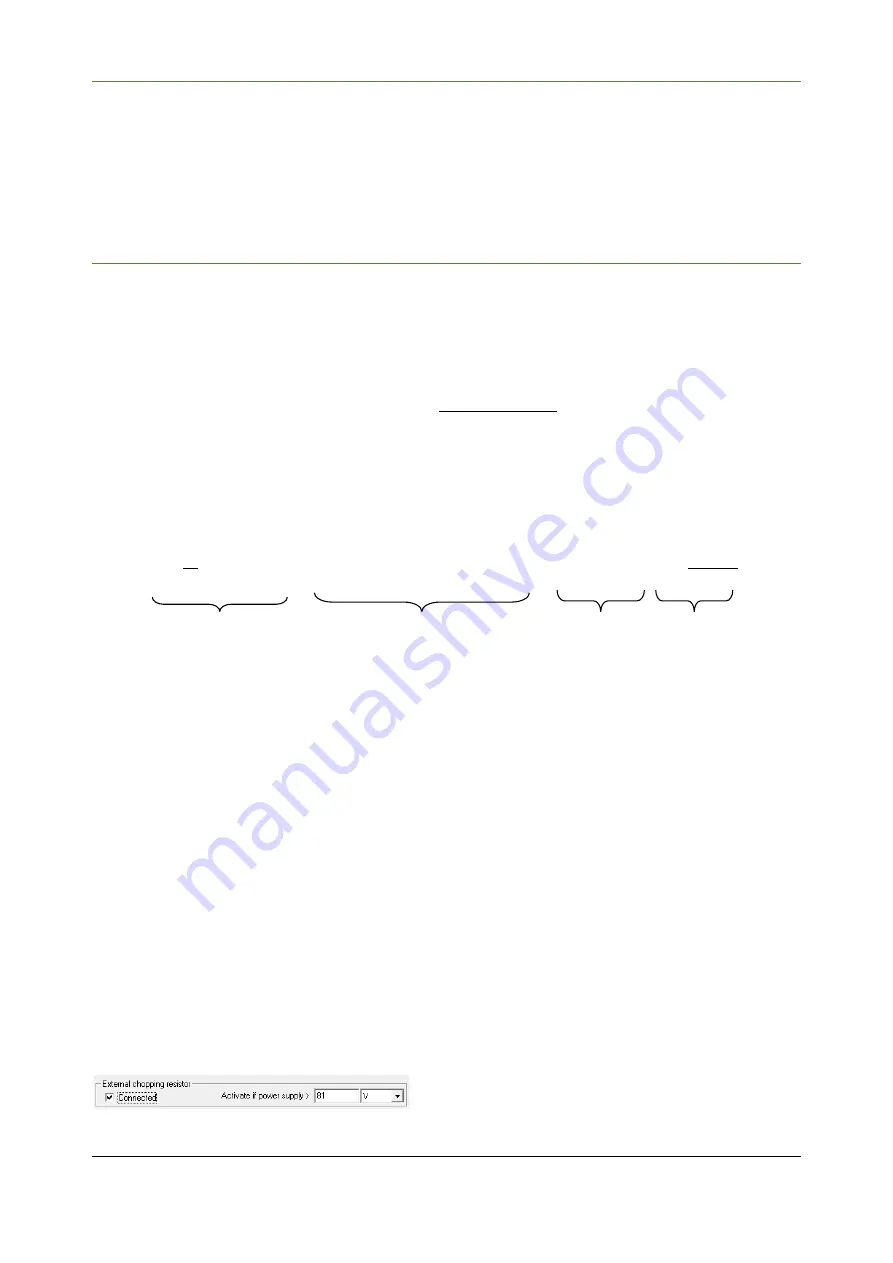
Technosoft 2019
34
iMOTIONCUBE Technical Reference
3.5.9.3
Recommendations for Supply Wiring
The iMOTIONCUBE always requires two supply voltages: V
log
and V
mot
.
Use short, thick wires between the iMOTIONCUBE and the motor power supply. Connect power supply
wires to all the indicated pins. If the wires are longer than 2 meters, use twisted wires for the supply and
ground return. For wires longer than 20 meters, add a capacitor of at least 4,700μF (rated at an appropriate
voltage) right on the terminals of the iMOTIONCUBE.
It is recommended to connect the negative motor supply return (GND) to the Earth protection near the power
supply terminals.
3.5.9.4
Recommendations to limit over-voltage during energy regeneration
During abrupt motion decelerations or reversals the regenerative energy is injected into the motor power supply. This
may cause an increase of the motor supply voltage (depending on the power supply characteristics). If the voltage
bypasses 81V, the drive over-voltage protection is triggered and the drive power stage is disabled. In order to avoid this
situation you have 2 options:
Option 1. Add a capacitor on the motor supply
big enough to absorb the overall energy flowing back to the supply.
The capacitor must be rated to a voltage equal or bigger than the maximum expected over-voltage and can be sized
with the formula:
2
2
2
NOM
MAX
M
U
U
E
C
−
×
≥
where:
U
MAX
= 28V is the over-voltage protection limit
U
NOM
is the nominal motor supply voltage
E
M
= the overall energy flowing back to the supply in Joules. In case of a rotary motor and load, E
M
can be
computed with the formula:
F
M
d
d
Ph
2
M
final
initial
L
M
2
M
L
M
M
T
2
t
t
R
3I
)
h
-
)g(h
m
(m
)
J
(J
2
1
E
ϖ
ϖ
−
−
+
+
+
=
where:
J
M
– total rotor inertia [kgm
2
]
J
L
– total load inertia as seen at motor shaft after transmission [kgm
2
]
ϖ
M
– motor angular speed before deceleration [rad/s]
m
M
– motor mass [kg] – when motor is moving in a non-horizontal plane
m
L
– load mass [kg] – when load is moving in a non-horizontal plane
g
– gravitational acceleration i.e. 9.8 [m/s
2
]
h
initial
– initial system altitude [m]
h
final
– final system altitude [m]
I
M
– motor current during deceleration [A
RMS
/phase]
R
Ph
– motor phase resistance [
Ω
]
t
d
– time to decelerate [s]
T
F
– total friction torque as seen at motor shaft [Nm] – includes load and transmission
In case of a linear motor and load, the motor inertia J
M
and the load inertia J
L
will be replaced by the motor mass and
the load mass measured in [kg], the angular speed
ϖ
M
will become linear speed measured in [m/s] and the friction
torque T
F
will become friction force measured in [N].
Option 2. Connect a chopping resistor R
CR
between phase CR/B- and ground, and activate the software option of
dynamic braking (see below).
This option is not available when the drive is used with a step motor.
The chopping resistor option can be found in the Drive Setup dialogue within EasyMotion / EasySetup :
The chopping will occur when DC bus voltage increases over U
CHOP
. This parameter (U
CHOP
) should be adjusted
depending on the nominal motor supply. Optimally (from a braking point of view), U
CHOP
should be a few volts above
Kinetic energy
Copper losses Friction losses
Potential energy