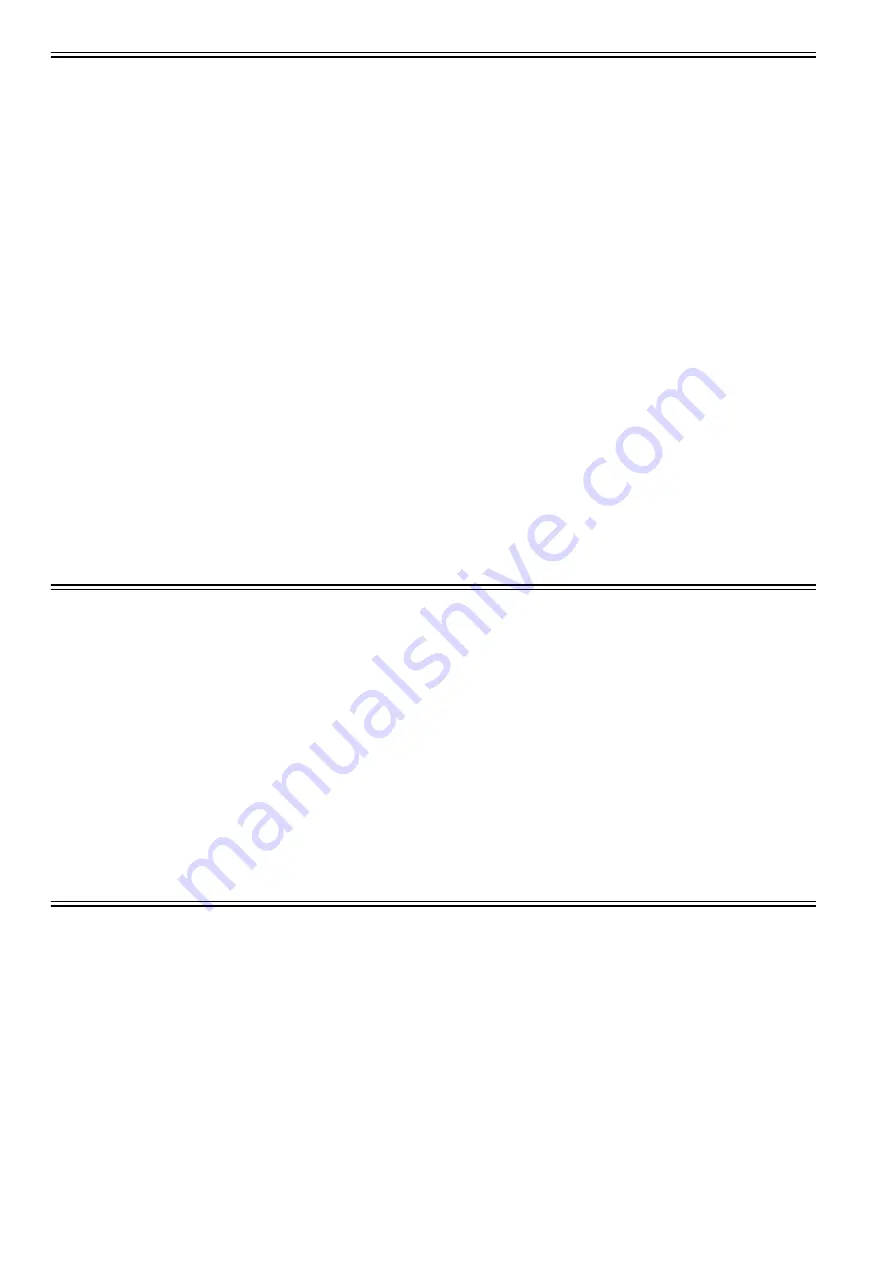
Refrigeration Maintenance
10-46
PURGE VALVE (PV) TEST
1. Attach a gauge manifold to the suction service valve and the discharge service valve. Attach another low pressure gauge to
the suction access port located in the suction line near the accumulator inlet. A low loss fitting must be used on the hose
connected to the suction access port.
2. Operate the unit with all zones in low speed cool.
3. Front seat the receiver tank outlet valve and allow the low side to pump down to 0 to 5 in. Hg vacuum (0 to -17 kPa).
4. Turn the unit Off.
5. Front seat the suction service valve to isolate the low side while it is still in a vacuum.
6. Watch the low pressure gauge attached to the suction access port. The low side pressure should not rise. It it does, there could
be a leak through one (or more) of following components: hot gas solenoid, purge valve, hot gas bypass solenoid, or receiver
tank pressure check valve.
7. Check the temperatures of the refrigeration lines on each side of the PV by hand. A temperature difference between the two
sides of the PV indicates it is leaking.
8. Use the Mechanics/Premium HMI Control Panel to enter the Interface Board Test Mode. Refer to the appropriate
Microprocessor Diagnostic Manual for specific information about the Interface Board Test Mode.
9. From the Interface Board Test Mode select Purge Valve.
10. Momentarily energize the PV with the Interface Board Test Mode by pressing the TEMP ON key. The low side pressure
should rise slightly. If the low side pressure does not rise, the PV is not opening. Check the continuity of the wiring and the
solenoid coil before assuming the solenoid is faulty.
NOTE: On units with a TSD Controller disconnect the purge valve wires from the main wire harness and use jumper
wires to momentarily (for approximately 1 second) energize the PV. The low side pressure should rise slightly. If the low
side pressure does not rise, the PV is not opening. Check the continuity of the wiring and the solenoid coil before
assuming the solenoid is faulty. Reconnect the purge valve wires to the main wire harness.
11. Back seat the receiver tank outlet valve and the suction service valve. Perform a “Refrigerant Gauge Removal” procedure.
RECEIVER TANK PRESSURE CHECK VALVE TEST
1. Attach a gauge manifold to the suction service valve and the discharge service valve. Attach another low pressure gauge to
the suction access port located in the suction line near the accumulator inlet. A low loss fitting must be used on the hose
connected to the suction access port.
2. Operate the unit in low speed cool.
3. Front seat the receiver tank outlet valve and allow the low side to pump down to 0 to 5 in. Hg vacuum (0 to -17 kPa).
4. Turn the unit Off.
5. Front seat the suction service valve to isolate the low side while it is still in a vacuum.
6. Watch the low pressure gauge attached to the suction access port. The low side pressure should not rise. If it does, there could
be a leak through the hot gas solenoid or the receiver tank pressure check valve (or both).
7. Check the temperatures of the refrigeration lines on each side of the receiver tank pressure check valve by hand. A temperature
difference between the two sides of the receiver tank pressure check valve indicates it is leaking.
8. Back seat the receiver tank outlet valve and the suction service valve, and remove the gauges to return the unit to normal
operation.
RECEIVER TANK PRESSURE SOLENOID (RTPS) TEST (MULTI-TEMP UNITS ONLY)
The receiver tank pressure solenoid is open when one or more zones are in heat. This moves the refrigerant out of the receiver
tank to improve heating capacity.
A leaking receiver tank pressure solenoid will reduce the cooling capacity when all zones are in cool because some of the
refrigerant bypasses the condenser. See “Condenser Check Valve, Purge Check Valve, and Receiver Tank Pressure Solenoid
Leak Test” to test for a leaking receiver tank pressure solenoid.
If the receiver tank pressure solenoid is stuck closed, the heating capacity may be reduced. If liquid refrigerant is visible in the
receiver tank sight glass when one or more zones are in heat, the receiver tank pressure solenoid is probably stuck closed. Use
the following procedure to see if the receiver tank pressure solenoid is opening correctly.
1. Attach a gauge manifold to the suction service valve and the discharge service port. Attach another low pressure gauge to the
suction access port located in the suction line near the accumulator inlet. Attach a high pressure gauge to the service port on
the receiver tank outlet valve. Low loss fittings must be used on the hoses connected to the discharge service port and the
suction access port.
2. Operate the unit with all zones in low speed cool until the system pressures stabilize.
CAUTION: Do not run scroll compressor in a vacuum for more than 1 minute.
Summary of Contents for T-1000R
Page 14: ...Safety Precautions 2 6 Warning Decals 2e24151g0 ...
Page 34: ...Maintenance Inspection Schedule 4 10 ...
Page 57: ...Unit Description 5 23 Purge Mode UT Series 1 3 4 5 2 ...
Page 67: ...Unit Description 5 33 Zone 1 Cool and Zone 2 Cool UT SPECTRUM Units ...
Page 69: ...Unit Description 5 35 Purge Mode UT SPECTRUM Units ...
Page 71: ...Unit Description 5 37 Zone 1 Cool and Zone 2 Heat UT SPECTRUM Units ...
Page 72: ...Unit Description 5 38 ...
Page 74: ...Diesel Electric Menu 6 28 Adjust Brightness 6 29 Time 6 30 ...
Page 120: ...Operating Instructions Standard HMI 7 18 ...
Page 152: ...Engine Maintenance 9 14 T Series Fuel and Oil System Components TK 376 ...
Page 154: ...Engine Maintenance 9 16 T Series Fuel and Oil System Components TK 270 ...
Page 156: ...Engine Maintenance 9 18 UT Series Fuel System Components AMA768 ...
Page 172: ...Engine Maintenance 9 34 T Series Engine Mounting Components for 2 Cylinder Engine ...
Page 184: ...Engine Maintenance 9 46 ...
Page 238: ...Refrigeration Maintenance 10 54 ...
Page 246: ...Clutch Maintenance 11 8 ...
Page 258: ...Structural Maintenance 12 12 ...
Page 264: ...Mechanical Diagnosis 13 6 ...
Page 265: ...14 Electric Standby Diagnosis ...
Page 268: ...Electric Standby Diagnosis 14 4 ...
Page 269: ...15 Refrigeration System Diagnosis ...
Page 272: ...Refrigeration System Diagnosis 15 4 ...
Page 280: ...Remote Evaporators 16 8 ...