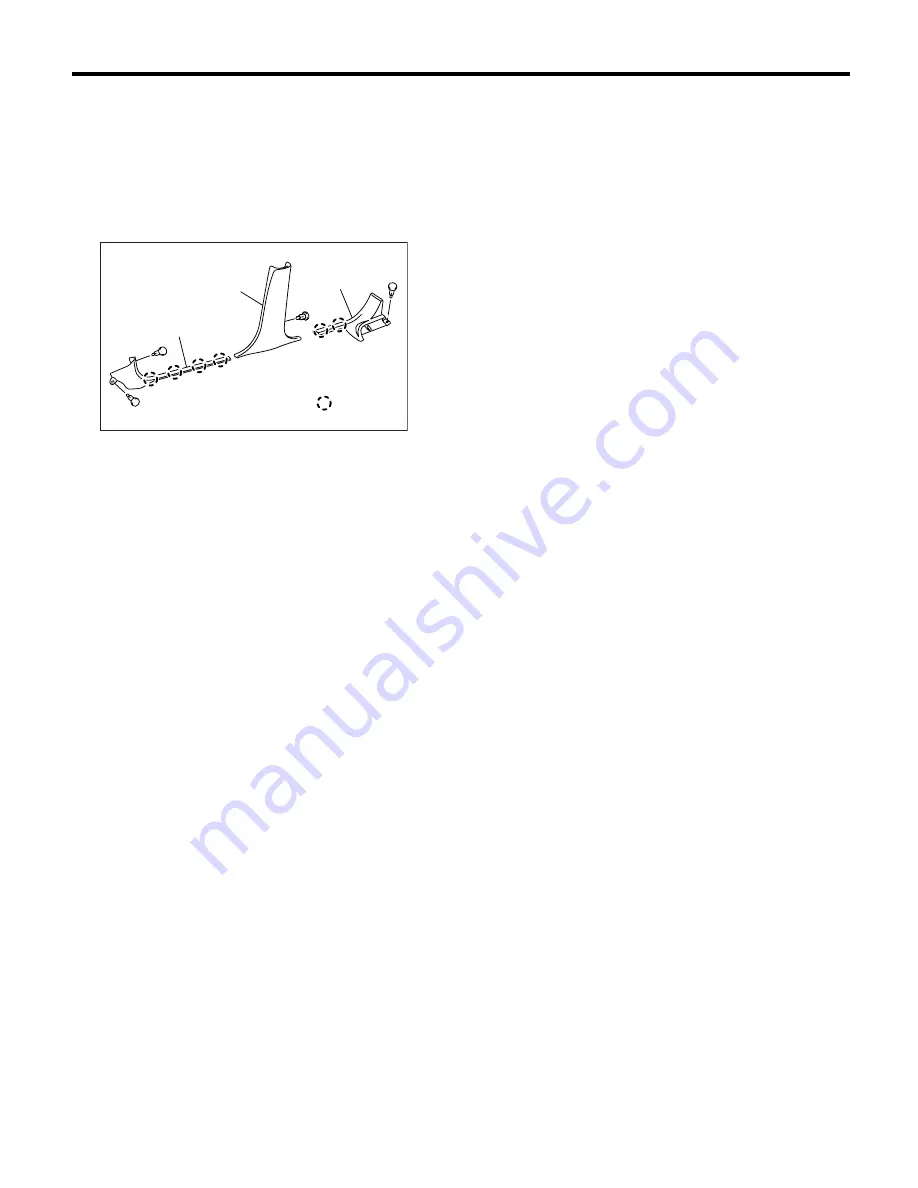
EI-44
EXTERIOR/INTERIOR TRIM
Lower Inner Trim
18.Lower Inner Trim
A: REMOVAL
1) Remove the side sill front cover (A).
2) Remove the rear seat cushion <Ref. to SE-13,
REMOVAL, Rear Seat.>, then remove side sill rear
cover (B).
3) Remove the center pillar lower trim (C).
B: INSTALLATION
Install in the reverse order of removal.
CAUTION:
Be sure to securely hook pawls of inner trim
panel to body flange.
(D) Clip
EI-00072
(A)
(C)
(B)
: (D)
Summary of Contents for 2004 Forester
Page 54: ...AC 52 HVAC SYSTEM HEATER VENTILATOR AND A C General Diagnostics ...
Page 96: ...AC 42 HVAC SYSTEM AUTO A C DIAGNOSTIC General Diagnostic Table ...
Page 306: ...ET 10 ENTERTAINMENT Front Accessory Power Supply Socket ...
Page 312: ...COM 6 COMMUNICATION SYSTEM Horn Switch ...
Page 347: ...BODY STRUCTURE BS Page 1 General Description 2 2 Datum Points 3 3 Datum Dimensions 11 ...
Page 356: ...BS 10 BODY STRUCTURE Datum Points 61 BS 00030 66 62 63 BS 00031 64 BS 00032 ...
Page 380: ...IDI 18 INSTRUMENTATION DRIVER INFO Ambient Sensor ...
Page 381: ...SEAT SE Page 1 General Description 2 2 Front Seat 6 3 Rear Seat 13 ...
Page 436: ...SL 42 SECURITY AND LOCK Keyless Transmitter ...
Page 446: ...SR 10 SUNROOF T TOP CONVERTIBLE TOP SUNROOF Sunroof Switch ...
Page 456: ...EI 10 EXTERIOR INTERIOR TRIM General Description 12 REAR GATE TRIM EI 00012 ...
Page 532: ...CC 14 CRUISE CONTROL SYSTEM Neutral Position Switch MT model ...
Page 571: ...CRUISE CONTROL SYSTEM DIAGNOSTIC CC H4DOTC Page 1 General Description 2 ...