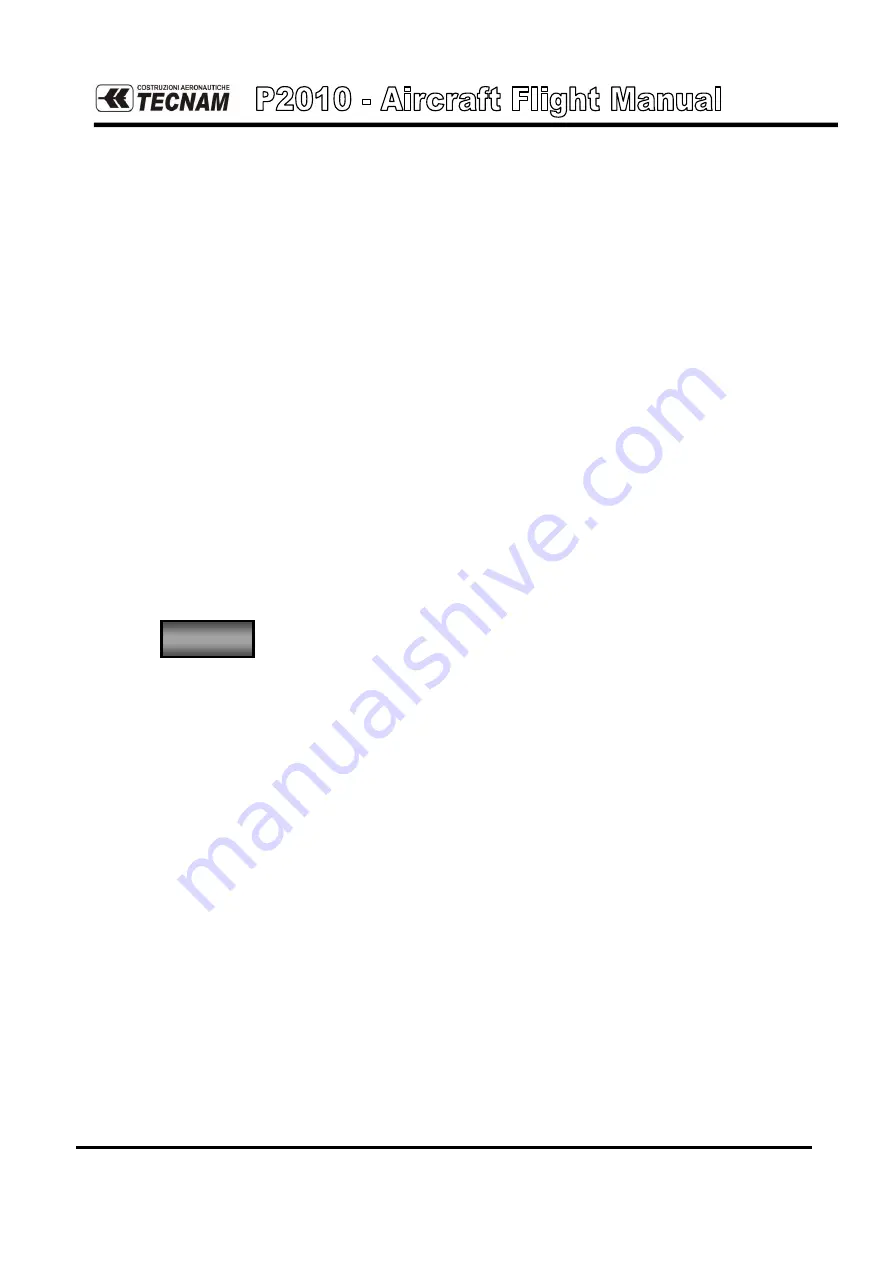
Page 3 - 29
2
nd
Edition, Rev.0
Section 3 – Emergency procedures
LANDING EMERGENCIES
11.
L
ANDING EMERGENCIES
11.1.
F
ORCED LANDING WITHOUT ENGINE POWER
Preparation:
1.
Flaps………………………………….
UP
2.
Best Glide Speed …………………….
85KTS
3.
Radio …………………………………
Transmit MAYDAY giving
location and intentions
4.
Transponder ………………………….
7700
5.
If off airport, ELT ……………………
ON
6.
Find a suitable place to land safely, plan to approach it upwind
7.
Throttle Lever ……………………….
IDLE
8.
Mixture ………………………………
CUTOFF
9.
Fuel Selector ………………………...
OFF
10.
Ignition key ………………………….
OFF
11.
Fuel pump ……………………………
OFF
12.
Seat belts …………………………….
Tightly fastened
When landing is assured
:
13.
Flaps …………………………………
As required
14.
Generator and Master switches ..…….
OFF
Be prepared for aircraft evacuation (Para 4).
11.2.
P
OWER
-
ON FORCED LANDING
1.
Flaps………………………………….
UP
2.
Best Glide Speed …………………….
85KTS
3.
Locate the most suitable terrain for emergency landing, plan to approach upwind
4.
Safety belts……………..………………
Tightly fastened
When landing is assured:
5.
Flaps …………………………………...
As necessary
6.
Fuel selector valve……………………..
OFF
7.
Electric Fuel Pump…………………….
OFF
8.
Ignition Key……………………………
OFF
9.
Generator and Master switches………..
OFF
NOTE
Summary of Contents for P2010
Page 6: ...Page 0 6 2nd Edition Rev 0 Aircraft Flight Manual INTENTIONALLY LEFT BLANK ...
Page 10: ...Page 0 10 2nd Edition Rev 0 Aircraft Flight Manual INTENTIONALLY LEFT BLANK ...
Page 12: ...Page 1 2 Section 1 General 2nd Edition Rev 0 INTENTIONALLY LEFT BLANK ...
Page 23: ...Page 1 13 Section 1 General 2nd Edition Rev 0 INTENTIONALLY LEFT BLANK ...
Page 26: ...Page 1 16 Section 1 General 2nd Edition Rev 0 INTENTIONALLY LEFT BLANK ...
Page 28: ...Page 2 2 Section 2 Limitations 2nd Edition Rev 0 INTENTIONALLY LEFT BLANK ...
Page 30: ...Page 2 4 2nd Edition Rev 0 Section 2 Limitations INTENTIONALLY LEFT BLANK ...
Page 40: ...Page 2 14 Section 2 Limitations 2nd Edition Rev 1 Approved INTENTIONALLY LEFT BLANK ...
Page 46: ...Page 3 4 Section 3 Emergency procedures 2nd Edition Rev 0 INTENTIONALLY LEFT BLANK ...
Page 54: ...Page 3 12 2nd Edition Rev 0 Section 3 Emergency procedures INTENTIONALLY LEFT BLANK ...
Page 62: ...Page 3 20 2nd Edition Rev 0 Section 3 Emergency procedures INTENTIONALLY LEFT BLANK ...
Page 66: ...Page 3 24 2nd Edition Rev 0 Section 3 Emergency procedures INTENTIONALLY LEFT BLANK ...
Page 74: ...Section 4 Normal procedures 2nd Edition Rev 0 Page 4 2 INTENTIONALLY LEFT BLANK ...
Page 78: ...Page 4 6 Section 4 Normal procedures 2nd Edition Rev 0 INTENTIONALLY LEFT BLANK ...
Page 80: ...Page 4 8 Section 4 Normal procedures 2nd Edition Rev 0 INTENTIONALLY LEFT BLANK ...
Page 86: ...Page 4 14 Section 4 Normal procedures 2nd Edition Rev 0 0 INTENTIONALLY LEFT BLANK ...
Page 116: ...Page 5 18 Section 5 Performances 2nd Edition Rev 0 INTENTIONALLY LEFT BLANK ...
Page 118: ...Page 6 2 Section 6 Weight and Balance 2nd Edition Rev 0 INTENTIONALLY LEFT BLANK ...
Page 126: ...Page 6 10 Section 6 Weight and Balance 2nd Edition Rev 0 INTENTIONALLY LEFT BLANK ...
Page 130: ...Page 6 14 Section 6 Weight and Balance 2nd Edition Rev 0 INTENTIONALLY LEFT BLANK ...
Page 170: ...Page 8 2 Section 8 Aircraft Care and Maintenance 2nd Edition Rev 0 INTENTIONALLY LEFT BLANK ...
Page 172: ...Page 8 4 Section 8 GROUND HANDLING SERVICE 2nd Edition Rev 0 INTENTIONALLY LEFT BLANK ...
Page 180: ...Page 8 12 Section 8 GROUND HANDLING SERVICE 2nd Edition Rev 0 INTENTIONALLY LEFT BLANK ...
Page 188: ...Page 9 4 Section 9 AFM Supplements 2nd Edition Rev 0 INTENTIONALLY LEFT BLANK ...