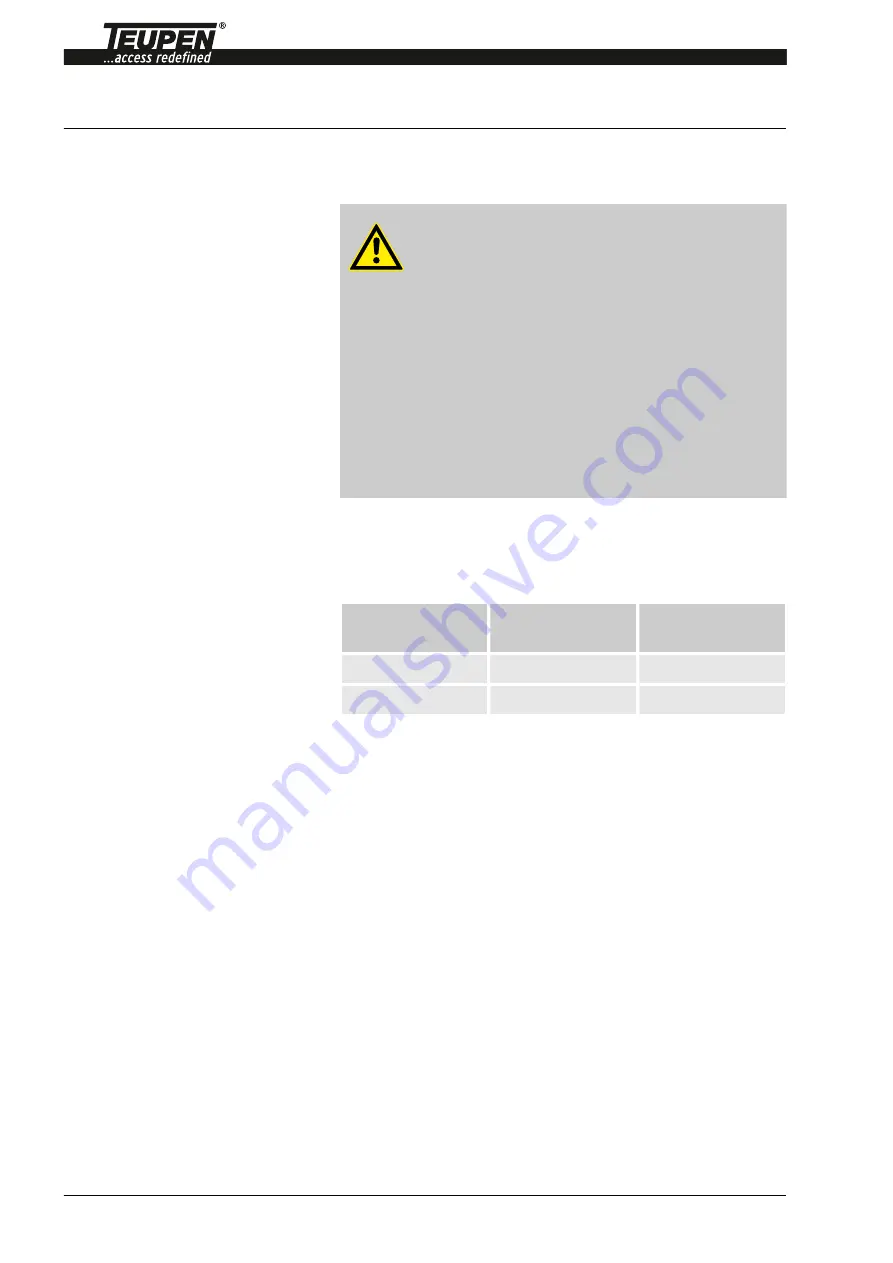
7.3.8
Rotating assembly tightening torques
WARNING!
Danger due to incorrect tightening tor-
ques!
If screws are tightened with the incorrect
tightening torque, components can come
loose and cause personal injury and property
damage.
– Never exceed the maximum allowable
tightening torque.
– Check the tightening torques regularly.
– Always heed the relevant guidelines and
design criteria for screw connections.
The table shows the required tightening torques for ach-
ieving the most reliable initial tension for the screws of
the rotating assembly.
Screw size
Screw quality
Tightening
torque
M 12
10.9
110 Nm
M16
10.9
270 Nm
Maintenance
13.02.2013
Aerial access platform Leo15GT 2012
120
Summary of Contents for LEO 15 GT
Page 12: ...General 13 02 2013 Aerial access platform Leo15GT 2012 12 ...
Page 37: ...3914 0095 3914 0021 3914 0054 3914 0021 3914 0053 ...
Page 39: ......
Page 58: ...Structure and function 13 02 2013 Aerial access platform Leo15GT 2012 54 ...
Page 66: ...Transport and storage 13 02 2013 Aerial access platform Leo15GT 2012 62 ...
Page 106: ...Operation 13 02 2013 Aerial access platform Leo15GT 2012 102 ...
Page 145: ...Appendix Appendix 13 02 2013 Aerial access platform Leo15GT 2012 141 ...
Page 146: ...Appendix 13 02 2013 Aerial access platform Leo15GT 2012 142 ...
Page 148: ...Appendix 13 02 2013 Aerial access platform Leo15GT 2012 144 ...
Page 149: ...A Combustion engine Combustion engine 13 02 2013 Aerial access platform Leo15GT 2012 145 ...
Page 150: ...Combustion engine 13 02 2013 Aerial access platform Leo15GT 2012 146 ...
Page 152: ...Combustion engine 13 02 2013 Aerial access platform Leo15GT 2012 148 ...
Page 166: ...Combustion engine 13 02 2013 Aerial access platform Leo15GT 2012 162 ...
Page 167: ...INSTRUCTION BOOK 43380207 ENG 10 05 3 Printed in Germany 33 1B20 1B27 1B30 1B40 1B50 ...
Page 204: ......
Page 205: ...B Circuit diagram Circuit diagram 13 02 2013 Aerial access platform Leo15GT 2012 201 ...
Page 206: ...Circuit diagram 13 02 2013 Aerial access platform Leo15GT 2012 202 ...
Page 207: ...C Hydraulic plan Hydraulic plan 13 02 2013 Aerial access platform Leo15GT 2012 203 ...
Page 208: ...Hydraulic plan 13 02 2013 Aerial access platform Leo15GT 2012 204 ...