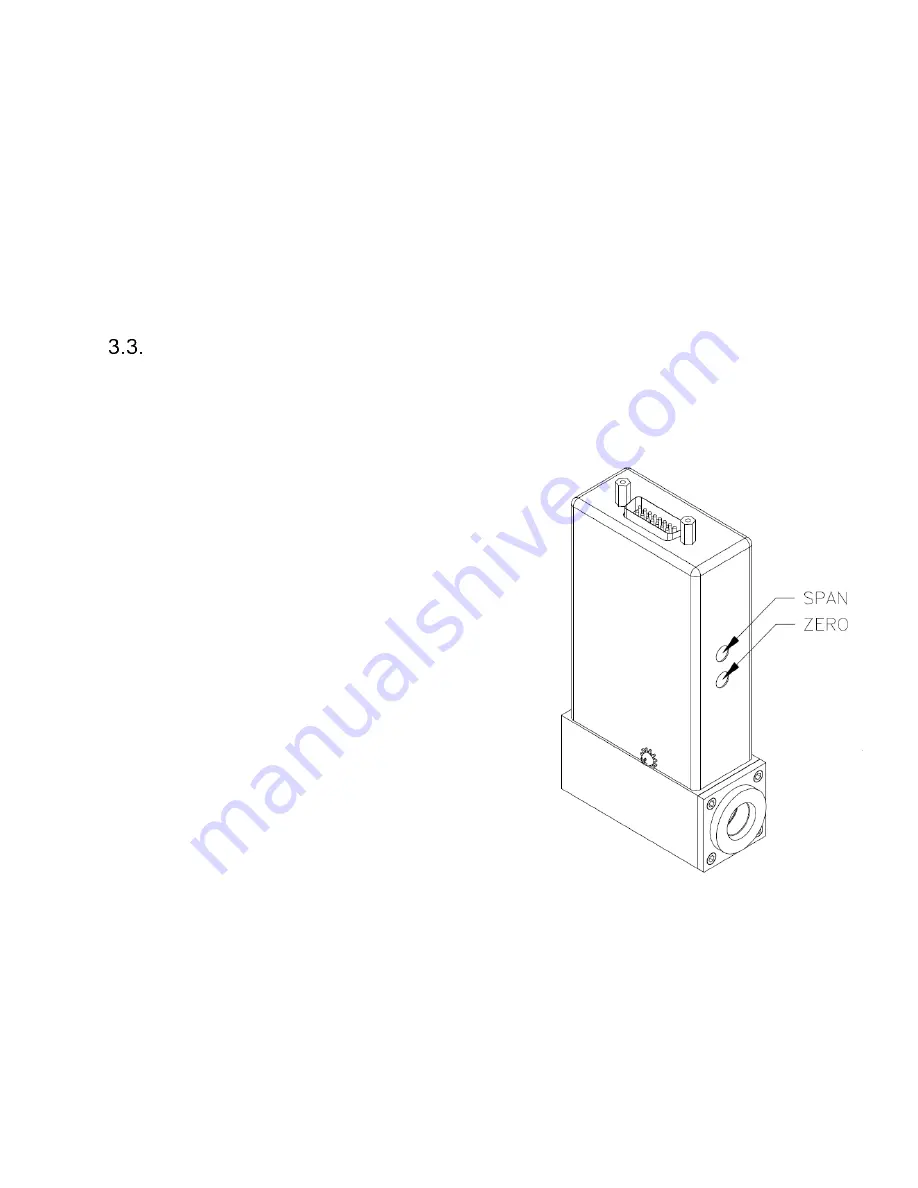
200/202 Series Flowmeters and Controllers Instruction Manual
EAR99 Technology Subject to Restrictions Contained on the Cover Page
Page 22 of 27
CAUSE:
Plugged orifice.
ACTION:
Verify the presence of a 10-50 psig pressure across the instrument. If present, shut off gas
supply and power supply. Remove orifice per Section 3.7. Examine orifice. If plugged, clean or replace
as applicable. Reassemble valve.
SYMPTOM:
Flow meter reads other than 0.00 VDC with no flow, or there is a small flow when flow
meter reads 0.00 VDC.
CAUSE:
ZERO potentiometer is out of adjustment.
ACTION:
Shut off all flow. Adjust ZERO potentiometer until output reads 0.00 VDC.
SYMPTOM:
Flow meter out of calibration and nonlinear.
CAUSE:
Leaks in gas inlet or outlet fittings.
ACTION:
Check all fittings for leaks by placing soap solution on all fittings between gas supply and final
destination of gas. Check flow meter for leaks. Replace “O” rings
if required or recalibrate as necessary.
Adjustments
The following sections detail adjustments that can be made to a Hastings flow instrument’s calibration. The
process of making these adjustments is only recommended if appropriate calibration equipment is available,
such as the appropriate leak-tight fittings and a formidable flow reference.
3.3.1.
Calibration Procedure (controller)
NOTE: Steps 5 and 6, adjusting the SPAN pot and
performing a calibration run, will require the use of a
calibration reference.
1)
Connect power to the instrument, put in AUTO
state, and allow 10% flow for 30 minutes as a
warm-up.
2)
After the warm-up period, set the flow to zero and
wait for 2 minutes. Check to make sure there is
zero flow.
3)
Adjust the ZERO potentiometer (bottom hole on
inlet side) so that the flow instrument outputs
0.000 VDC (6,5 on 15V, 2,8 on 24V).
4)
Override the valve closed or give a 0% flow
command. Turn on gas supply to inlet of
instrument. Adjust the orifice underneath the
controller to obtain zero flow.
5)
Set the flow to 100% (don’t forget to put the valve
state back into AUTO if you closed it in step 4) and
Ensure that full range flow can still be obtained at
minimum inlet pressure.
6)
NOTE 1:
Controllers regulate flow to the analog command given. If a user commands 5 volts, the
controller will move the valve to indicate 5 volts of flow regardless of how the span pot is set. If
users keep turning the span pot, the controller will continue to regulate to 5 volts as long as the
valve can physically pass the flow needed to get there.
NOTE 2:
Users need a flow reference in series with the controller to tell exactly what flow rate is
passing at the controller
’
s full scale. Set the command to 100%. Adjust the SPAN potentiometer (top
hole on inlet side, usually under a sticker) until the flow controller full scale (5.000 VDC) matches the
desired flow rate indicated by the flow reference.
7)
Record flow controller and flow reference outputs for flow rates of 20%, 40%, 60%, 80% and 100%.
Take the data and make sure the output is within ±1% of full scale at each point (accuracy spec).