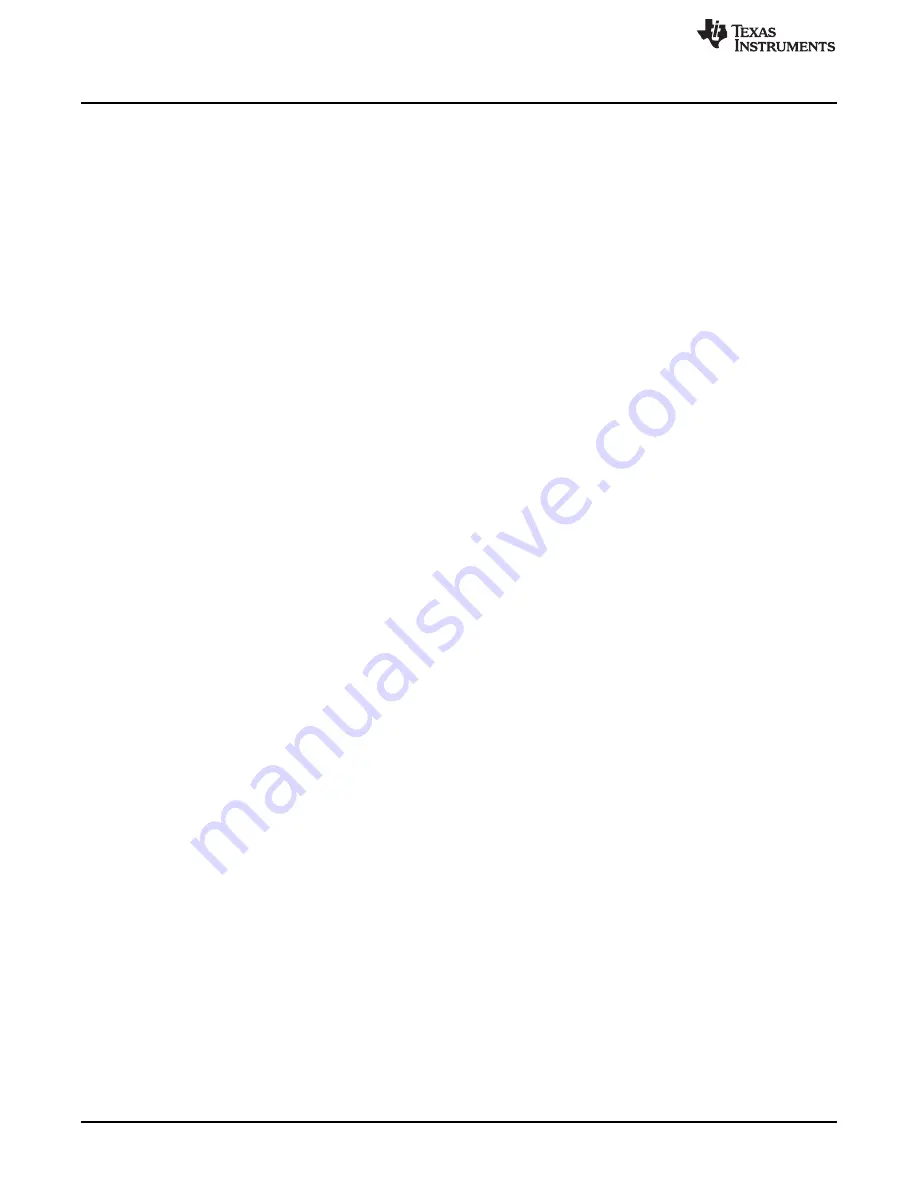
TAS54x4C Hardware Design Guidelines
1.10 EMI and PCB Layout Considerations
Electromagnetic interference (EMI) only relates to the TAS54x4C devices and the PCB layout. This
section also includes some discussion on the critical filtering component. Car manufacturers require a
strict electromagnetic compliance (EMC). Most manufacturers use the requirements for, or base their
requirements on the CISPR25 specification. The TAS54x4C devices can be part of a system that meets
these requirements. The devices already have many characteristics designed into them to eliminate the
emission of EMI. There are two types of tests for EMC emissions, conducted and radiated. Conducted
tests measure the EMI on the power and ground wires directly. Radiated test are performed with a series
of antennas.
1.10.1
PCB Layout Concerns
The PCB layout for the TAS54x4C devices must satisfy function, performance, and EMC. The devices
have the signal input and control pins on one side of the IC package and the output and power pins on the
other side to ease PCB layout.
A good ground plane is required for EMC and proper function of the TAS54x4C devices. All the GND pins
must be connected to the same ground plane. Preferably a ground plane should be on the top and bottom
of the PCB with many vias tying the two planes together. The ground plane should encase all of the traces
on the PCB so that the ground plane reaches all the edges of the PCB. Vias should be placed 10 mm
apart near the edge tying the ground plane together to create a Faraday cage.
For proper function all the bypass capacitors on the D_BYP, A_BYP, CP, and PVDD pins must be as
close to the pin as possible. The ground side of the bypass capacitors should be directly connected to the
ground plane. The bypass capacitors for PVDD should be connected to the ground plane close to the
GND pins to produce a low inductance path. The RC snubbers on the output pins should have the
corresponding ground connected to the ground plane as close the GND pins to improve the effect.
The best solution for EMC is to use a four-layer PCB with all the traces with high current or clocks on the
inner layers with vias to connect them to the parts. The outer layers are reserved for ground planes which
creates a Faraday cage around the whole PCB reducing the EMI emanated from the PCB.
1.11 Filtering
1.11.1
Power Supply Filtering
The power supply is tested for both conducted and radiated emissions. The first test is for conducted
emissions. If EMI is not conducted on the power wire, then it cannot radiate. On the TAS54xx device the
majority of the conducted EMI is
differential mode
. To remove differential mode EMI a series inductor with
a capacitor to ground is used. A second inductor in series can also be used for further reduction of
conducted EMI to form a
T
filter. The values for the inductors are from 10 µH to 40 µH. The capacitor
used is a parallel combination of two 4.7µ, 0.082µF, and 2.2nF capacitors. This combination extends the
effectiveness above 100 MHz. For
common mode
EMI a four layer PCB can be used. The two outside
layers are the ground plane with the power traces on one of the inner layers. The two ground layers are
connected together with many vias which forms a pseudo coaxial cable and blocks the common mode
EMI from entering the power traces.
1.11.2
Output Filtering
The outputs of the TAS54x4C devices have a large PWM waveform with a large current. These pins and
traces connected to the output pins produce the largest amount of EMI in the system. The EMI is
dominated by difference mode and therefore the LC filter described in the data sheet provides the most
reduction. The PCB traces between the TAS54xx device and the inductor in the LC filter must be as short
as possible. If a four-layer PCB is used, these traces should be on an inner layer with the ground plane on
the two outer layers. The previously described snubbers also reduce the EMI on these traces.
After each inductor, place two 470nF capacitors to ground for common mode EMI reduction. The ground
for these two capacitors should be at the same ground plane point. If they are not grounded at the same
point the common mode EMI reduction is decreased.
16
TAS54x4C Design Guide
SLOA196 – June 2014
Copyright © 2014, Texas Instruments Incorporated