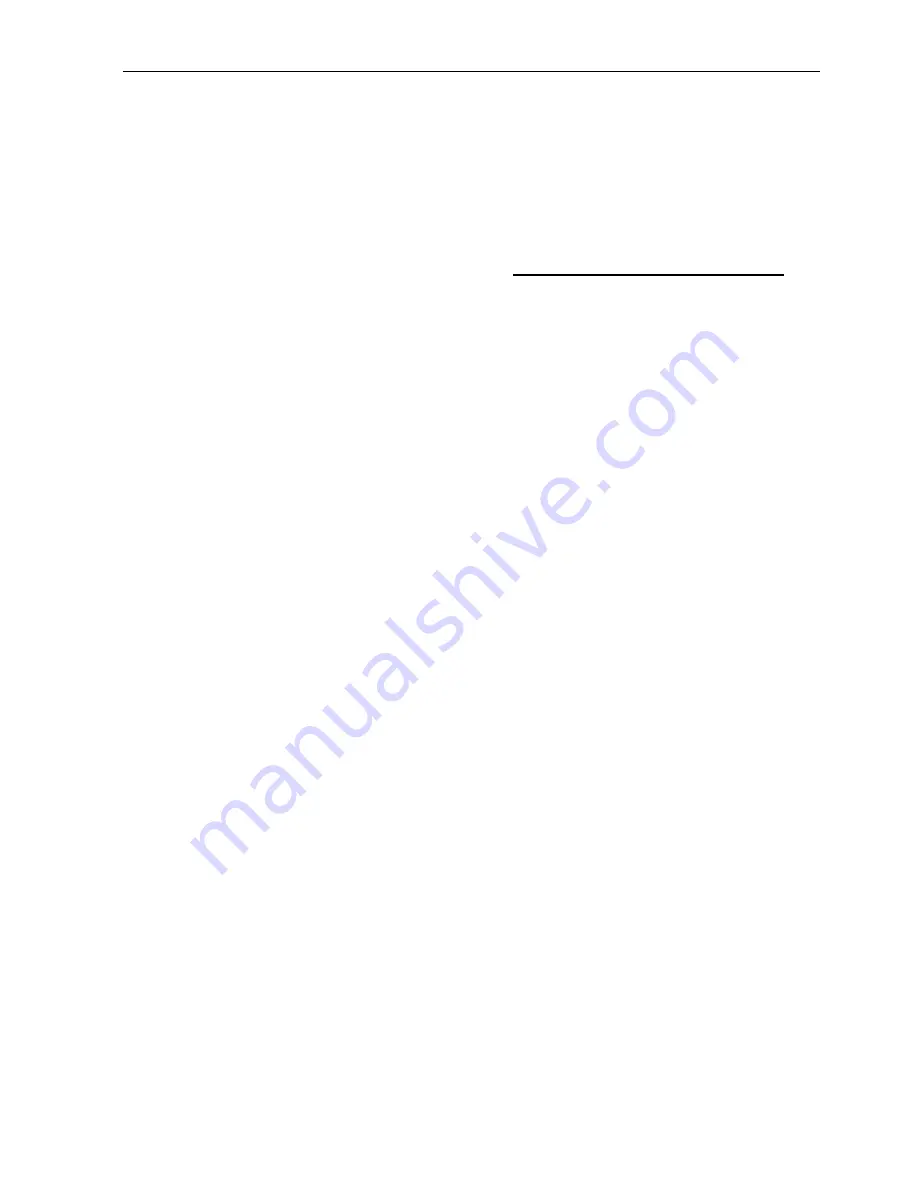
Refrigeration Service Operations
95
Use the following procedure to change the
compressor oil filter.
1. Pump down the low side and equalize the
pressure to slightly positive.
2. Front seat the discharge and suction service
valves. Remove the remaining refrigerant
from the compressor.
3. Disconnect the oil lines from the compressor
oil filter. Hold the oil filter with back-up
wrench on the hex behind the ORS fitting.
4. Remove the clamp and the compressor oil
filter.
5. Coat the new O-rings with clean compressor
oil and place them in the ORS fittings on the
ends of the new compressor oil filter.
6. Fasten the new compressor oil filter in place
with the clamp.
7. Attach and tighten the oil lines to the
compressor oil filter. Hold the oil filter with a
back-up wrench on the hex behind the ORS
fitting.
8. Evacuate the compressor and filter to a
maximum of 500 microns to remove trapped
air.
9. Open the service valves, operate the system,
and check the compressor oil filter for leaks.
Checking Compressor Oil
Pressure
The oil pressure at the oil pressure access port
varies with the suction pressure in the compressor.
Therefore, we need to calculate the “net oil
pressure” to determine the actual compressor oil
pressure. The net oil pressure is the pressure at the
oil pressure access port minus the suction pressure
below the throttling valve. Use the following
procedure to check the compressor oil pressure.
1. Attach a suitable oil pressure gauge to the oil
pressure access port on the compressor oil
filter.
2. Attach the low pressure gauge of a gauge
manifold to the fitting on the side of the
throttling valve. This fitting allows you to
monitor the suction pressure in the compressor
below the throttling valve.
3. Start the unit and note the pressure at the oil
pressure access port and the suction pressure
below the throttling valve.
4. Subtract the suction pressure below the
throttling valve from the pressure at the oil
pressure access port to get the net oil pressure.
5. The net oil pressure should be at least 20 psi
(138 kPa). If the net oil pressure is low, first
check the compressor oil level, then check the
compressor oil pump and relief valve.
Priming New Compressor
Installations
Thermo King remanufactured compressors have
had a special break in process to assure that the oil
pump is primed, functioning, and broken in. The
following procedure is recommended, but not
required for factory-remanufactured compressors.
This procedure must be followed to prevent
premature pump failure in any compressor that
has had an oil pump installed, especially a
compressor that has been stored for any length of
time.
1. Attach a suitable oil pressure gauge to the oil
pressure access port on the compressor oil
filter.
2. Attach the low pressure gauge of a gauge
manifold to the fitting on the side of the
throttling valve. This fitting allows you to
monitor the suction pressure in the compressor
below the throttling valve.
3. Disconnect the wires to the fuel solenoid.
4. Disconnect the wires to the high speed
solenoid.
NOTE: The microprocessor will probably
record some alarm codes because the
solenoids are disconnected and the engine
does not start. Clear these alarm codes as
necessary.
Pressure at Oil Pressure Access Port
– Suction Pressure Below Throttling Valve
= Net Oil Pressure
Summary of Contents for Spectrum DE 30-2
Page 4: ...4...
Page 12: ...Safety Precautions 12...
Page 16: ...Specifications 16...
Page 31: ...Unit Description 31 1 Access Panels 2 Defrost Dampers Figure 12 Back View of Unit 1 2 AGA215...
Page 42: ...Operating Instructions 42...
Page 48: ...Electrical Maintenance 48...
Page 106: ...Structural Maintenance 106...
Page 110: ...Mechanical Diagnosis 110...
Page 114: ...Remote Evaporator Specifications 114...
Page 116: ...Remote Evaporator Maintenance Inspection Schedule 116...
Page 122: ...Remote Evaporator Electrical Maintenance 122...
Page 126: ...Remote Evaporator Refrigeration Service Operations 126...
Page 128: ...Remote Evaporator Structural Maintenance 128...
Page 130: ...Remote Evaporator System Diagnosis 130...
Page 134: ...Wiring and Schematic Diagrams Index 134...
Page 135: ...135 Schematic Diagram Page 1 of 2...
Page 136: ...136 Schematic Diagram Page 2 of 2...
Page 137: ...137 Wiring Diagram Page 1 of 4...
Page 138: ...138 Wiring Diagram Page 2 of 4...
Page 139: ...139 Wiring Diagram Page 3 of 4...
Page 140: ...140 Wiring Diagram Page 4 of 4...