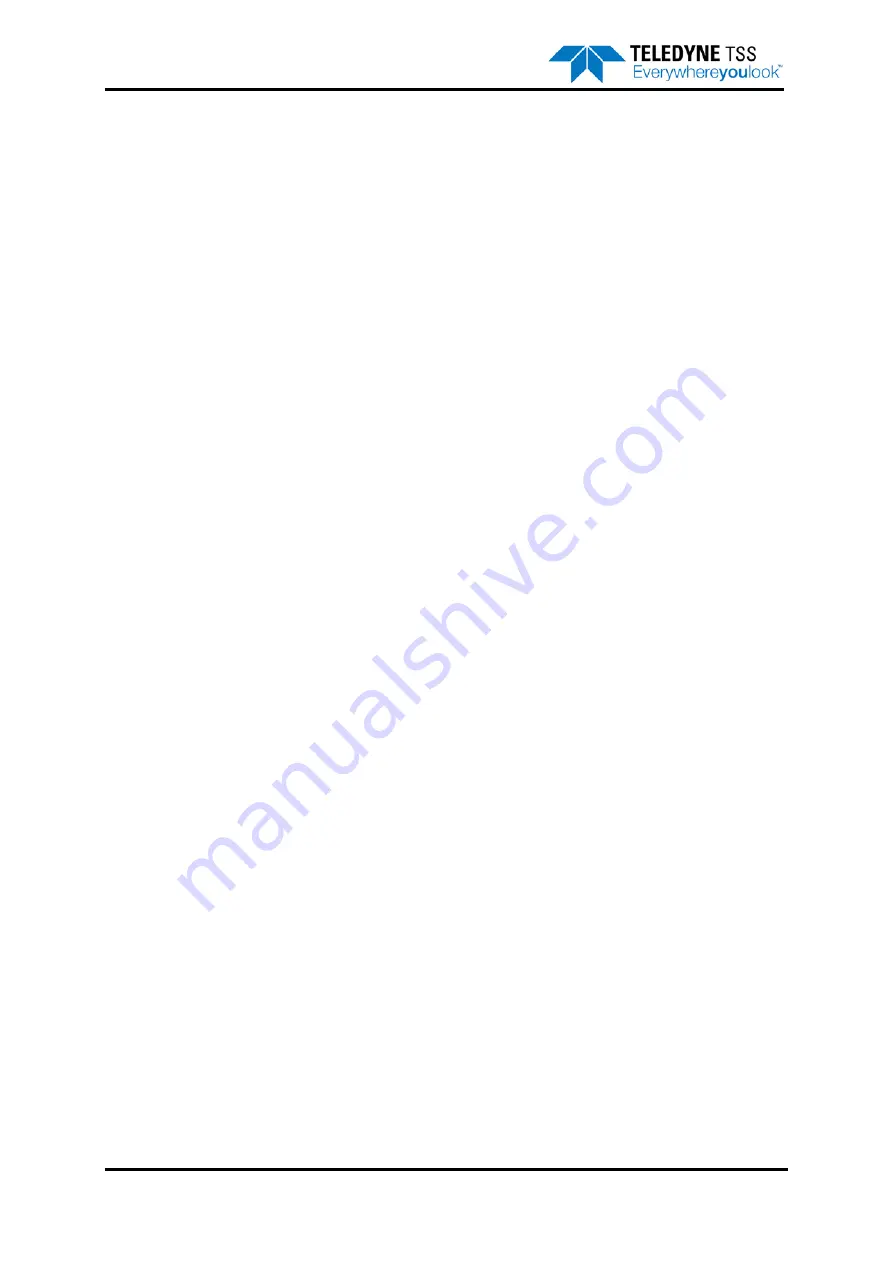
9 – Maintenance
9-8
© Teledyne TSS
DPN 402196 Issue 4.1
To remove any of the boards:
❐
Note their positions and carefully disconnect all the plugs and connectors that link the board to
the main assembly.
❐
Use the 3mm hexagonal key to remove the M4 × 16mm bolts that secure the board to the sup-
port and remove the board from the assembly.
❐
On completion of repair work refit the board and reconnect the cables and connectors cor-
rectly.
Reassemble the SEP:
12. Check the condition of the two rubber O-rings that seal each of the end-caps. Clean or renew
them if necessary. Apply a thin smear of approved lubricant to the rings to ensure they make
an efficient seal when you reassemble the SEP. For this purpose, use the same type of lubri-
cant that you use for the sub-sea electrical connectors – see
section 4.1.2 "Care of Sub-sea
for these important instructions.
13. Place the desiccant pack inside so that it fits between the Main Board and the SEP housing.
Make certain that there are no trapped wires or components, and push the end-cap home. This
end-cap must be opposite the end of the SEP that has the ground strap attached inside.
14. Carefully align the end-cap to the SEP housing so that the four securing screws will engage
properly. If necessary, turn the end-cap slightly to achieve perfect alignment. Ensure that both
holes for the grub screws align with the hardened stainless steel inserts on the end of the SEP
housing.
15. Insert the four M4 × 16mm A4 stainless steel screws and use the 3mm hexagonal key to
tighten them evenly. Insert both grub-screws and tighten them lightly.
16. Reconnect the ground wires, the 8-way and the 6-way connectors on the ‘Power/Comms’ end-
cap. Make certain both locking clips on each of the multi-way connectors engage properly.
17. Align and engage the ‘Power/Comms’ end-cap into the SEP housing. Make certain both holes
for the grub screws align with the hardened stainless steel inserts in the end of the SEP hous-
ing.
18. Make certain there are no trapped wires and press the end-cap home. If necessary, twist the
end-cap slightly to achieve perfect alignment of the screw holes. As you replace the end-cap,
the SEP housing may become slightly pressurised which may make the cap difficult to replace.
Do not apply excessive force
.
19. Insert the four M4 × 16mm A4 stainless steel screws and use the 3mm hexagonal key to
tighten them evenly. Insert both grub-screws and tighten them lightly.
9.2.2.2 Power Supply Pod
Neither of the PSU end-caps has an obvious point of reference to use for orientation when you
reassemble the pod.
Remove the end-cap that has the moulded cable attached:
1.
Jack the end-cap off the housing by following the same procedure described above for the
SEP. Note that a partial vacuum may form inside the PSU as you remove the end-cap and this
may make removal difficult.
Do not insert any hard or sharp instruments into the gap to
act as a lever
.
Summary of Contents for 440
Page 12: ...List of Figures x Teledyne TSS DPN 402196 Issue 4 1 ...
Page 18: ...Glossary xvi Teledyne TSS DPN 402196 Issue 4 1 ...
Page 24: ...1 Introduction 1 6 Teledyne TSS DPN 402196 Issue 4 1 ...
Page 32: ...2 System Overview 2 8 Teledyne TSS DPN 402196 Issue 4 1 ...
Page 66: ...4 Electrical Installation 4 20 Teledyne TSS DPN 402196 Issue 4 1 ...
Page 88: ...5 Operating Software 5 22 Teledyne TSS DPN 402196 Issue 4 1 Figure 5 10 Altimeter Test ...
Page 144: ...6 Operating Procedure 6 40 Teledyne TSS DPN 402196 Issue 4 1 ...
Page 154: ...7 Operational Considerations 7 10 Teledyne TSS DPN 402196 Issue 4 1 ...
Page 164: ...8 System Specifications 8 10 Teledyne TSS DPN 402196 Issue 4 1 ...
Page 203: ...10 System Drawings DPN 402196 Issue 4 1 Teledyne TSS 10 17 Figure 10 15 SDC10 Dimensions ...
Page 230: ...A Operating Theory A 12 Teledyne TSS DPN 402196 Issue 4 1 ...
Page 242: ...B Options B 12 Teledyne TSS DPN 402196 Issue 4 1 ...
Page 244: ...C Altimeter C 2 Teledyne TSS DPN 402196 Issue 4 1 ...
Page 246: ...D Reference D 2 Teledyne TSS DPN 402196 Issue 4 1 ...
Page 248: ...D Reference D 4 Teledyne TSS DPN 402196 Issue 4 1 ...
Page 250: ...D Reference D 6 Teledyne TSS DPN 402196 Issue 4 1 ...
Page 252: ...D Reference D 8 Teledyne TSS DPN 402196 Issue 4 1 ...
Page 254: ...D Reference D 10 Teledyne TSS DPN 402196 Issue 4 1 ...