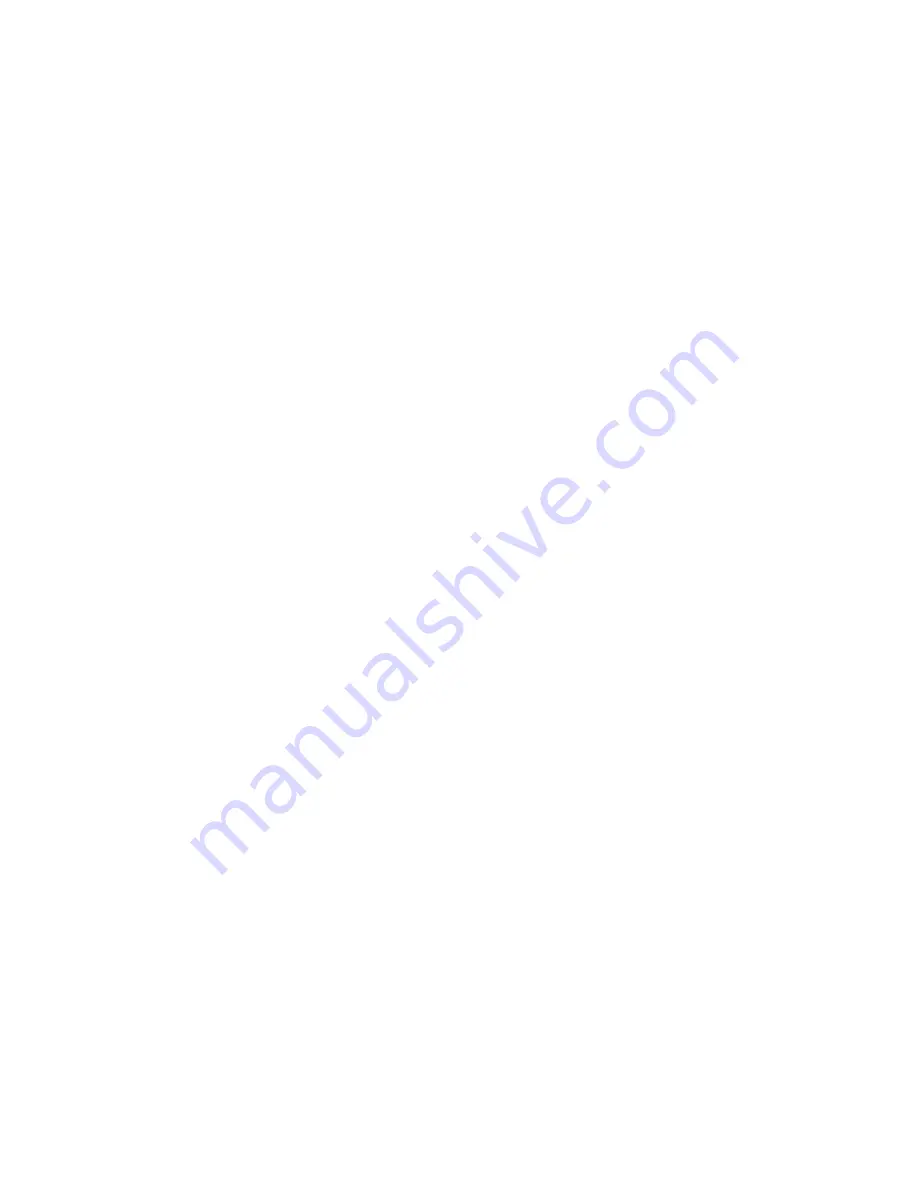
40
can be most effectively decreased in the P-97 by decreasing air pressure, however a
decreasing TIME may also be useful.
5.1.4
Problem: How can the size of a patch-pipette be increased?
1.
The first thing to try is to reduce the HEAT on the last line of the program. Try dropping
the HEAT 5 units at a time to see if this will increase the size of the tips.
2.
If this does not work, increase the pressure in units of 50. The PULL should generally be
set to 0 when pulling large tipped (1-10 mm) pipettes.
3.
See also the Step 10 under “Step-by-step patch programming” in the PARAMETER
ADJUSTMENT chapter and Chapter 1 in the Pipette Cookbook.
5.1.5
Problem: Patch-pipette tips vary in size from pull to pull.
This can happen when a pipette is formed in two or more loops. If the pipette is formed in
three loops in one case and then on the next pull it forms in four loops the tips will not be the
same. Adding one unit in the VELOCITY value will in most cases cause the pipette to be
formed in three loops or subtracting one unit should cause the pipette to form in four loops.
It is always good technique when a program is developed that produces a desired pipette, to
try increasing and decreasing the VELOCITY value to be sure that you are in a stable region.
The best procedure in developing a very reliable pipette program is to change the VELOCITY
value both up and down until the number of cycles to pull the pipette changes. Then pick a
value halfway between for the final VELOCITY value.
5.1.6
Problem: Difficulty making an injection pipette with a 0.5 – 1 mm tip that also has a
very short final taper and tip (20 to 50 mm long). How can this be done?
(See “Bee Stinger” pipettes in Chapter 3 of the Pipette Cookbook.)
Try a program in which the first two lines of the program have a PULL value of 0, a
VELOCITY value of 10 to 30, a TIME setting of 200 and use the ramp value for the HEAT
(box filament). The third line should have the same HEAT value, a PULL value of 150, a
VELOCITY of 30 and the TIME should be between 0 to 50 depending on the tip needed
(values may vary depending on glass characteristics).
The idea behind this program is to reduce the size of the glass on the first two cycles and
then on the third cycle we give a hard pull with the air turned off. Normally if the air is
turned off a long wisp will result, but since we have greatly reduced the size of the glass and
with a very hard pull the glass will tend to separate when it is about 1mm in diameter.
5.1.7
Problem: The electrodes are bent. How can they be made to pull straight?
This problem occurs most often when using the trough filament. Going to a box type of
filament will produce straighter pipettes. The bend in the pipette has no effect on the
pipette’s tip and should cause no problems unless you are penetrating quite deep in the
tissue and you are aiming at a certain site. Then the bend may lead the pipette to the wrong
area. The box filament is not a complete improvement on the trough filament as the airflow
is much less effective with the box filament, and you give up much of the length control that
the cooling air gives with the trough filament.
5.1.8
Problem: One electrode is much longer than the other electrode.
This is caused by one of two things.
P-97 FLAMING/BROWN MICROPIPETTE PULLER OPERATION MANUAL – REV. 2.43 - DOM (20161118)
Summary of Contents for P-97
Page 3: ......
Page 4: ......
Page 66: ...56 NOTES P 97 FLAMING BROWN MICROPIPETTE PULLER OPERATION MANUAL REV 2 43 DOM 20161118...