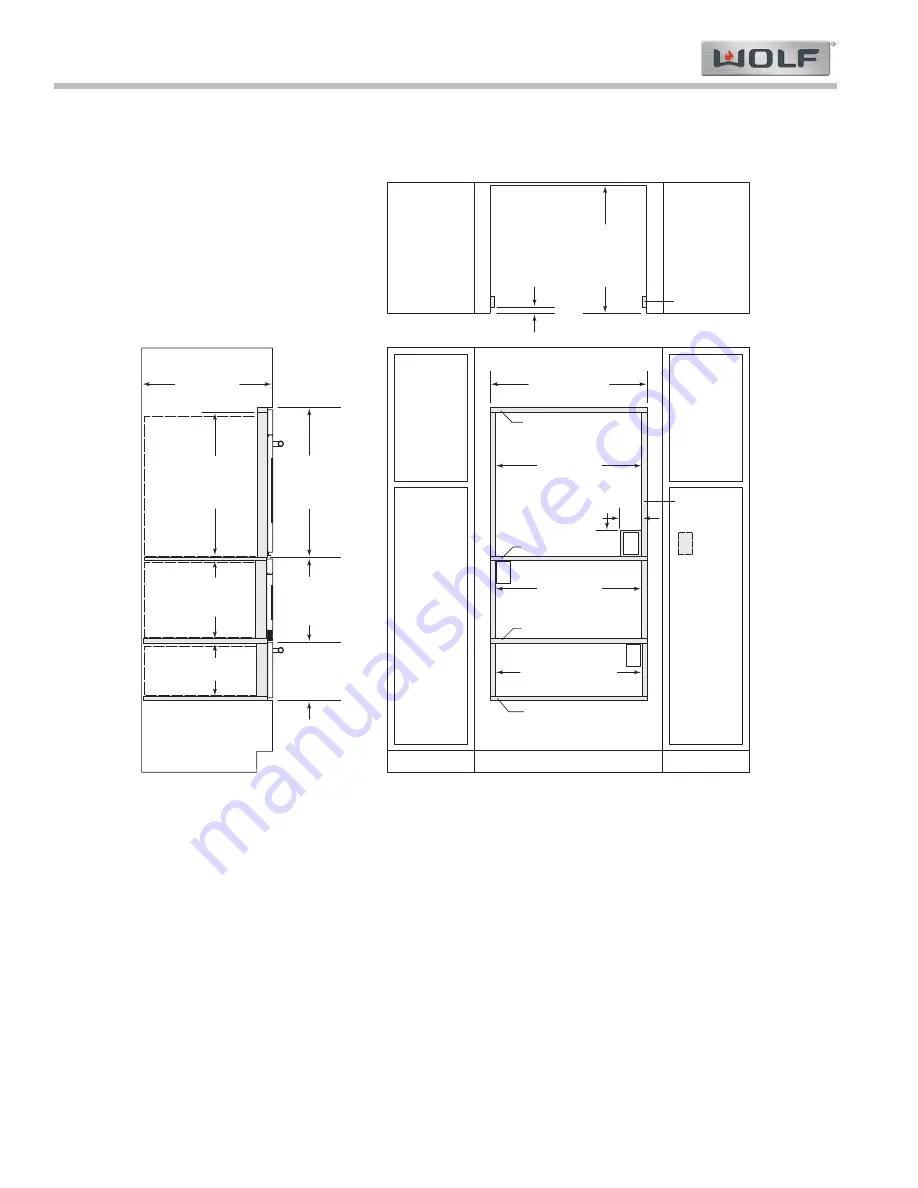
Page 12
Warming Drawer WWD30-2
Installation Information
2-8
#814750 - Revision A - January, 2011
Flush Inset Tower Installation
27
3
/
16
"
(691)
OPENING
HEIGHT
28
1
/
8
"
(714) min
FLUSH INSET
HEIGHT
28
1
/
2
"
(724)
E SERIES OVEN
OPENING WIDTH
25"
(635) min
CABINET DEPTH
30
3
/
8
"
(772) min
FLUSH INSET WIDTH
28
1
/
2
"
(724)
DRAWER MICROWAVE
OPENING WIDTH
E
7
/
8
"
(22) TOP CLEAT
9
/
16
"
(14)
PLATFORM*
5
/
8
"
(16) PLATFORM
SIDE CLEATS
24
3
/
4
"
(629) min
FLUSH
INSET
DEPTH
1
1
/
4
"
(32)
FOR MICROWAVE
1"
(25) FOR OVEN
AND WARMING
DRAWER
*
Platform mus t s upport 250 lbs
(113 kg.
NO T E : Location of electrical s upply within oven opening may require additional cabinet depth. Das hed line repres ents profile of unit.
FRONT VIEW
SIDE VIEW
TOP VIEW
14
3
/
4
"
(375)
OPENING
HEIGHT
15
3
/
8
"
(391)
FLUSH INSET
HEIGHT
1"
(25)
SIDE CLEATS
10
5
/
8
"
(270)
FLUSH INSET
HEIGHT
9
1
/
8
"
(232)
OPENING HEIGHT
E
1"
(25) PLATFORM
28
5
/
8
"
(727)
WARMING DRAWER
OPENING WIDTH
E
E
5"
(127)
4"
(102)
INS TAL L ATION WITH DR AW E R MIC R OWAVE AND E S E R IE S OVE N