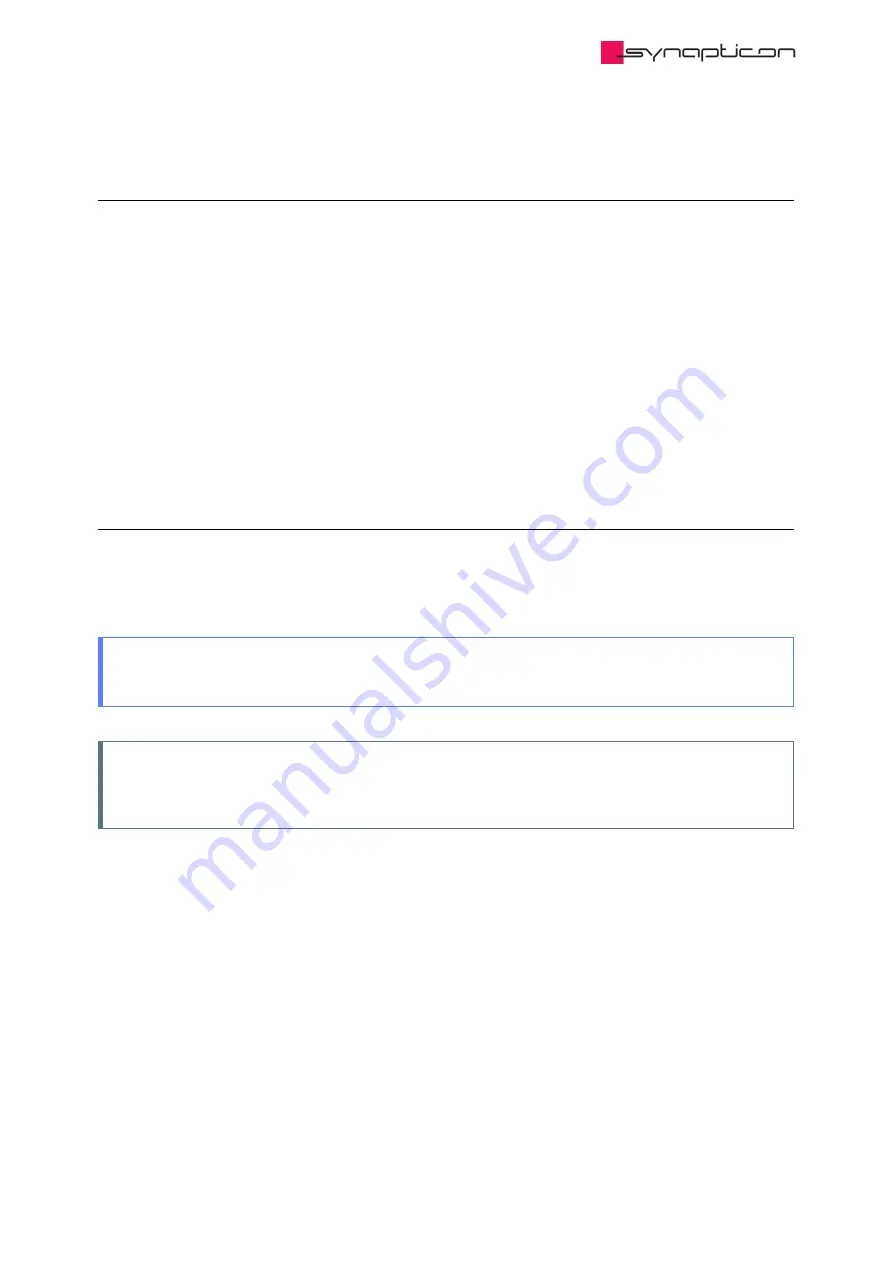
3.1.8.3.11.2 Following error
The easiest way to measure the performance of a control loop is to calculate a following error:
Following error = Target value - Actual value
If the master-generated value is used as a target value, it is not synchronized with the actual measured value.
The typical delay can be up to 3 communication cycles. Thus, the computed error will contain an extra error
due to communication delay.
To circumvent this issue, ‘Demanded value’ objects should be used. These values a sampled synchronously
with the actual measured value and should be used to correctly compute the following error.
Example: Velocity following error = Velocity demanded value - Velocity actual value
Alternatively, the object Following error actual value (0x60F4) can be used to monitor the position control
loop.This object is also used for the Following Error Window feature.
3.1.8.3.11.3 Following error window
If the actual value is outside of the configured window for a configured period of time, the user is informed
that the following error is bigger than the configured value.
This information is reflected by bit 10 of the statusword.
Use case: Predictive maintenancing (monitor system wear)
In case the following error grows bigger in time, check if mechanical wear is the reason.
Note
The Following error window feature can only be used in a position control mode (operational modes
CSP and PP)
Synapticon Documentation
© 2021 Synapticon GmbH | Daimlerstraße 26 | D-71101 Schönaich Documentation v 4.19.0 | Built 2022-02-01
703/1031