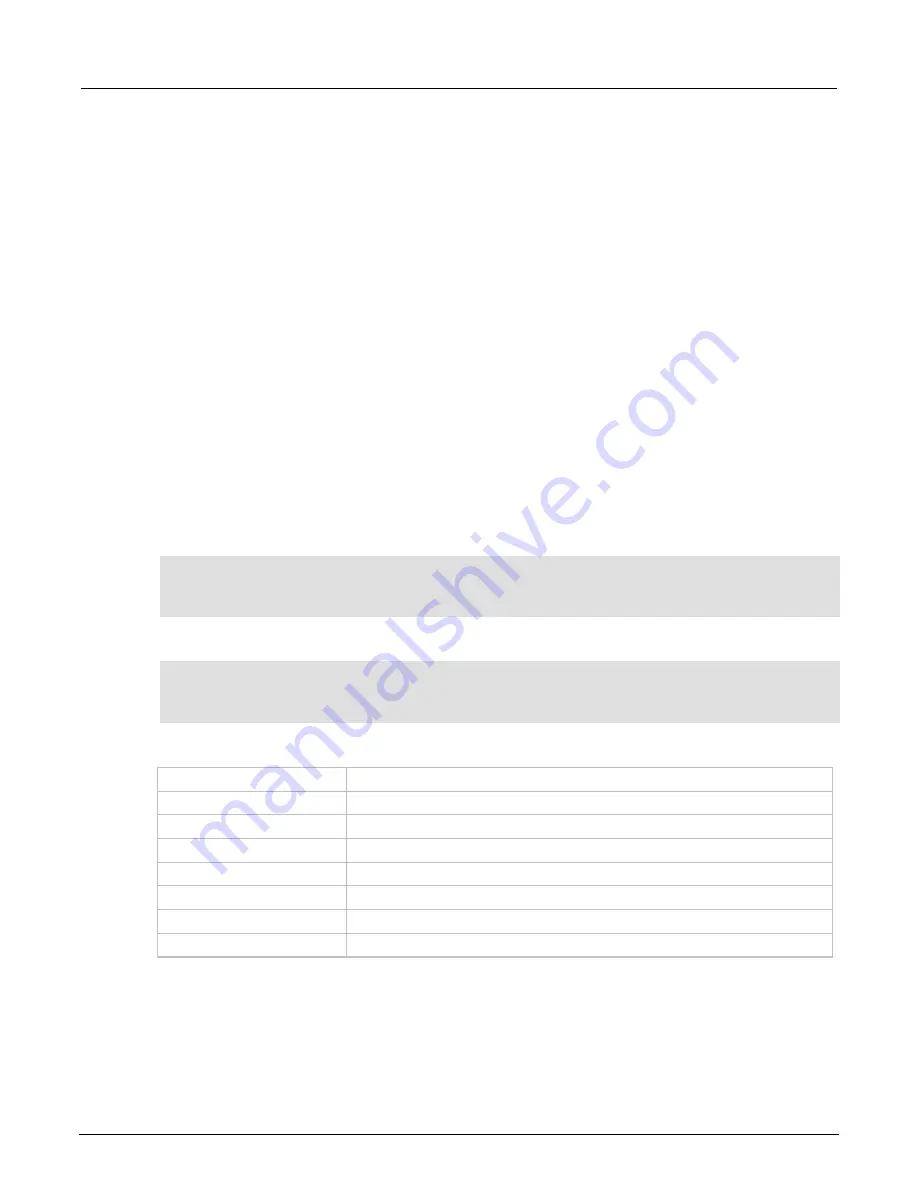
Model DMM7510 7½ Digit Multimeter Application Manual
Section 5: Grading and binning resistors
DMM7510-904-01 Rev. D March 2021
5-3
If a resistor passes the 20% limit test, the resistance value is checked against limit 2, which is the
10% limit value. If the resistor fails this limit inspection, the resistance is outside of the 10% tolerance
band. The trigger model outputs the limit 2 fail pattern, which causes the component handler to place
the resistor in the limit 2 fail bin (10% fail bin).
If a resistor passes the 10% limit test, the resistance value is checked against limit 3, which is the 5%
limit value, and so on. If a resistor passes all the limit tests, the trigger model outputs the overall pass
bit pattern, which causes the component handler to place the resistor in the all pass bin.
For this example, the same fail pattern is assigned to both the lower and upper bounds of the limits.
Therefore, a fail bin contains resistance values in the range (Resistance
− Percentage to
Resi Percentage). The percentage is 20, 10, 5, or 1. You can assign different bit patterns for
different limit values.
Trigger-model template: GradeBinning
The GradeBinning trigger-model template contains the settings for the number of components, digital
I/O, and limits. The command parameters for the template are described in the following commands
and table.
SCPI command usage:
:TRIGger:LOAD "GradeBinning", <components>, <startInLine>, <startDelay>, <endDelay>,
<limit1High>, <limit1Low>, <limit1Pattern>, <allPattern>, <limit2High>,
<limit2Low>, <limit2Pattern>, <limit3High>, <limit3Low>, <limit3Pattern>,
<limit4High>, <limit4Low>, <limit4Pattern>, "<bufferName>"
TSP command usage:
trigger.model.load("GradeBinning",
components
,
startInLine
,
startDelay
,
endDelay,
limit1High
,
limit1Low
,
limit1Pattern
,
allPattern
,
limit2High
,
limit2Low
,
limit2Pattern
,
limit3High
,
limit3Low
,
limit3Pattern
,
limit4High
,
limit4Low
,
limit4Pattern
,
bufferName
)
Parameter list
components
100
startInLine
Digital I/O line 5
startDelay
100 ms
endDelay
100 ms
limit1High
Resistance = 100
Ω, Percentage = 20%, 100 + 20% = 120 Ω
limit1Low
Resistance = 100
Ω, Percentage = 20%, 100
−
20% = 80
Ω
limit1Pattern
Bin 1 fail pattern 15: Drive all digital I/O lines high (1111)
allPattern
All pass pattern 4: Drive line 3 high (0100)