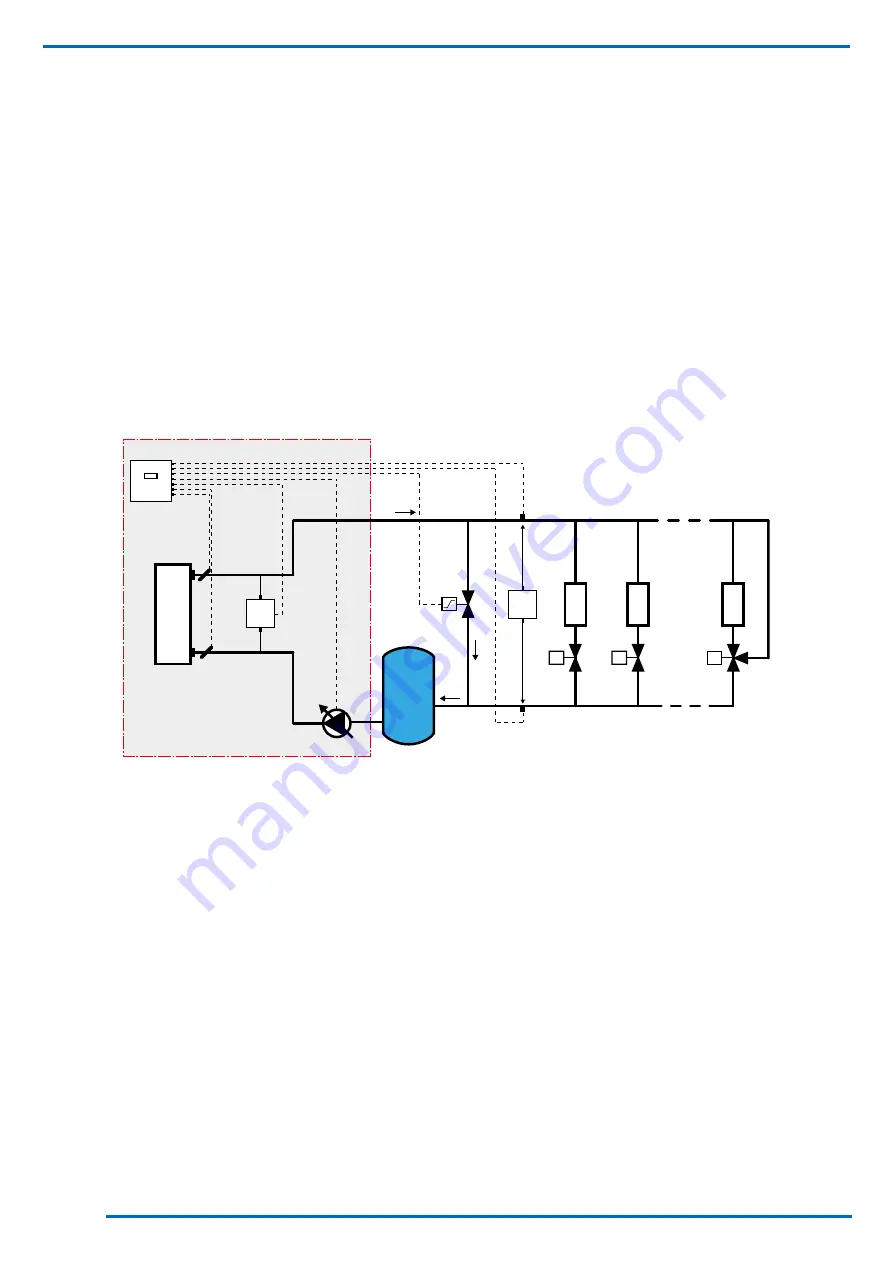
52
We reserve the right to make changes without any prior notice.
Translation from original instructions
7.3.5 Flowzer VFPP
The “VFPP” function is designed to control variable flow systems to the primary circuit.
The system keeps stable the difference in the water pressure and temperature in the system delivery line as the demand
changes.
The water flow rate and temperature are independent variables and not directly connected.
Control of the “single pump in the system” provides for the necessary flow rate/head, while control of the cooling capacity
provides for the correct temperature.
If the demand from the system is reduced, the pressure difference increases and the controller offsets it by reducing the
pump speed, which results in energy consumption saving.
The water flow rate in the primary circuit is always set within the limits required for correct operation of the cooling unit.
The controller in units featuring a heat pump offers the possibility to set a pressure difference for operation in cooling mode
and a pressure difference for operation in heating mode, which helps the unit adapt to seasonal requirements.
This function requires the installation of pressure probes on the system delivery and return lines in addition to a bypass
valve.
The bypass valve and the probes are supplied in a kit. They must be connected as shown in the wiring diagram.
For this function to be applied correctly, the hydraulic circuit must be made as shown in the diagram below.
A040
Y2V
Vmin.
U2
U1
Un
Y2V
Y2V
Y3V
VP
A2
UL
ΔPp
BPWO
BPWI
UE
BT2
BT1
ΔPex
BP41
The abbreviations present in the diagram indicate:
- A2 = cooling unit controller
- BT1 = unit input temperature sensor
- BT2 = unit output temperature sensor
- EU = heat exchanger in cooling unit
-
BP41= differential pressure sensor;
-
ΔPex = pressure difference at the ends of the unit;
-
VP = variable flow pump
- A040 = 2-way bypass valve servo control
-
BPWO = system/plant delivery pressure sensor
-
BPWI = system/plant return pressure sensor
-
ΔPp = pressure difference at the ends of the system
-
U1, U2 .. Un = points of use present in the system/plant
- Y2V = 2-way valve servo controls
- Y3V = 3-way valve servo controls