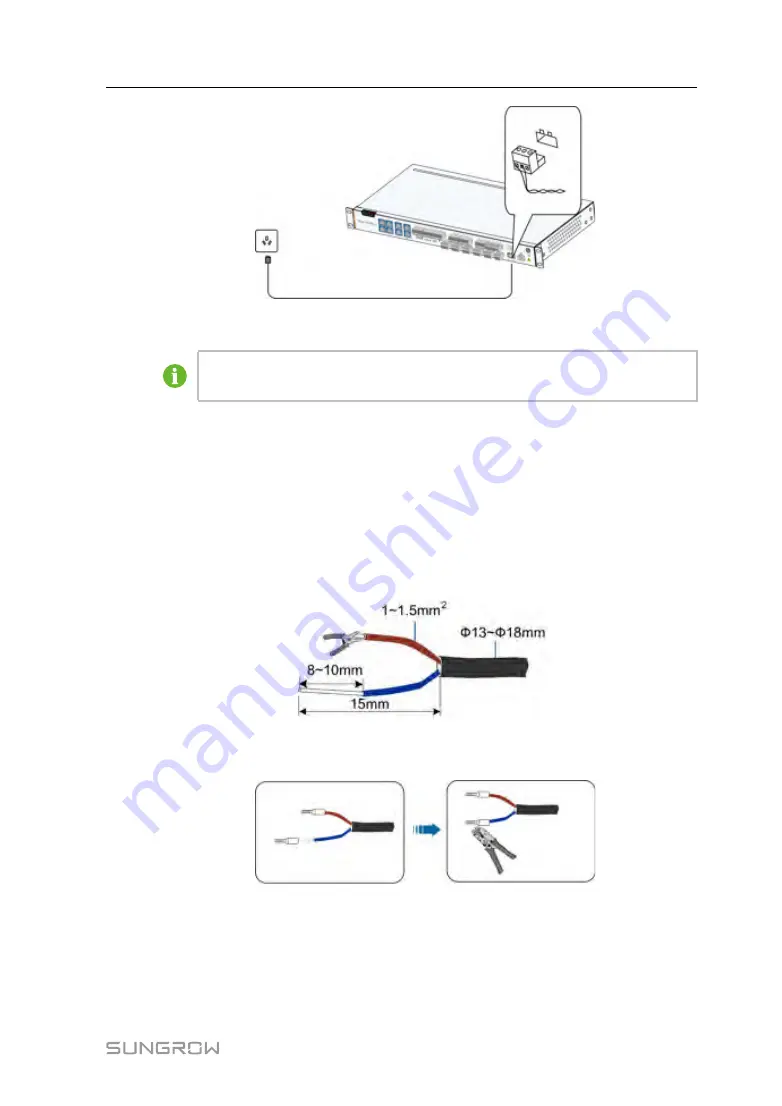
39
-- -- E
En
nd
d
The Logger4000 can be connected to both AC power supply and DC power
supply. UPS can be used as a DC backup power source.
7.13 Connecting to the DC Power Supply
The Logger4000 can be connected to 24Vdc external power supply. UPS can be used
as a power source.
step 1
Lead the external power supply cable to the wiring area of the Logger4000.
step 2
Strip off the protective layer and insulation layer of the power cable with wire strippers,
as shown below.
step 3
Assemble proper cord end terminals to power cable whose protective layer and
insulation layer are stripped off and crimp them with a crimping tool.
step 4
Connect the cord end terminals to the plug "DC IN 24V,1.25A" outside Logger4000.
User Manual