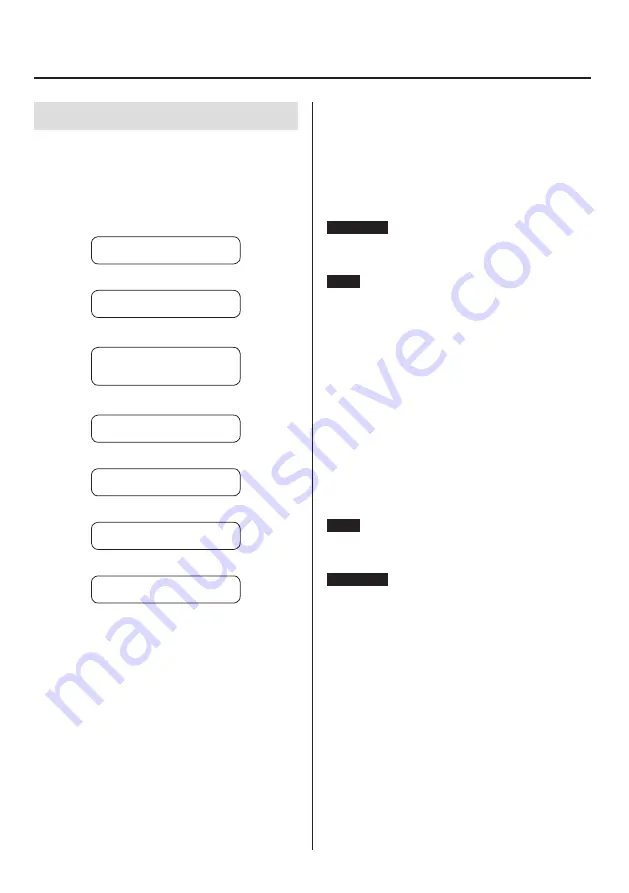
37
8-2. Equivalent input calibration
This method determines the calibration value by recording
rated output and rated capacity values from a test report.
Use this to calibrate easily when an actual load cannot be
applied.
An overview of the equivalent input calibration procedures is
shown below.
Bridge Voltage
c
Decimal Point Position
c
Rated Output Value/
Rated Capacity Value
c
Zero Balancing
c
D/A Output Mode*
c
D/A Maximum Voltage*
c
Calibration Value Lock
o
See “7. D/A converter” on page 33 for information about
D/A settings.
*TD-SC1 (D/A) only
8-2-1. Bridge Voltage
Options: 5 V, 10 V
Set the bridge voltage to supply to the strain gauge transducer.
o
As a reference for setting the bridge voltage, consider that
the output from the sensor should be increased, and set
the maximum voltage in a range that does not exceed the
maximum safe excitation voltage on the sensor test report.
ATTENTION
A sensor could be damaged if this is set to a value that exceeds
its maximum safe excitation voltage.
NOTE
The default value is 5 V.
8-2-2. Decimal Point Position
Set the decimal point position for the rated capacity value.
8-2-3. Rated Output Value
Input range: 0.050 to 5.000 mV/V
Set the rated output of the strain gauge transducer being
used.
8-2-4. Rated Capacity Value
Set the rated capacity of the strain gauge transducer being
used.
NOTE
The decimal point position set here will be used as the indica-
tor value decimal point position.
ATTENTION
When using a D/A option, the rated capacity is set as the D/A
full scale value.
8-2-5. Zero Balancing
With no load on the sensor, send a Zero Balancing command.
During zero balancing, ST1 will be “Executing”.
o
If ST1 becomes “Error occurred”, conduct countermeasures
and redo calibration.
8. Calibration