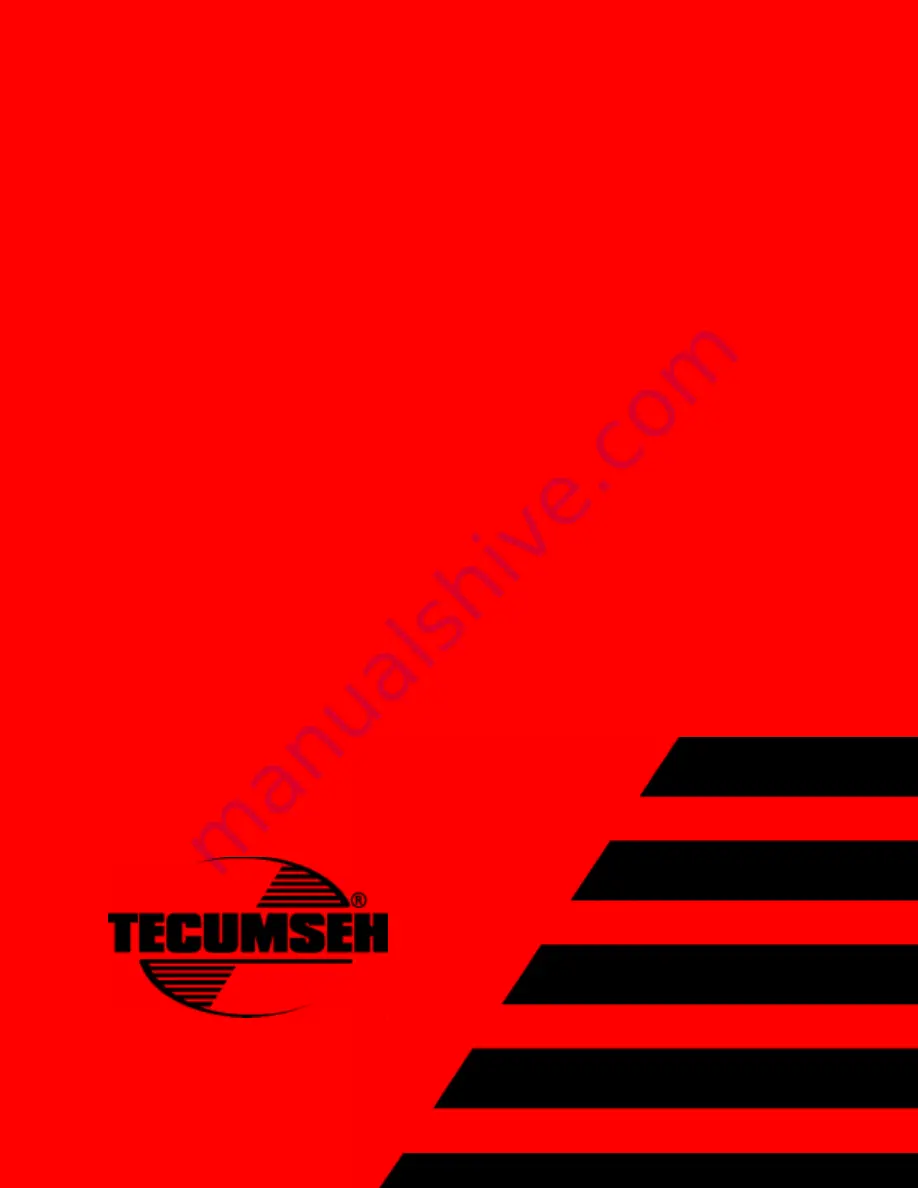
This manual covers engine models:
ECV100 - 120, H22 - 80, HH40 - 70, HHM80, HM70 - 100,
HMSK70 - 110, HMXL70, HS40 - 50, HSK30 - 70, HSSK40 - 50,
HT30 - 35, HXL35, LAV30 - 50, LEV80 - 120, TNT100 - 120,
TVM125 - 220, TVXL170 - 220, TVS75 - 120, TVXL105 - 115,
V40 - 80, VH40 - 70, V60 - 70, VM70 - 100
Model numbers are located on the engine shroud.
3
TO
11
HP
4-CYCLE
L-HEAD
ENGINES
T E C H N I C I A N ' S H A N D B O O K
TECUMSEH