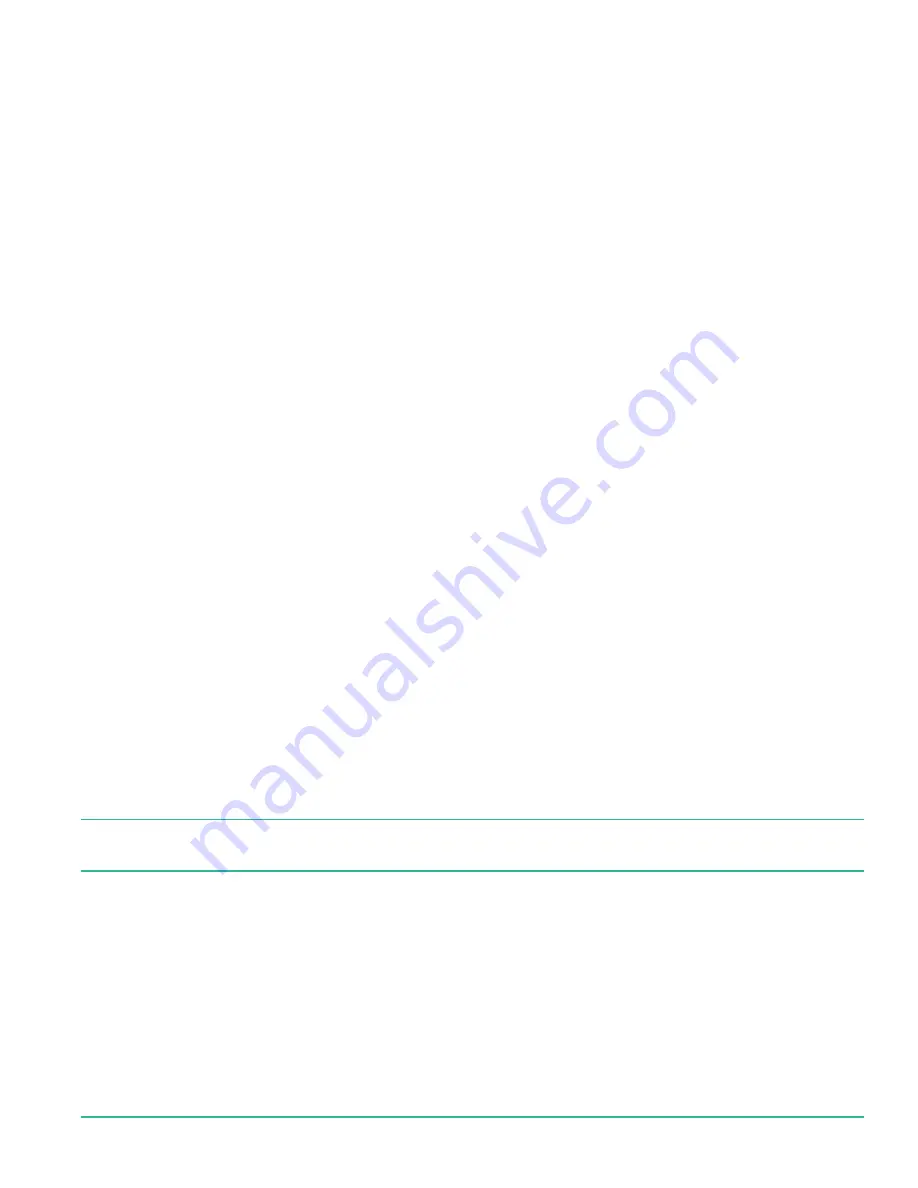
29
COMPONENT DESCRIPTION
3.4.2 PRESSURE RELIEF VALVE
The pressure relief valve will open to relieve excess pressure in the sump tank if the pressure exceeds the set
point. The valve will automatically reset to its reset pressure point after the excess pressure is relieved. The
pressure relief valve is ASME compliant and rated at 200 psig to match the rating of the tank. It is located on
the upper side (wet side) of the sump tank.
3.4.3 ANTI-START PRESSURE (ASP) SWITCH
This switch is supplied to stop the system from starting up when running in reverse rotation. This built-in
feature helps to protect the compressor unit from being run in reverse rotation for an extended period of
time. The switch body is located in the electrical enclosure and is tubed into the unit inlet.
3.4.4 COMPRESSOR DISCHARGE TEMPERATURE (CDT) SWITCH
This switch is supplied to shut the compressor down in the presence of high unit discharge temperature. The
switch is non-adjustable and preset at 240°F (116°C). It is located in the compressor unit discharge outlet
port.
3.4.5 HIGH AIR TEMPERATURE (HAT) SWITCH (OPTIONAL)
This switch is supplied to shut down the compressor in the presence of high sump tank outlet temperature.
The switch is non-adjustable and preset at 220°F (104°C). The switch body is located on the back bottom
port of the minimum pressure valve.
3.5
AIR/OIL DISCHARGE SYSTEM
After compression, the high pressure air and oil mixture travels to the sump tank where the air and oil is
separated by change of direction and reduction in velocity. The oil is stored in the bottom portion (sump) of
the tank until it is recirculated through the system.
The remaining oil in the air is reduced by the air/oil separator in the top portion of the sump tank. Oil
removed by the separator collects the bottom pan of the element and is returned to the low pressure side
of the compressor unit by the scavenger line. After passing through the air/oil separator, the compressed air
then continues through to the minimum pressure valve.
Initially, the pressure is held by the MPV (minimum pressure valve) until the set point of the valve is reached.
Once the minimum pressure is met, the minimum pressure valve will allow air to pass through to the
aftercooler to reduce the temperature of the air from a nominal 180°F to 100°F (82°C to 38°C). This change
in temperature condenses the water so that it can be removed by a water separator equipped with an
electric drain valve. After leaving the water separator, the compressed air can then begin building pressure in
the air system for use.
3.5.1 SUMP TANK (RECEIVER)
The sump tank (also referred to as a receiver, reservoir or separator tank) collects and holds oil to be
circulated through the compressor cooling system. Air and oil discharged from the compressor unit are
separated in the sump tank by change of direction and reduction in velocity. The sump tank is an ASME
pressure vessel rated for 200 psig maximum operating pressure.
3.5.2 AIR/OIL SEPARATOR
The air/oil separator (also referred to as a separator element) separates the majority of the remaining oil in
the air before the air passes through the minimum pressure valve to the aftercooler. The air/oil separator is
located in the upper part of the sump tank under the lid.
WARNING!
DO NOT REMOVE STAPLES! The air/oil separator is supplied with staples in the gaskets to ground the
separator to the sump tank in order to prevent flash fires created by build-up of static electricity.
3.5.3 MINIMUM PRESSURE VALVE
The minimum pressure valve maintains the minimum pressure in the sump tank necessary to circulate
oil throughout the compressor and also prevents reverse airflow into the compressor upon unloading or
shutdown. At start-up, the valve remains closed and no output air is supplied until the minimum pressure is
reached. Once the minimum pressure is reached, the valve will open and allow air to enter the system for use.
At shutdown or unloading, a built-in check valve closes to prevent reverse airflow. The minimum pressure
valve is located on top of the sump tank lid.
Summary of Contents for 15D
Page 6: ...vi About This Manual ...
Page 12: ...4 Introduction ...
Page 20: ...12 Specifications 2 2 DIMENSIONS OPEN BASE MOUNT AIR COOLED Figure 2 1 GA 15 40D AC BM OPEN ...
Page 30: ...22 Specifications 2 12 PIPING AND INSTRUMENTATION AIR COOLED Figure 2 11 GA P I S R02 ...
Page 34: ...26 Specifications ...
Page 66: ...58 Troubleshooting ...
Page 112: ...NOTES ...
Page 113: ...NOTES ...