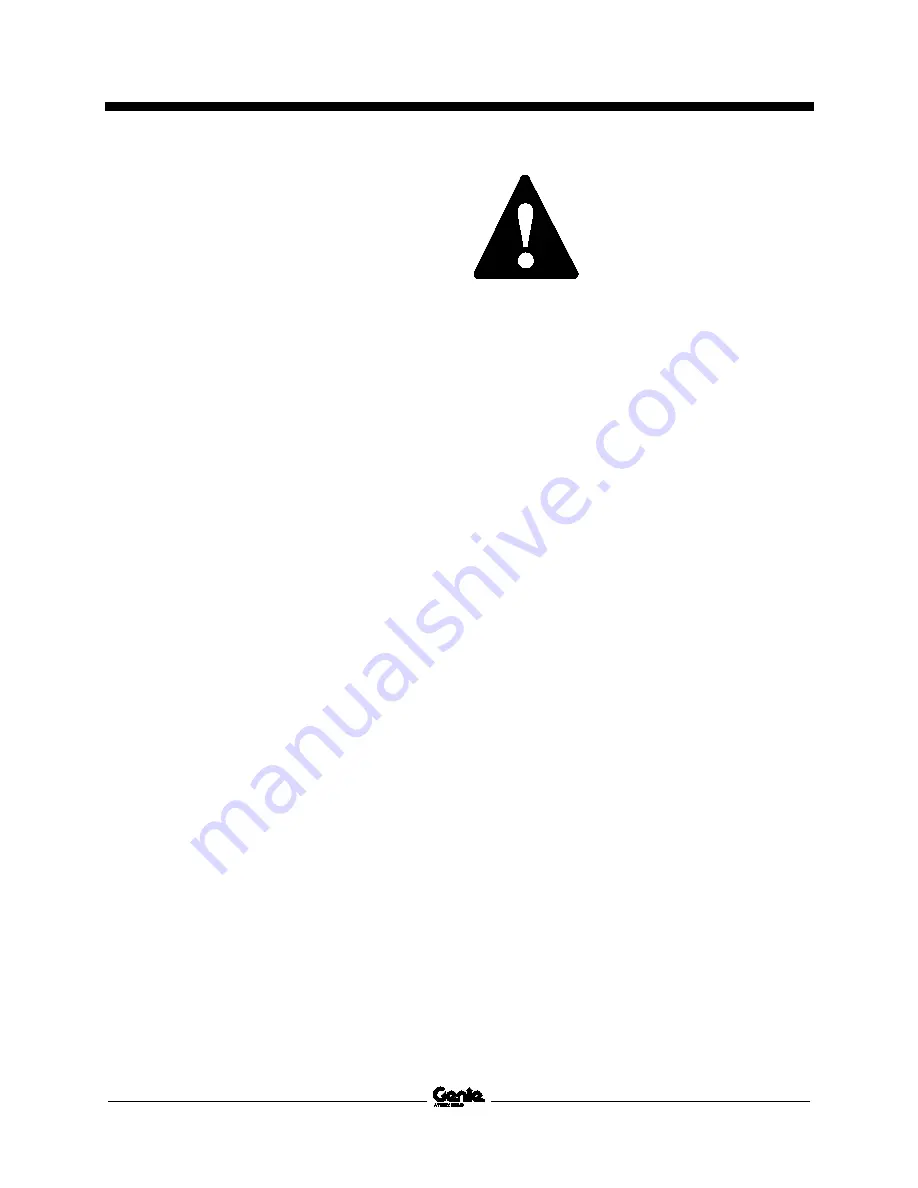
Service Manual
May 2015
Safety Rules
vi
GS-2669 BE • GS-3369 BE • GS-4069 BE
Part No. 1257106
Section 1
Safety R ules
Danger
Failure to obey the instructions and safety rules in
this manual and the appropriate Operator's Manual
on your machine will result in death or serious
injury.
Many of the hazards identified in the operator's
manual are also safety hazards when maintenance
and repair procedures are performed.
Do Not Perform Maintenance
Unless:
You are trained and qualified to perform
maintenance on this machine.
You read, understand and obey:
•
manufacturer's instructions and safety rules
•
employer's safety rules and worksite
regulations
•
applicable governmental regulations
You have the appropriate tools, lifting
equipment and a suitable workshop.
Summary of Contents for Genie GS-2669 BE
Page 1: ...Service Manual GS 2669 BE GS 3369 BE GS 4069 BE Part No 1257106 Rev A3 May 2015...
Page 27: ...May 2015 Service Manual Specifications Part No 1257106 GS 2669 BE GS 3369 BE GS 4069 BE 11...
Page 100: ...Service Manual May 2015 Manifolds 84 GS 2669 BE GS 3369 BE GS 4069 BE Part No 1257106...
Page 173: ...May 2015 Service Manual 157 Contactor Box Layout All Models...
Page 176: ...Service Manual May 2015 160 Ground Control Box Layout All Models...
Page 177: ...May 2015 Service Manual 161 Platform Control Box Layout All Models...
Page 180: ...Service Manual May 2015 164 Generator Wiring Diagram All Models...
Page 185: ...May 2015 Service Manual 169 Electrical Schematic GS 4069 BE with 2 Speed Lift ANSI CSA...
Page 188: ...Service Manual May 2015 172 Electrical Schematic GS 4069 BE with Proportional Lift ANSI CSA...
Page 193: ...May 2015 Service Manual 177 Electrical Schematic GS 4069 BE with 2 Speed Lift AS CE...
Page 196: ...Service Manual May 2015 180 Electrical Schematic GS 4069 BE with Proportional Lift AS CE...
Page 197: ...May 2015 Service Manual 181 Hydraulic Schematic GS 2669 BE and GS 3369 BE with 2 Speed Lift...
Page 201: ...May 2015 Service Manual 185 Hydraulic Schematic GS 4069 BE with 2 Speed Lift...
Page 205: ......