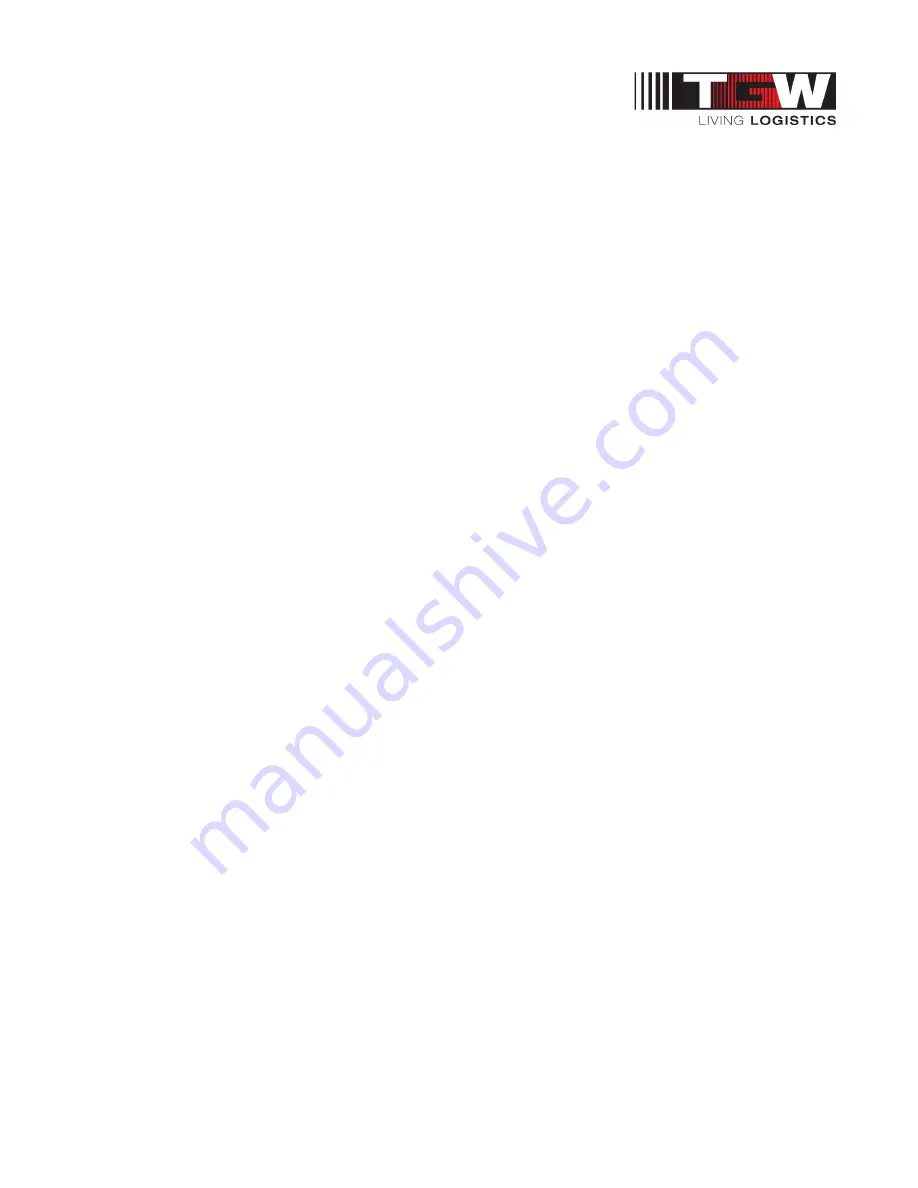
NBS®90 PolySort & SP IOM
P/N: 1193974
Revision Date: 4/25/2019
Page
60
of
83
9.7: NBS
C
OMMISSIONING OF
E
QUIPMENT
General
Commissioning of the equipment can best be defined as the final adjustments and test of the installed
equipment required for its proper operation. The need for commissioning is inherent, since the
individual components of equipment are brought together at the installation site to operate as a system.
Mechanical and electrical commissioning are most often carried out simultaneously. Commissioning
must simulate the actual operation of the system as closely as possible to demonstrate the ability to
perform reliably at the specified rate in the prescribed operational sequence.
During the Commissioning Phase, it is necessary to load the equipment with product to be conveyed,
which provides the means of detecting those areas requiring adjustment. Personnel will be required to
support operational functions. This may serve as part of operator training and familiarity with the
system. During the commissioning activity, special attention should be directed toward personnel
safety. No unnecessary risks should be taken that would endanger the safety of any personnel. All
personnel must familiarize themselves with all safety features of the system such as emergency stops
and motor disconnects.
Mechanical Static Checkout
(No power to the conveyor.)
•
The belt tension and air pressure must be set to the correct pressure setting, which is
dependent on sorter width. Air pressure higher than required can cause belt failure.
•
Listen for air leaks after air pressure is turned on.
•
Check the plumbing of the solenoids.
•
Follow the belt path through the entire conveyor. The belt must be threaded through the
drive per the diagram in the Belt Installation section, all of the belts must be captured
between the grooved guide pulleys at each diverter location, and no belt should be threaded
under a crossmember (belt path labels are attached at each diverter location from the
factory).
•
Visually inspect the installation. Is the conveyor straight? Is the conveyor reasonably level
from side to side? From end-to-end?
•
Check guard rail clearance to product.
•
Eliminate all catch points.
•
Check conveyor elevations.
•
All bolts and set screws tight.
•
Check product clearance to overhead structures.
•
Simulate all operational functions with actual product.
•
All guards in place with proper clearance.
•
All OSHA required guards in place on walkways, catwalks, ladder-ways, floor openings, etc.
•
All labels and warning signs in proper place, unobstructed.