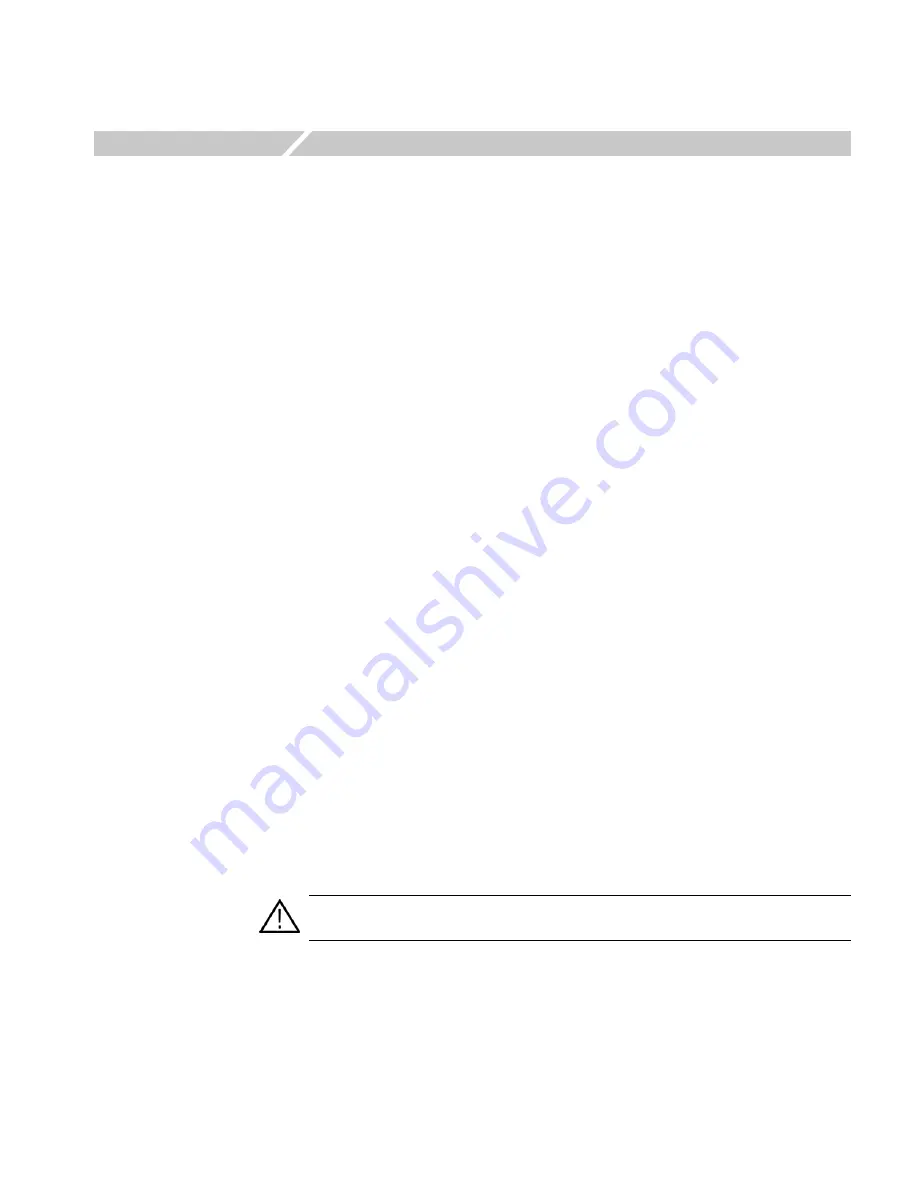
AWG7000 Series Service Manual
4-1
Maintenance
This section contains information needed to do periodic and corrective
maintenance on the instrument. The following subsections are included:
Preparation
— Tells you how to get ready to do arbitrary waveform generator
maintenance.
Preparation Preventing ESD
— Provides general information on preventing
damage to internal modules when doing maintenance.
Inspection and Cleaning
— Information and procedures for inspecting the
instrument and cleaning its external and internal modules.
Removal and Installation Procedures
— Procedures for the removal of
defective modules and replacement of new or repaired modules.
Toubleshooting
— Information for isolating failed modules. Included are
instructions for operating the instrument diagnostic routines and
troubleshooting trees. Most of the trees make use of the internal diagnostic
routines to speed fault isolation to a module.
Preparation
Only qualified persons should perform service procedures. Before performing any
service procedures, read the
Service Safety Summary
and
General Safety Summary
at the front of this manual and the ESD information below. Also refer to the
Operating Information section and your arbitrary waveform generator quick start
user manual for information about using the arbitrary waveform generator.
Preventing ESD
When performing any service that requires internal access to this instrument,
adhere to the following precautions to avoid damaging internal modules and their
components due to electrostatic discharge (ESD).
Minimize handling of static-sensitive modules.
Transport and store static-sensitive modules in their static protected containers
or on a metal rail. Label any package that contains static-sensitive modules.
CAUTION.
Static discharge can damage any semiconductor component in this
instrument.
Summary of Contents for AWG7000 Series
Page 4: ......
Page 10: ...List of Tables vi AWG7000 Series Service Manual...
Page 14: ...Service Safety Summary x AWG7000 Series Service Manual...
Page 16: ...Environmental Considerations xii AWG7000 Series Service Manual...
Page 18: ...Preface xiv AWG7000 Series Service Manual...
Page 19: ...Operating Information...
Page 20: ......
Page 23: ...Theory of Operation...
Page 24: ......
Page 31: ...Adjustment Procedures...
Page 32: ......
Page 51: ...Maintenance...
Page 52: ......
Page 58: ...Maintenance 4 6 AWG7000 Series Service Manual...
Page 109: ...Replaceable Parts...
Page 110: ......