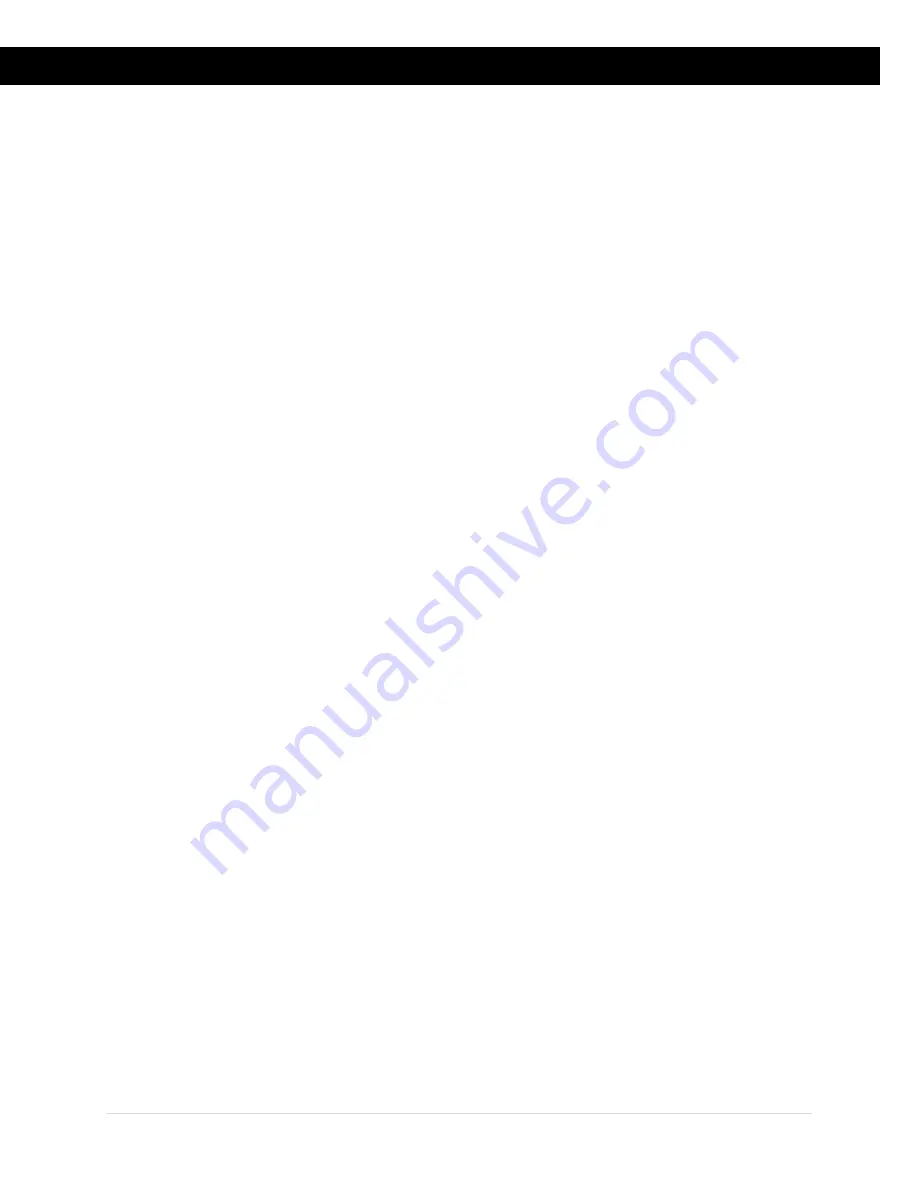
38 |
P a g e
USER MAINTENANCE
D
OOR
C
OMPONENTS AND
S
EAL
Periodically, inspect the door latch, trim, and catch for alignment. Check the chamber liner gasket
located on the oven door frame at least once per year for signs of fraying, brittleness, or tearing.
Failure to maintain the integrity of the door system shortens the lifespan of the oven and may
adversely impact chamber temperature uniformity and stability.
E
LECTRICAL
C
OMPONENTS
Electrical components do not require maintenance. If the unit electrical systems fail to operate as
specified, please contact your distributor or Technical Support for assistance.
Summary of Contents for FOV Series
Page 2: ...2 P a g e This page left blank...
Page 18: ...18 P a g e INSTALLATION This page left blank...
Page 43: ......