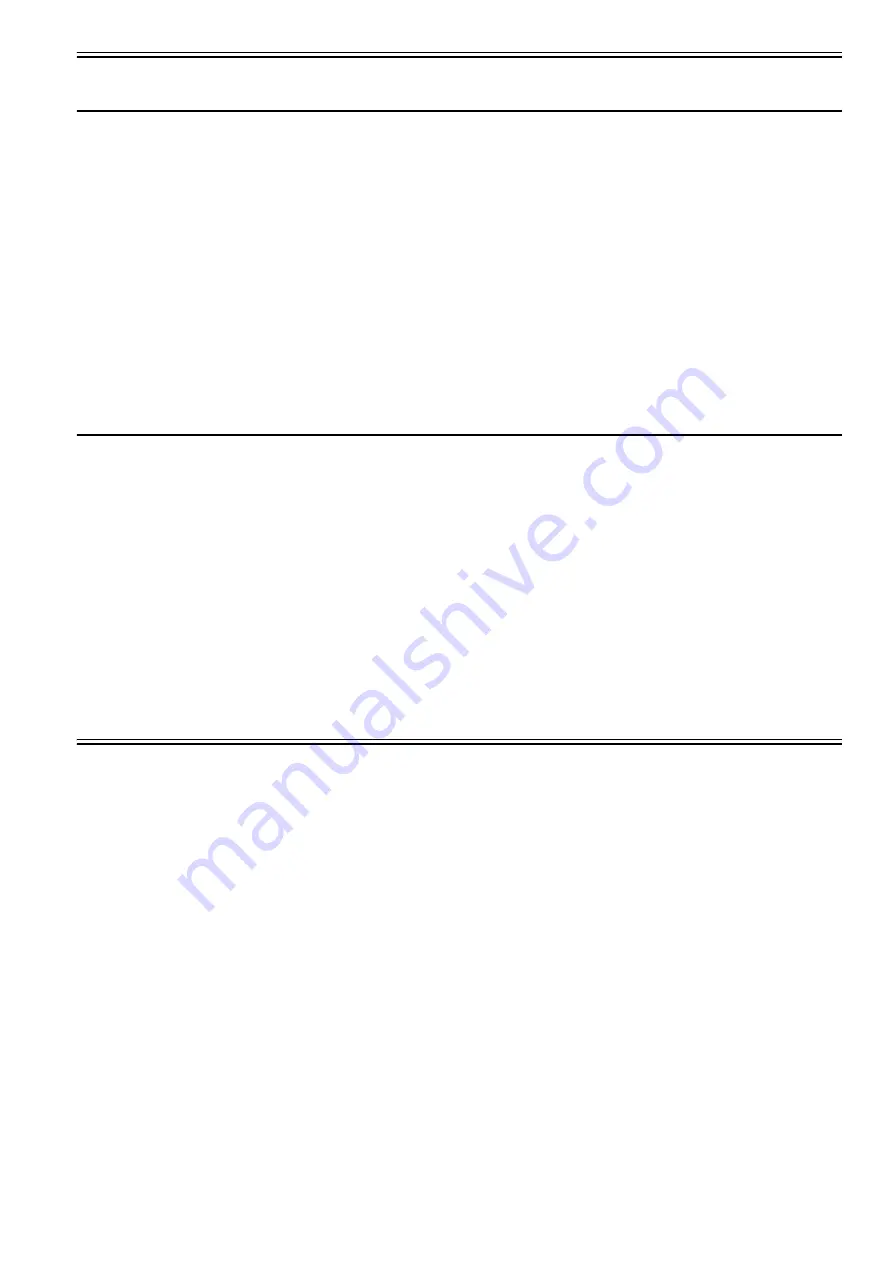
Refrigeration Maintenance
10-23
RECIPROCATING COMPRESSOR REPLACEMENT (T-SERIES)
Removal
1. Perform a “Low Side Pump Down” to prepare unit to perform service.
2. Front seat the discharge and suction service valves.
3. Open both service manifold hand valves to bleed the pressure in the head into the compressor crankcase.
4. Loosen and remove the electric motor (jackshaft)/compressor belt from the compressor pulley.
5. Disconnect the high pressure cutout switch wires.
6. Unbolt the discharge and suction valves from the compressor.
7. Unsolder and remove the discharge and suction lines where necessary to allow clearance for removing the compressor.
8. Remove the compressor/frame bracket and the compressor mounting bolts.
9. Lift the compressor out of the unit. Keep the compressor ports covered to prevent dust, dirt, etc., from falling into the
compressor.
NOTE: When the compressor is removed from the unit, the oil level should be noted, or the oil removed from the
compressor should be measured so that the same amount of oil can be added before placing the replacement compressor
in the unit.
Installation
1. Lift the compressor into the unit and install the mounting bolts and the compressor/frame bracket.
2. Install the discharge and suction lines and attach the discharge and suction service valves to the compressor using new gaskets
soaked in refrigeration oil.
3. Reconnect (solder) the discharge and suction lines.
4. Reconnect the high pressure cutout switch wires.
5. Pressurize the compressor and test for refrigerant leaks.
6. If no leaks are found, replace the liquid line drier then evacuate the low side.
7. Replace the compressor/electric motor belt and adjust the tension.
8. Back seat the receiver tank outlet valve. Mid seat the discharge and suction service valves.
9. Operate the unit at least 30 minutes and then inspect the oil level in the compressor. Add or remove oil if necessary.
10. Check the refrigerant charge and add refrigerant if needed.
11. Perform a “Refrigerant Gauge Removal” procedure.
COMPRESSOR OIL FILTER
This unit is equipped with a compressor bypass oil filter. The compressor oil filter should be changed when the drier is
replaced.
The outlet fitting is larger than the inlet fitting, so the compressor oil filter cannot be put on backwards. There are two fittings
on the inlet end of the compressor oil filter. The inlet fitting contains a check valve that prevents reverse flow through the
compressor oil filter. The capped fitting is called the oil pressure access port and is used to check the compressor oil pressure (see
“Checking Compressor Oil Pressure”).
Summary of Contents for T-1000R
Page 14: ...Safety Precautions 2 6 Warning Decals 2e24151g0 ...
Page 34: ...Maintenance Inspection Schedule 4 10 ...
Page 57: ...Unit Description 5 23 Purge Mode UT Series 1 3 4 5 2 ...
Page 67: ...Unit Description 5 33 Zone 1 Cool and Zone 2 Cool UT SPECTRUM Units ...
Page 69: ...Unit Description 5 35 Purge Mode UT SPECTRUM Units ...
Page 71: ...Unit Description 5 37 Zone 1 Cool and Zone 2 Heat UT SPECTRUM Units ...
Page 72: ...Unit Description 5 38 ...
Page 74: ...Diesel Electric Menu 6 28 Adjust Brightness 6 29 Time 6 30 ...
Page 120: ...Operating Instructions Standard HMI 7 18 ...
Page 152: ...Engine Maintenance 9 14 T Series Fuel and Oil System Components TK 376 ...
Page 154: ...Engine Maintenance 9 16 T Series Fuel and Oil System Components TK 270 ...
Page 156: ...Engine Maintenance 9 18 UT Series Fuel System Components AMA768 ...
Page 172: ...Engine Maintenance 9 34 T Series Engine Mounting Components for 2 Cylinder Engine ...
Page 184: ...Engine Maintenance 9 46 ...
Page 238: ...Refrigeration Maintenance 10 54 ...
Page 246: ...Clutch Maintenance 11 8 ...
Page 258: ...Structural Maintenance 12 12 ...
Page 264: ...Mechanical Diagnosis 13 6 ...
Page 265: ...14 Electric Standby Diagnosis ...
Page 268: ...Electric Standby Diagnosis 14 4 ...
Page 269: ...15 Refrigeration System Diagnosis ...
Page 272: ...Refrigeration System Diagnosis 15 4 ...
Page 280: ...Remote Evaporators 16 8 ...