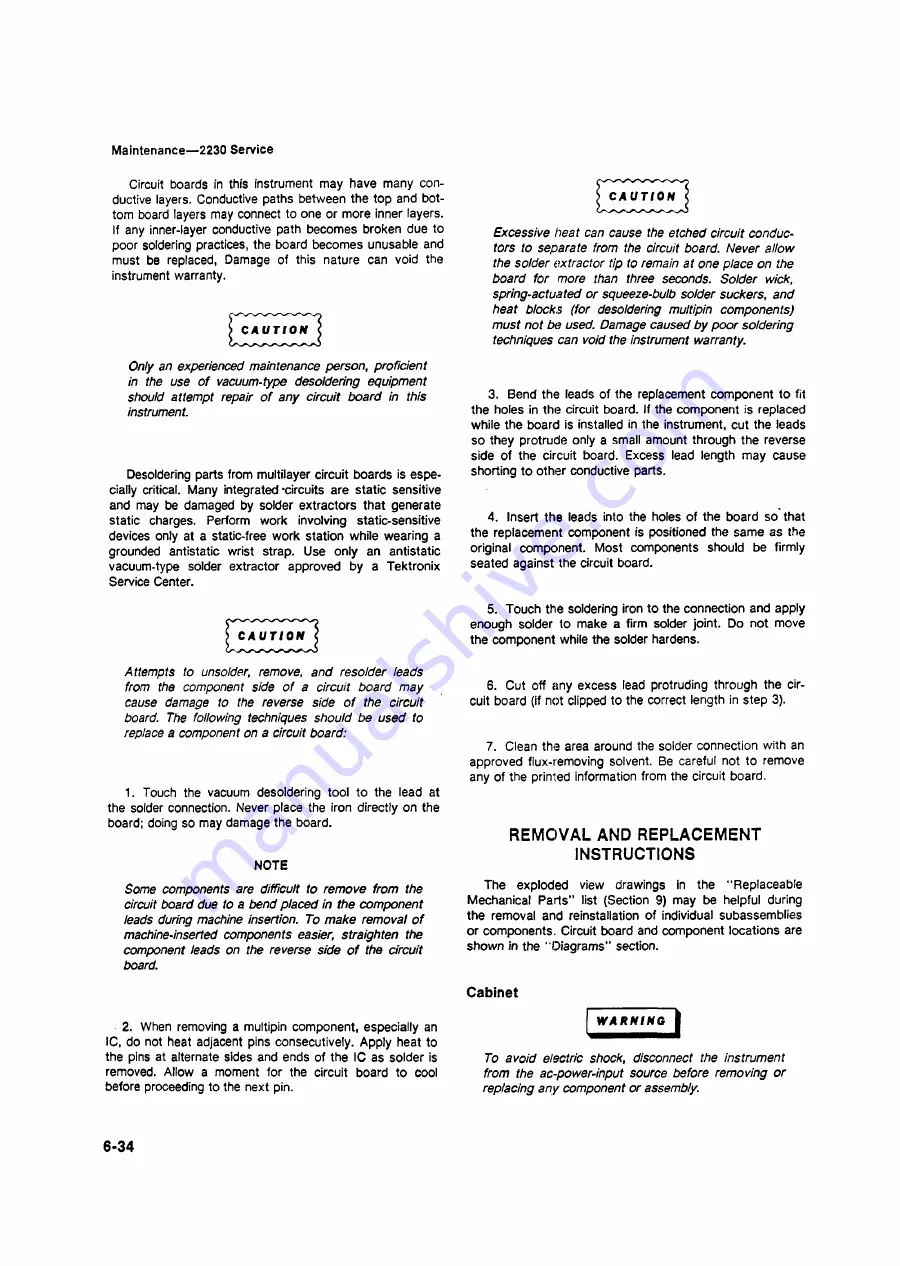
Maintenance— 2230 Service
Circuit boards in this instrument may have many con
ductive layers. Conductive paths between the top and bot
tom board layers may connect to one or more inner layers.
If any inner-layer conductive path becomes broken due to
poor soldering practices, the board becomes unusable and
must be replaced, Damage of this nature can void the
instrument warranty.
>
C A U T I O N (
Only an experienced maintenance person, proficient
in the use of vacuum-type desoldering equipment
should attempt repair of any circuit board in this
instrument.
Desoldering parts from multilayer circuit boards is espe
cially critical. Many integrated‘circuits are static sensitive
and may be damaged by solder extractors that generate
static charges. Perform work involving static-sensitive
devices only at a static-free work station while wearing a
grounded antistatic wrist strap. Use only an antistatic
vacuum-type solder extractor approved by a Tektronix
Service Center.
) C A U T I O N
I
Attempts to unsolder, remove, and resolder leads
from the component side of a circuit board may
cause damage to the reverse side of the circuit
board. The following techniques should be used to
replace a component on a circuit board:
1.
Touch the vacuum desoldering tool to the lead at
the solder connection. Never place the iron directly on the
board; doing so may damage the board.
NOTE
Some components are difficult to remove from the
circuit board due to a bend placed in the component
leads during machine insertion. To make removal of
machine-inserted components easier, straighten the
component leads on the reverse side of the circuit
board.
2.
When removing a multipin component, especially an
1C, do not heat adjacent pins consecutively. Apply heat to
the pins at alternate sides and ends of the 1C as solder is
removed. Allow a moment for the circuit board to cool
before proceeding to the next pin.
) C A U T I O N
<
Excessive heat can cause the etched circuit conduc
tors to separate from the circuit board. Never allow
the solder extractor tip to remain at one place on the
board for more than three seconds. Solder wick,
spring-actuated or squeeze-bulb solder suckers, and
heat blocks (for desoldering multipin components)
must not be used. Damage caused by poor soldering
techniques can void the instrument warranty.
3.
Bend the leads of the replacement component to fit
the holes in the circuit board. If the component is replaced
while the board is installed in the instrument, cut the leads
so they protrude only a small amount through the reverse
side of the circuit board. Excess lead length may cause
shorting to other conductive parts.
4.
Insert the leads into the holes of the board so that
the replacement component is positioned the same as the
original component. Most components should be firmly
seated against the circuit board.
5.
Touch the soldering iron to the connection and apply
enough solder to make a firm solder joint. Do not move
the component while the solder hardens.
6.
Cut off any excess lead protruding through the cir
cuit board (if not clipped to the correct length in step 3).
7.
Clean the area around the solder connection with an
approved flux-removing solvent. Be careful not to remove
any of the printed information from the circuit board.
REMOVAL AND REPLACEMENT
INSTRUCTIONS
The exploded view drawings in the "Replaceable
Mechanical Parts” list (Section 9) may be helpful during
the removal and reinstallation of individual subassemblies
or components. Circuit board and component locations are
shown in the "Diagrams” section.
Cabinet
w a r n i n g
I
To avoid electric shock, disconnect the instrument
from the ac-power-input source before removing or
replacing any component or assembly.
6 -3 4
Summary of Contents for 2230
Page 12: ...2230 Service X The 2230 Digital Storage Oscilloscope 4998 01 ...
Page 33: ...Operating Information 2230 Service Figure 2 5 Vertical controls and connectors 2 6 ...
Page 48: ...Operating Information 2230 Service Figure 2 11 X Y Plotter interfacing ...
Page 56: ...Theory of Operation 2230 Service 4999 01 3 2 Figure 3 1 Simplified block diagram ...
Page 68: ...Operating Information 2230 Service Figure 2 11 X Y Plotter interfacing ...
Page 76: ...Theory of Operation 2230 Service 4999 01 3 2 Figure 3 1 Simplified block diagram ...
Page 98: ...Theory of Operation 2230 Service 499 9 06 Figure 3 6 Horizontal Amplifier block diagram 3 24 ...
Page 111: ...Theory of Operation 2230 Service 3 37 Figure 3 9 Acquisition Memory timing ...
Page 190: ...Maintenance 2230 Service 999 14 Figure 6 3 Isolated kernel timing 6 9 ...
Page 329: ...PUT Figure 9 2 S em ico n d u cto r lea d co n fig u ratio n s ...
Page 332: ...2230Service CHASSIS MOUNTED PARTS ...
Page 334: ...A14 CH 1 LOGIC BOARD ...
Page 337: ......
Page 344: ...u sr z z o 1 ...
Page 347: ...i n 5 a O Q q o u S a o h UJ s a b c d e f g h j k l m n ...
Page 352: ......
Page 355: ...WAVEFORMS FOR DIAGRAM 5 4999 83 ...
Page 358: ...I W L U O U rc a 4 2 s ...
Page 361: ...WAVEFORMS FOR DIAGRAM 6 S 84 ...
Page 362: ...2230 Service TEST SCOPE TRIGGERED ON U665 PIN 8 FOR WAVEFORMS 31 THROUGH 33 ...
Page 365: ... I I ...
Page 366: ...A 1 6 S W E E P R EFEREN CE BOARD FIG 9 17 2230 Service Figure 9 17 A16 Sweep Reference board ...
Page 369: ... o 0 UJU sa eg aiu c u J in su eg 5 C sis n g e s o N QO ...
Page 371: ...Static Sensitive Devices See Maintenance Section CM I rv CD o 2230 Service ...
Page 378: ......
Page 384: ... I I c o C u o a 5 r O tD v j If 3 IV if I I ci if 5 3 I ...
Page 386: ......
Page 388: ...H K L M N 7 8 8 2 2 3 0 INPUT OUTFUT WIRING INTERCONNECT ...
Page 392: ...W A V E F O R M S F O R D IA G R A M 14 ...
Page 393: ...2230Service 0 0 d s t 4 9 9 9 9 5 ...
Page 394: ...2230 Service TEST SCOPE TRIGGERED ON U911 PIN 21 FOR WAVEFORMS 64 THROUGH 69 4999 92 ...
Page 396: ... ...
Page 397: ...WAVEFORMS FOR DIAGRAM 15 TEST SCOPE TRIGGERED ON U9111 PIN 21 FOR WAVEFORMS 70 THROUGH 77 ...
Page 399: ......
Page 403: ......
Page 404: ......
Page 405: ......
Page 409: ......
Page 415: ...IMF PU TPR A IR TM FQ U I W A V E F O R M SF O RO IA G R A M1 5 W A V E F O R M SF O R i ...
Page 417: ...4999 9S ...
Page 419: ...i s 5 0 C C p F 2 CC p 2 a u 4 I s c c O 2 e e o 5 a o 5 i 2 i f 2 E C 52 ...
Page 423: ...W A V E F O R M SF O RD IA G R A M1 8 O c n ...
Page 424: ...Figure 9 22 A11A1 Input Output board ...
Page 430: ...Figure 9 23 A11A2 Vector Generator board ...
Page 434: ...49 9 9 tOO ...
Page 436: ......
Page 437: ...22 3 0 S ervice W A V E F O R M S F O R D I A G R A M 2 1 m f n h ...
Page 442: ...WAVEFORMS FOR DIAGRAM 22 4999 78 ...
Page 443: ...XY PLOTTER BOARD DIAGRAM 22 See Parts List for serial number ranges ...
Page 447: ...A21 RS 232 OPTION BOARD Flfi A 9 K 01 01 W M ...
Page 450: ......
Page 452: ...COMPONENT NUMBER EXAMPLE ...
Page 459: ...A16 SWEEP REFERENCE ADJUSTMENT LOCATION ...
Page 467: ...2230 Service ...
Page 468: ......
Page 474: ......
Page 475: ...2230 Service ...
Page 476: ...2230 Service ...
Page 477: ... D ...
Page 483: ...2230 Service ...