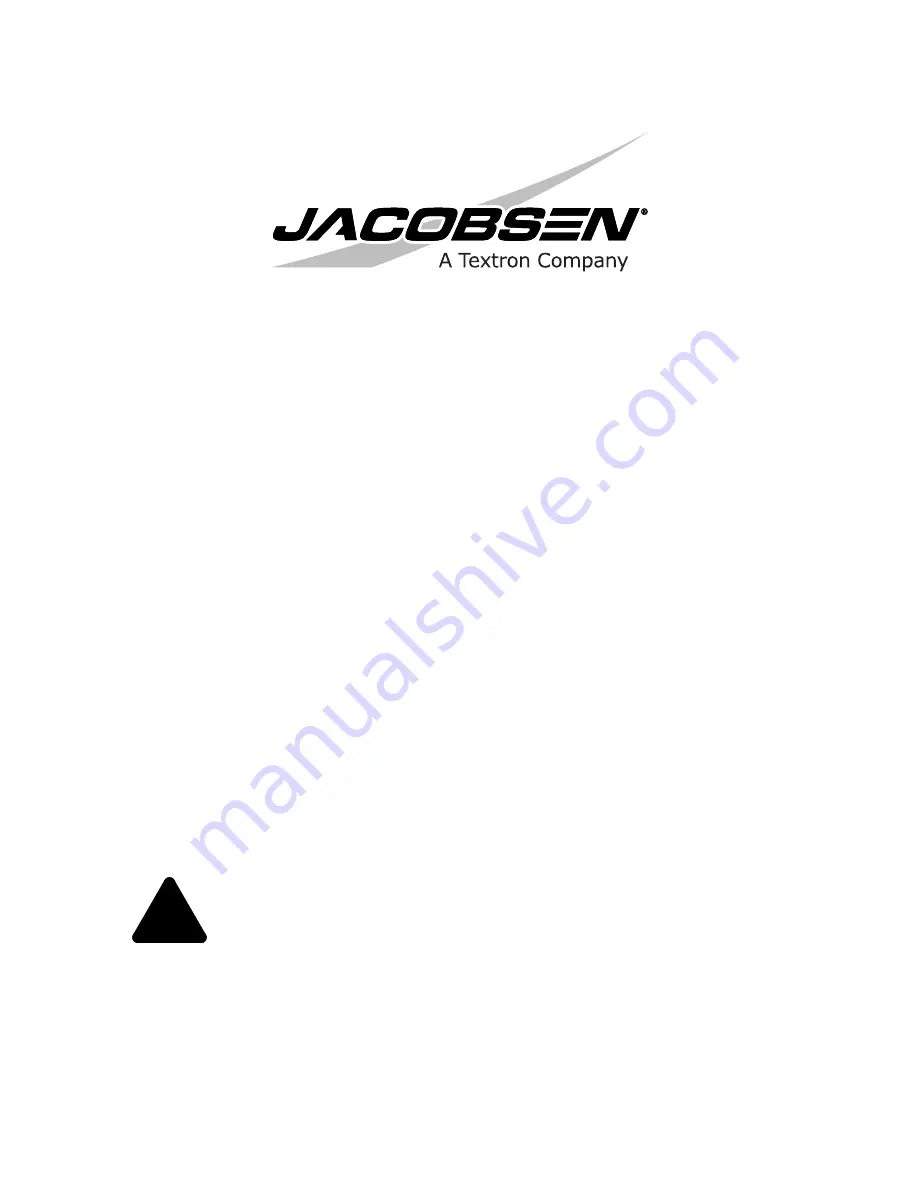
Suzuki K6A-YH6 Engine
Technical/Repair Manual
WARNING: If incorrectly used this machine can cause severe injury. Those
who use and maintain this machine should be trained in its proper use,
warned of its dangers and should read the entire manual before attempting to
set up, operate, adjust or service the machine.
!
©2007 Jacobsen, A Textron Company. All rights reserved.
When Performance Matters.
™
Summary of Contents for K6A-YH6
Page 6: ...1 2 SAFETY 1 Page Intentionally Blank...
Page 22: ...2 12 SPECIFICATIONS AND GENERAL INFORMATION 2...
Page 26: ...3 4 MAINTENANCE 3...
Page 54: ...6 6 DIAGNOSTIC TROUBLESHOOTING 6...
Page 102: ...7 48 REPAIR 7...
Page 103: ...8 8 1 Chapter 8 Tools and Materials Special Tools 8 1 Required Materials 8 2...
Page 106: ...8 4 TOOLS AND MATERIALS 8...
Page 112: ...IX 6 INDEX IX...