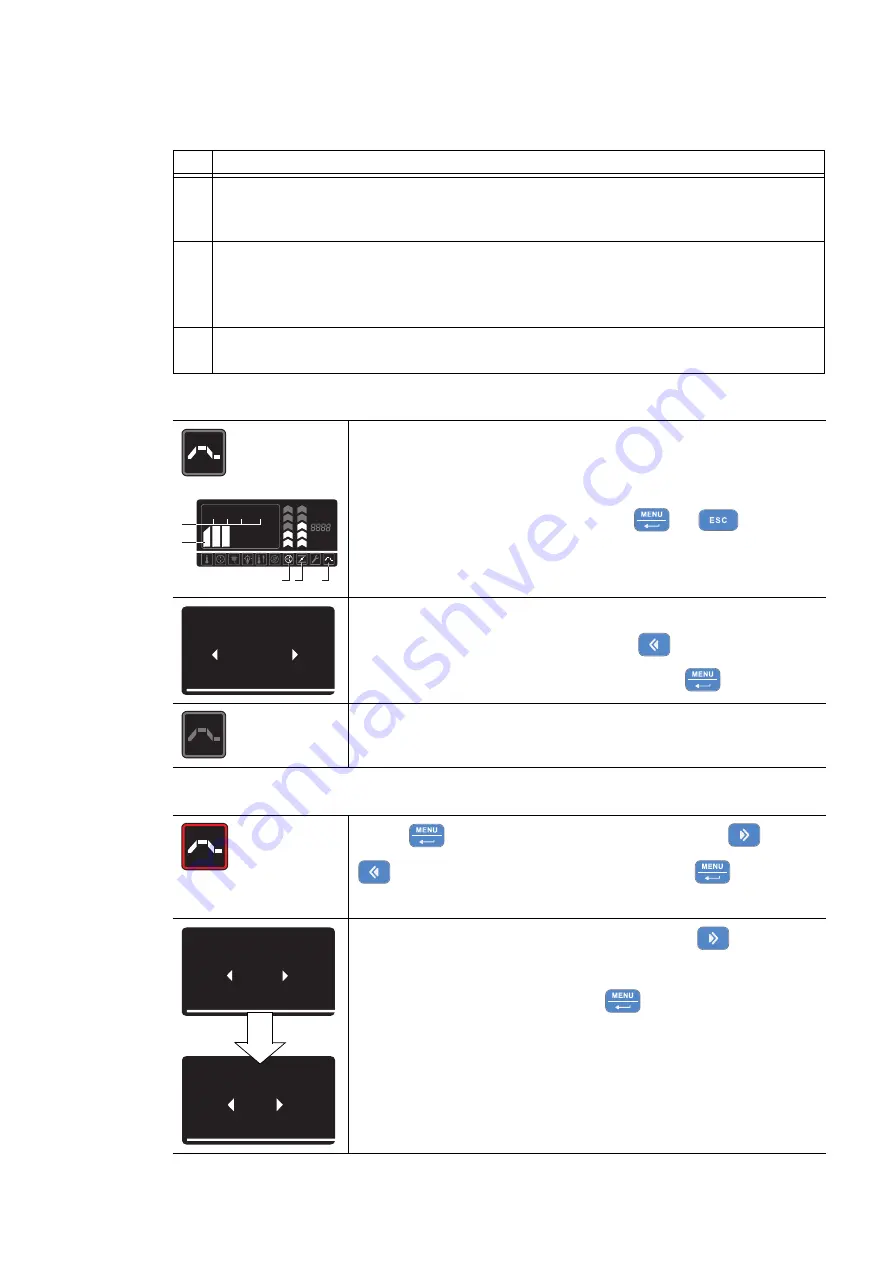
Handling and Control
Programming
7-28
Heratherm IMP
Thermo Scientific
3
The
Fan
icon is illuminated to indicate that the fan has been turned on for the
current step of the program. The fan speed level can be determined from the bar
graph located directly above the icon (see
table
7-2
on
page
7-3
).
4
The
Damper
icon is illuminated to indicate that the fan damper has been
opened for the current step of the program. The damper position can be deter
-
mined from the bar graph located directly above the icon (see
table
7-2
on
page
7-3
).
5
The
Program
icon in the menu bar is illuminated to indicate that a user program
is running.
Table 7-30 Abborting a Program
While a program is running (as indicated by the flashing
bar, program number and remaining time counter in the
multifunctional display pane and the
Program
icon
illuminated in the menu bar) press
or
.
When the prompt shown at left appears in the
multifunctional display pane, press
to choose the
Yes
option and confirm the selection with
.
The display returns to its default mode.
The
Program
icon in the menu bar will go out.
Table 7-31 Creating a New Program
Press
to activate the menu bar, then use
or
to select the
Program
icon and press
to
confirm.
In the selection screen that appears press
to
switch from the preselected option
Start
option to
New
,
then confirm the selection with
.
Table 7-29 Display Elements Active during Program Execution
No. Function
13.04.2010 11:05
P1 L1 S1 3:02
1
3
4
5
2
2010-04-16 3:07
PM
Stop Program?
No Yes
2010-04-13 10:25
AM
Program
Start
2010-04-13 10:25
AM
Program
New
Summary of Contents for IMP 180
Page 1: ......
Page 6: ...Contents iv Heratherm IMP Thermo Scientific...
Page 8: ...List of Figures ii Heratherm IMP Thermo Scientific...
Page 40: ...Product Description Additional Tube Access Ports Option 4 14 Heratherm IMP Thermo Scientific...
Page 88: ...Handling and Control Programming 7 34 Heratherm IMP Thermo Scientific...
Page 90: ...Shut down Shutting the refrigerated incubator down 8 2 Heratherm IMP Thermo Scientific...
Page 110: ...Technical Data 13 4 Heratherm IMP Thermo Scientific...
Page 114: ...Device Log 15 2 Heratherm IMP Thermo Scientific...
Page 117: ...Contact Thermo Scientific Heratherm IMP 16 3...
Page 118: ...Contact 16 4 Heratherm IMP Thermo Scientific...