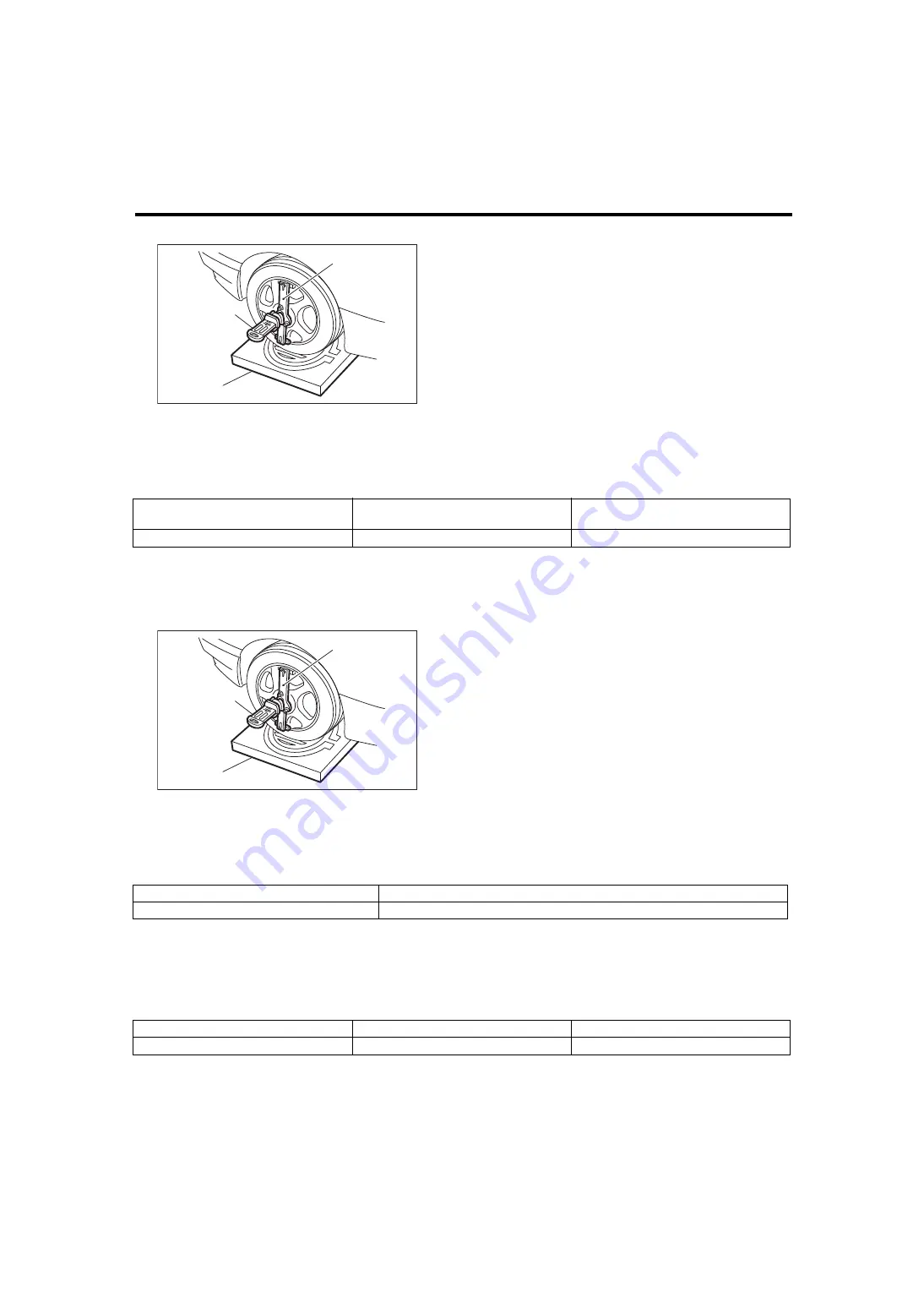
FS-9
Wheel Alignment
FRONT SUSPENSION
2) Set the adapter into the center of wheel, and then set the wheel alignment gauge.
3) Measure the camber angle in accordance with the operation manual for wheel alignment gauge.
3. CASTER
1) Place the front wheel on the turning radius gauge. Make sure the ground contact surfaces of the front and
rear wheels are at the same height.
2) Set the adapter into the center of wheel, and then set the wheel alignment gauge.
3) Measure the caster angle in accordance with the operation manual for wheel alignment gauge.
4. STEERING ANGLE
1) Place the vehicle on turning radius gauge.
2) While depressing the brake pedal, turn the steering wheel fully to the left and right.
3) With the steering wheel held at each fully turned position, measure both the inner and outer wheel steering
angles.
FS-00213
(1)
(2)
(3)
(1) Alignment gauge
(2) Turning radius gauge
(3) Adapter
Tire size
Front camber (difference between RH
and LH 45
or less)
Rear camber (difference between RH and
LH 45
or less)
265/35R19
–1°05
0°30
–1°50
0°45
FS-00213
(1)
(2)
(3)
(1) Alignment gauge
(2) Turning radius gauge
(3) Adapter
Tire size
Caster
265/35R19
6°38
Tire size
Inner wheel
Outer wheel
265/35R19
32.0°
1.5°
28.6°
1.5°
Summary of Contents for S209 2019
Page 2: ......
Page 3: ...FOREWORD FW Page 1 Foreword 2...
Page 5: ...SPECIFICATIONS SPC Page 1 S209 2...
Page 8: ...SPC 4 S209 SPECIFICATIONS...
Page 9: ...IDENTIFICATION ID Page 1 Identification 2...
Page 12: ...ID 4 Identification IDENTIFICATION...
Page 13: ...RECOMMENDED MATERIALS RM Page 1 Recommended Materials 2...
Page 15: ...PRE DELIVERY INSPECTION PI Page 1 Pre delivery Inspection 2...
Page 18: ...PI 4 Pre delivery Inspection PRE DELIVERY INSPECTION...
Page 19: ...PERIODIC MAINTENANCE SERVICES PM Page 1 Schedule 2 2 Air Cleaner Element 5...
Page 24: ...PM 6 Air Cleaner Element PERIODIC MAINTENANCE SERVICES...
Page 26: ......
Page 27: ...FUEL INJECTION FUEL SYSTEMS FU Page 1 General Description 2...
Page 58: ...IN 28 Intercooler Water Spray Hose INTAKE INDUCTION AA 14017 AA 14018 AA 14019...
Page 69: ...MECHANICAL ME Page 1 General Description 2 2 Cylinder Head 3...
Page 73: ...LUBRICATION LU Page 1 General Description 2...
Page 76: ......
Page 77: ...CONTROL SYSTEMS CS Page 1 General Description 2 2 MT Gear Shift Lever 4...
Page 90: ...CS 14 MT Gear Shift Lever CONTROL SYSTEMS...
Page 91: ...CLUTCH SYSTEM CL Page 1 General Description 2...
Page 94: ......
Page 97: ...FS 3 General Description FRONT SUSPENSION Individual toe angles...
Page 112: ...FS 18 Front Crossmember Support Plate FRONT SUSPENSION 5 Lower the vehicle...
Page 156: ...RS 28 Rear Flexible Draw Stiffener REAR SUSPENSION...
Page 157: ...WHEEL AND TIRE SYSTEM WT Page 1 General Description 2 2 Tire Repair Kit 3...
Page 161: ...BRAKE BR Page 1 General Description 2 2 Front Brake Pad 6 3 Rear Brake Pad 9...
Page 170: ...BR 10 Rear Brake Pad BRAKE...
Page 184: ......
Page 185: ...INSTRUMENTATION DRIVER INFO IDI Page 1 General Description 2...
Page 188: ...IDI 4 General Description INSTRUMENTATION DRIVER INFO...
Page 264: ...EI 76 Trunk Room Trim EXTERIOR INTERIOR TRIM...
Page 265: ...EXTERIOR BODY PANELS EB Page 1 Front Fender 2...
Page 270: ......
Page 280: ...WI 10 Rear Wiring Harness and Trunk Lid Cord WIRING SYSTEM...
Page 282: ......
Page 283: ......
Page 284: ......
Page 285: ......
Page 286: ......
Page 287: ......
Page 288: ......
Page 289: ...0 50mm 50mm...
Page 290: ...0 50mm 50mm...
Page 291: ......
Page 292: ......
Page 293: ......
Page 294: ......
Page 295: ......
Page 296: ......
Page 297: ......