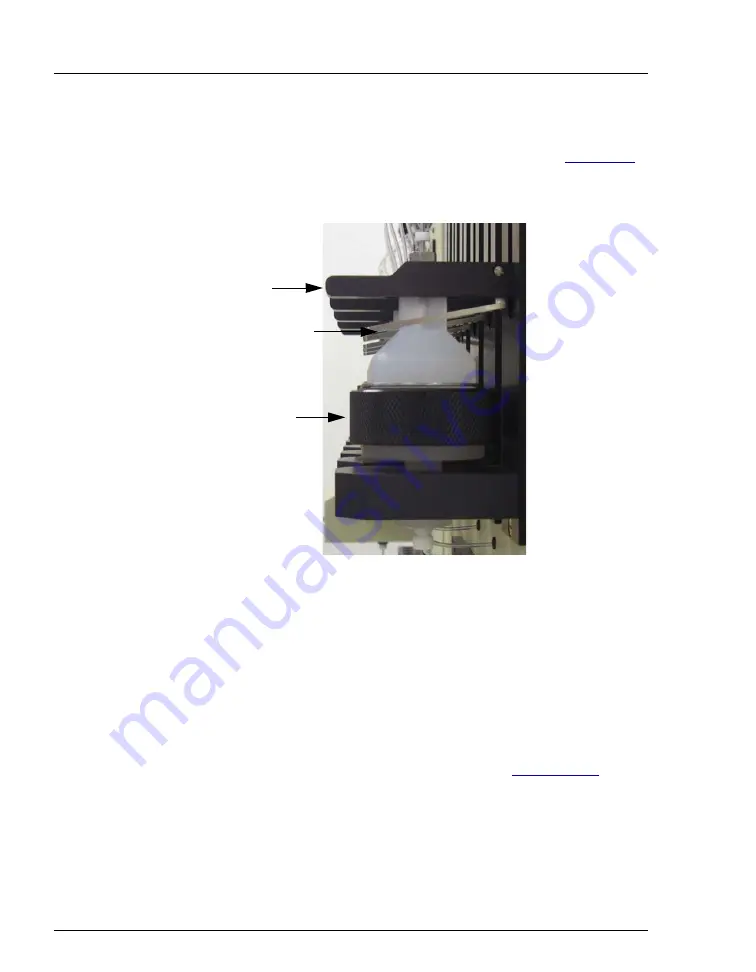
Dionex AutoTrace 280 Operator’s Manual
60
Doc. 065330-05 03/2020
3.7.5
Removing Used Disks
Remove the used disks by unscrewing the locking collar (see
squeezing the clip and moving it up toward the lever, and sliding the
holder up.
Figure 3-6. Disk Holder–Side View
3.7.6
Preparing the Next Sample Batch
Unless the last steps of the method were
Clean Sample Path
steps,
always clean the sample lines between batches of samples.
1. Place an empty cartridge in each holder.
2. Make sure each holder is in the fully down position, with the holder
LED on. (There is no need to place an empty disk in each holder.)
3. Load the
Clean Sample Path
4. Start running the method.
Lever
Clip
Locking Collar