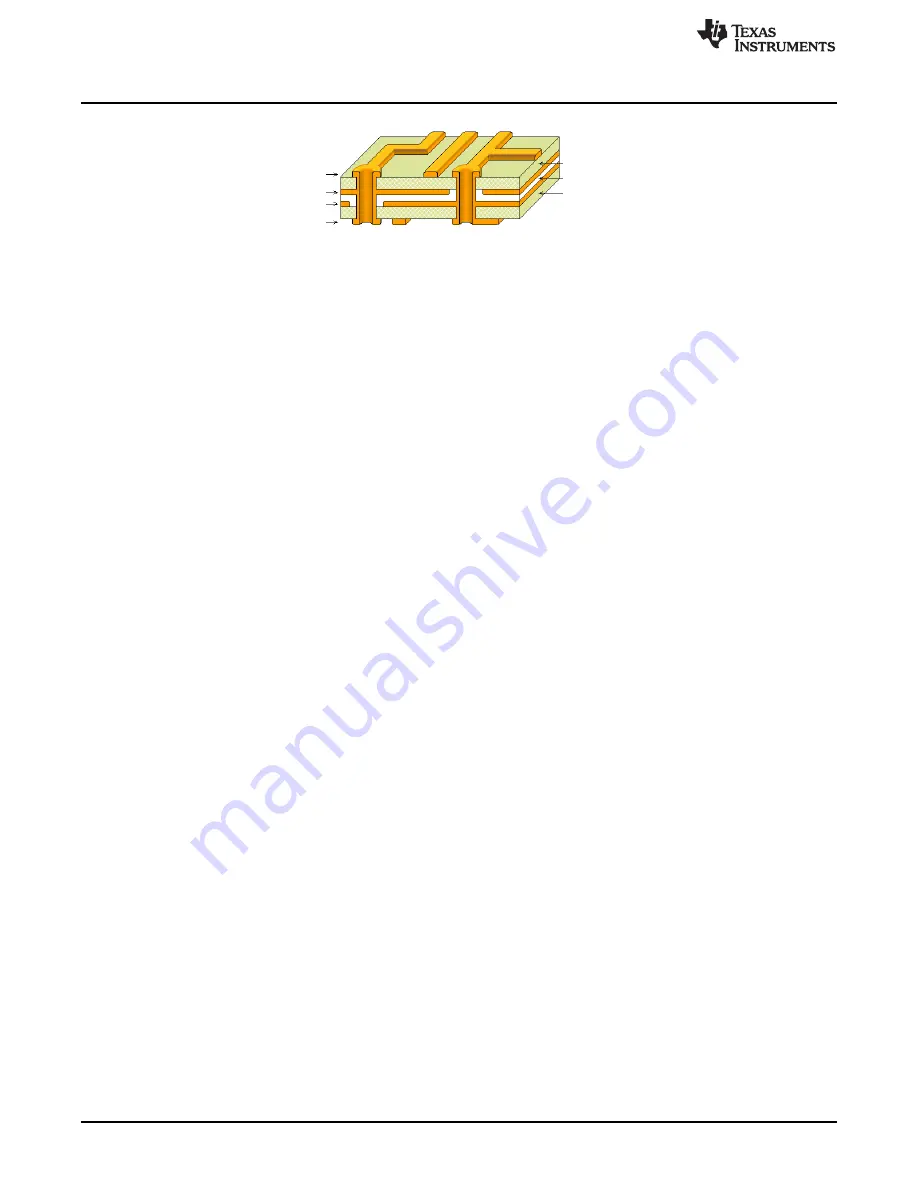
Prepreg
Core
Prepreg
Top Layer
Bottom Layer
PGND
GND
Start-Up of the EVM and Power Sequences
Figure 4. Evaluation Board Stackup
•
4-layer board FR4
•
Material thickness 1.616 ± 10% mm
•
Surface finish immersion gold
6
Start-Up of the EVM and Power Sequences
The LP8861-Q1 EVM is set up for easy start-up:
•
Connect LEDs to OUT1 - OUT4 of connector J16. (Note: LED current default is 100 mA and maximum
boost voltage default is 37 V. LED outputs that are not used must be grounded via jumpers J11 to
J14.)
•
Connect input (BATTERY) voltage 12 V to connector J25.
LEDs will turned on immediately because the jumpers on the EVM are set up for PWM input of 100% duty
cycle. For connector and jumper positions, see
and
Input (BATTERY) voltage range is 4.5 V to 40 V.
The LP8861-Q1 has a dual function VDDIO/EN pin. By default, VDDIO/EN = 3.3 V is generated
automatically on the EVM from battery input voltage via jumpers J1 and J26. VDDIO/EN acts as enable for
the device as well as supply/reference voltage for IO logic. Device starts when VIN voltage is present and
above the VIN UVLO voltage level (4 V), and the VDDIO/EN voltage is set above threshold voltage (1.2
V).
By default, boost switching frequency is 400 kHz (jumper J4 connecting R3 = 160 k
Ω
to FSET) and boost
maximum voltage is 37 V (R12 = 750 k
Ω
and R13 = 130 k
Ω
). See
and
for
description on how to change boost settings.
By default, LED current is 100 mA per string (jumper J5 connecting R4= 24 k
Ω
to ISET). See
for the description on how to change LED current setting.
Alternatively to internal LDO, device circuitry can be powered from external power supply (4.4 V to 5.25 V)
connected to the LDO pin. Internal LDO will be disabled in this case.
6.1
PWM Input to Initiate Start-up Sequence
The backlight is started by setting PWM input high. By default, the LP8861-Q1EVM has PWM input set
high (100% duty cycle), which is connected to VDDIO through jumper J2. Alternatively, an external PWM
signal can be connected by removing jumper J2 , shorting pins 3 and 4 on jumper J17, and connecting the
external PWM to connector J18.
8
LP8861-Q1EVM Evaluation Module
SNVU456 – July 2015
Copyright © 2015, Texas Instruments Incorporated