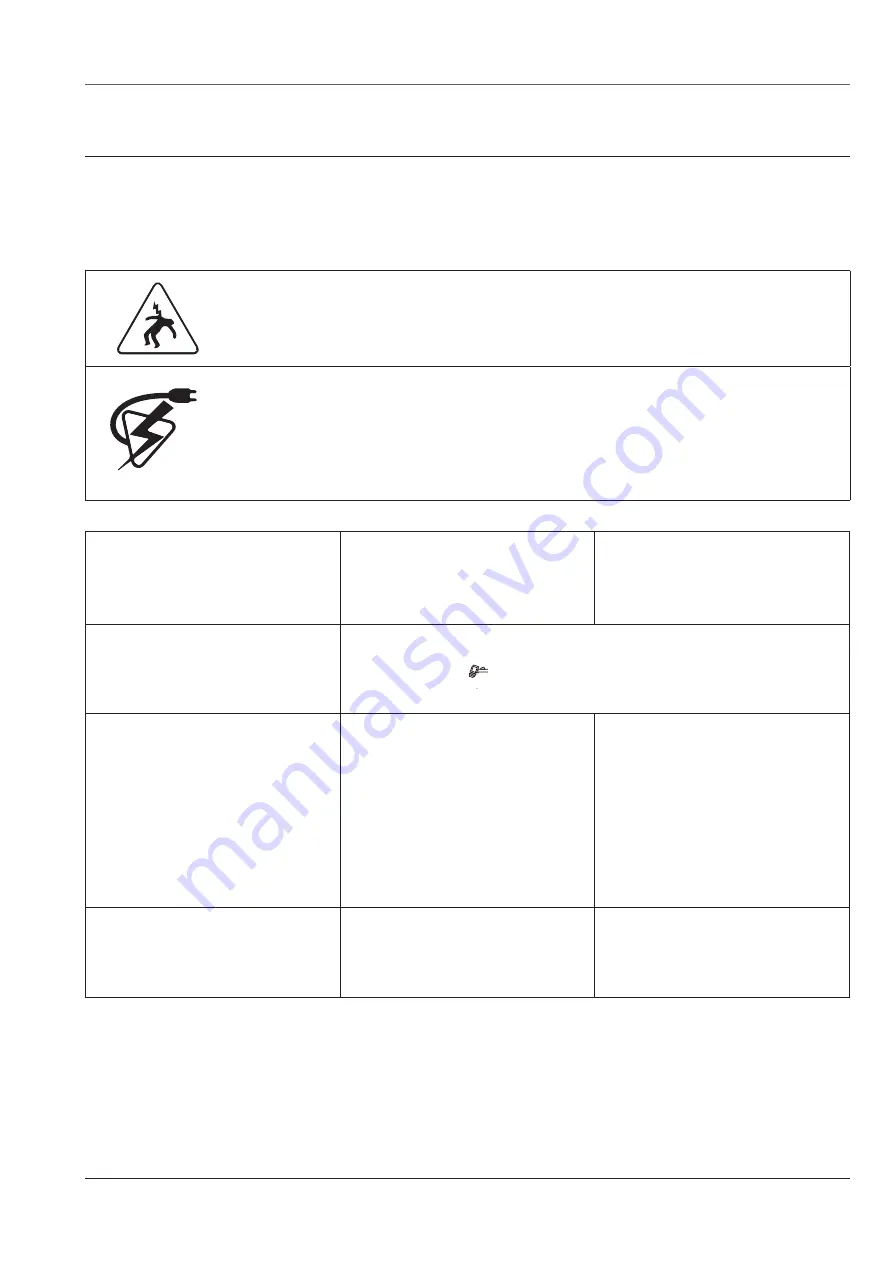
EX-TRAFIRE
®
75SD
Operator Manual, Revision T-5
5-45
Routine maintenance
WARNING
ELECTRIC SHOCK CAN KILL
Disconnect mains power lead before servicing; Qualified technicians only
should perform any work that requires removal of the system cover� Allow a
period (minimum 5 min�) for electrical discharge before handling internal parts�
MAINTENANCE
Every usage
Check the gas pressure�
Check the consumables�
Check the work clamp�
Ensure that consumables are
installed correctly and are not
worn�
Every week
Examine and check the torch retaining cap safety switch pins,
ensure that the LED3 safety indicator which indicates a loose
retaining cap is fully functional�
Every 3 months
Clean the dust from inside of
the power supply using clean
dry compressed air�
Advisory note:
The dust can be harmful to
health!
Full examination of the torch,
check the torch trigger safety
mechanism, check for signs of
cracking in the torch body or
exposed wires�
Immediately replace the mains
power lead/plug if damaged�
Immediately replace the torch
lead if damaged�
Check air-line hose, filter
elements, and connections for
leaks�