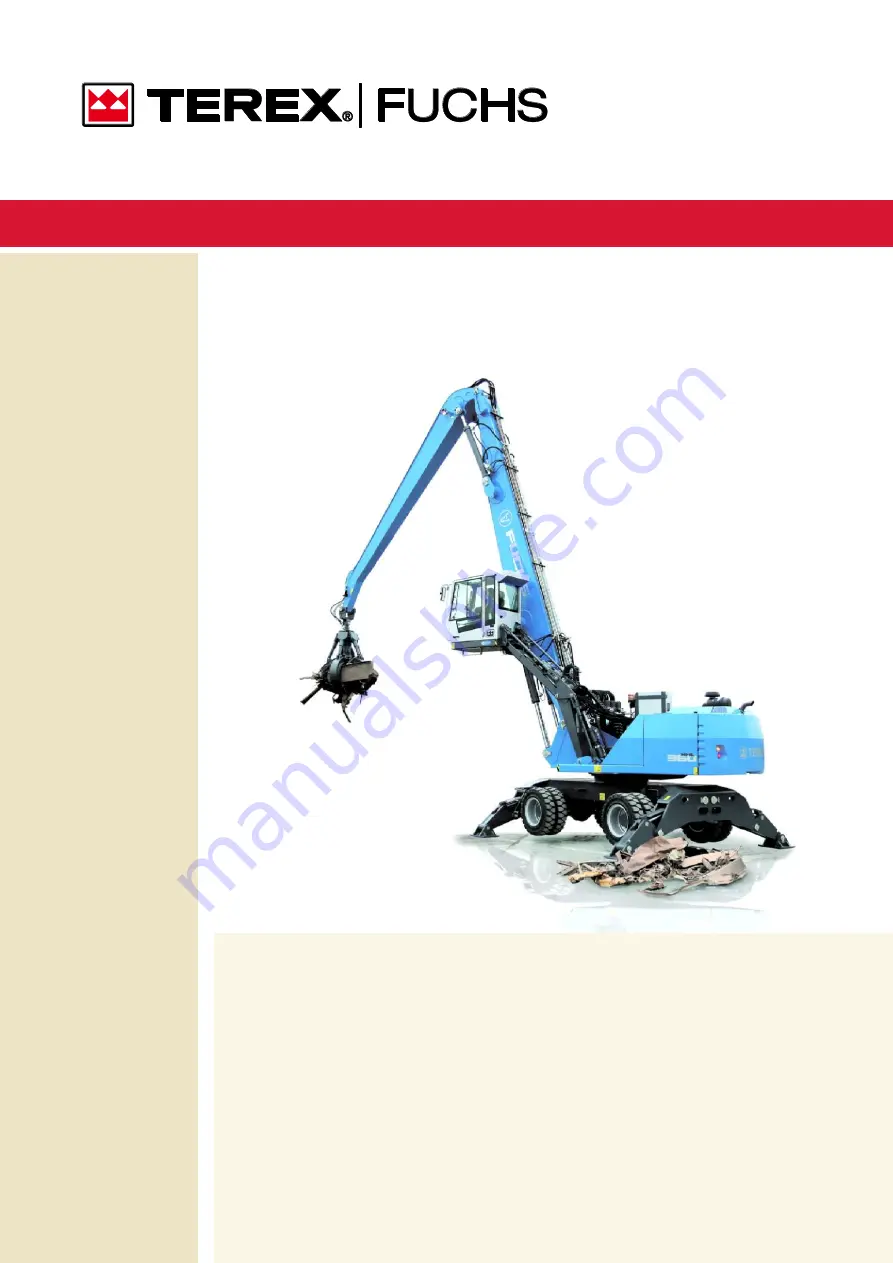
Operating Instructions
MHL360
E
BSB50000
Mobile hydraulic loading machine
MHL360 E
Vehicle ID no. starting
Year of manufacture starting
Version
17.07.2014 en
(englisch)
Original operating instructions
Operating Instructions
MHL360
E
BSB50000
Mobile hydraulic loading machine
MHL360 E
Vehicle ID no. starting
Year of manufacture starting
Version
17.07.2014 en
(englisch)
Original operating instructions