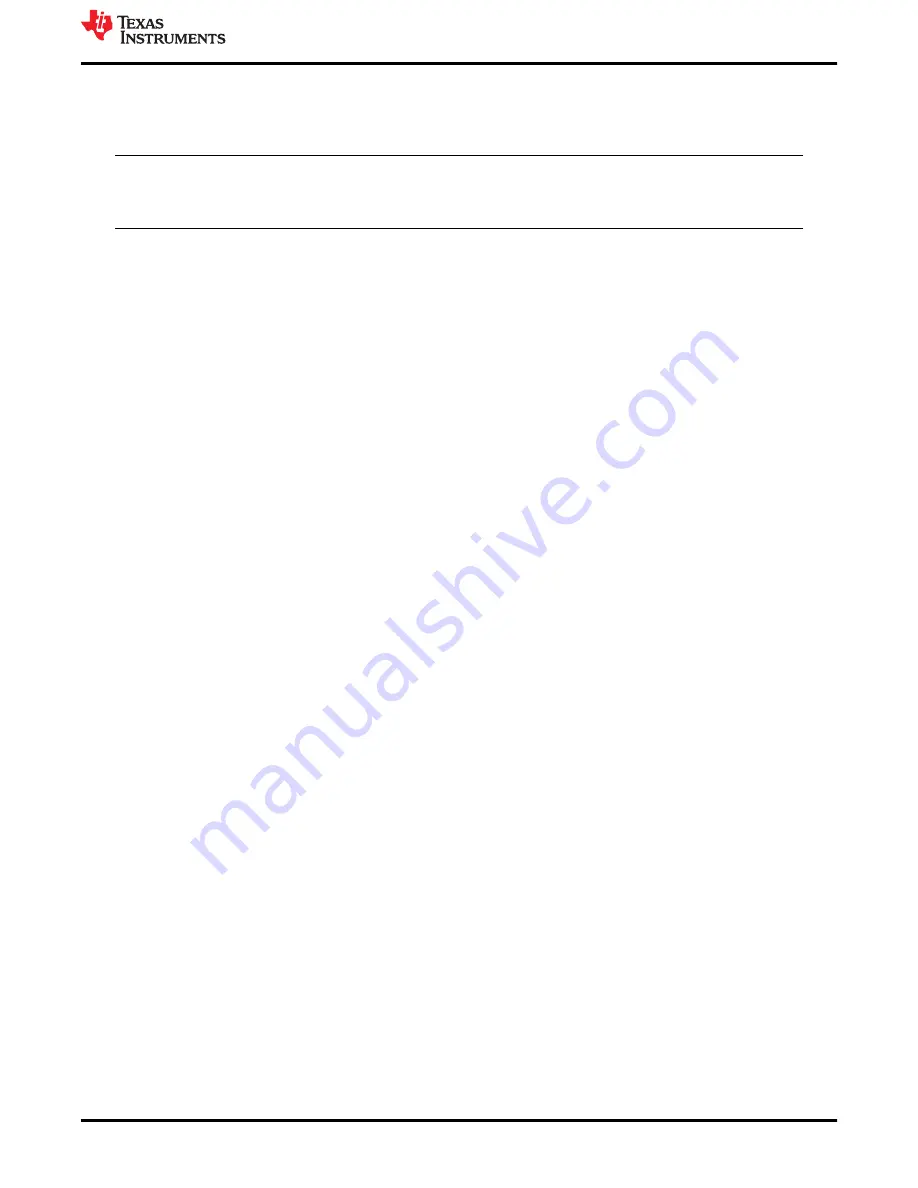
Step 1: Connect external crystal with frequency of 32.768kHz across pin 37 and 38.
Step 2: Configure pin 37 and 38 [PIN_36_37_CONFIG] as Pin 37 as X1 and Pin 38 as X2.
Step 3: Select Crystal Oscillator in Clock Source Select [CLK_SEL]
Note
Pin 36 and 37 can either be used as DACOUT1 and DACOUT2 for real time variable tracking or as X1
and X2 for external clock source. Both functionalities cannot be used together.
Option 2: External Clock
Step 1: Select External Clock input in Clock Source Select [CLK_SEL]
Step 2: Select external clock source frequency through External Clock configuration [EXT_CLK_CONFIG]
Note: Make sure to connect your external clock to pin 33.
Step 3: Enable External clock mode [EXT_CLK_EN]
4.2 System level configuration
4.2.1 Tracking motor speed feedback in real time
MCT8316A device provides information about the motor speed through the frequency generator (FG) pin,
which is also known as a TACH (tachometer) out. In MCT8316A, the FG pin behavior is configured through
FG_CONFIG. Configure FG_SEL to output FG signal only in closed loop, both open loop and closed loop, or
only in open loop for the first try. Configure FG_DIV to number of motor poles so that the FG output matches the
motor mechanical speed in Hz.
When FG_CONFIG is configured to 0 (FG active as long as motor is driven), the FG output is active as long as
MCT8316A is driving the motor. FG will not be active during a motor stop and coasting condition. In this mode,
FG is released high when MCT8316A enters sleep or standby mode. This mode is useful in applications that
require real time motor speed information as long as MCT8316A is driving the motor.
When FG_CONFIG is configured to 1 (FG active till BEMF drops below FG_BEMF_THR), MCT8316A provides
FG output until BEMF falls below FG_BEMF_THR. The FG output will continue to indicate motor speed even if
the motor is not being actively driven. This mode is useful in applications that require motor speed information
above a certain speed, and rotor motion information during the coast and braking conditions.
For example, if the motor Ke is 5 mV/Hz and the application require measuring motor speed above 4 Hz, then
the user can configure FG_BEMF_THR to 20 mV. Once when the motor speed reaches 4 Hz, the device will
output FG as the BEMF voltage will be 20 mV at 4 Hz.
4.2.2 Monitoring power supply voltage fluctuations for normal motor operation
In applications where the power supply may fluctuate, it is recommended to specify the minimum and maximum
power supply voltage range. During an undervoltage condition, the motor might operate at lower speeds. During
an overvoltage condition, the MOSFETs, MCT8316A and motor may be stressed with continued operation in
high voltage.
Step 1: Keep decreasing the supply voltage until we see a drop in the speed. Measure the bus voltage at
which the speed drops and set MIN_VM_MOTOR to that value. The range of minimum bus voltage that can be
configured is between 4.5V and 12.5V.
Step 2: Keep increasing the bus voltage to a point where the motor phase voltage reaches the maximum rated
voltage of the motor. MAX_VM_MOTOR will be the bus voltage at which motor phase voltage reaches the
maximum rated voltage of the motor. Range of maximum bus voltage that can be configured is between 20V and
35V.
Basic Controls
SLLU336 – MAY 2021
MCT8316A Tuning Guide
13
Copyright © 2021 Texas Instruments Incorporated