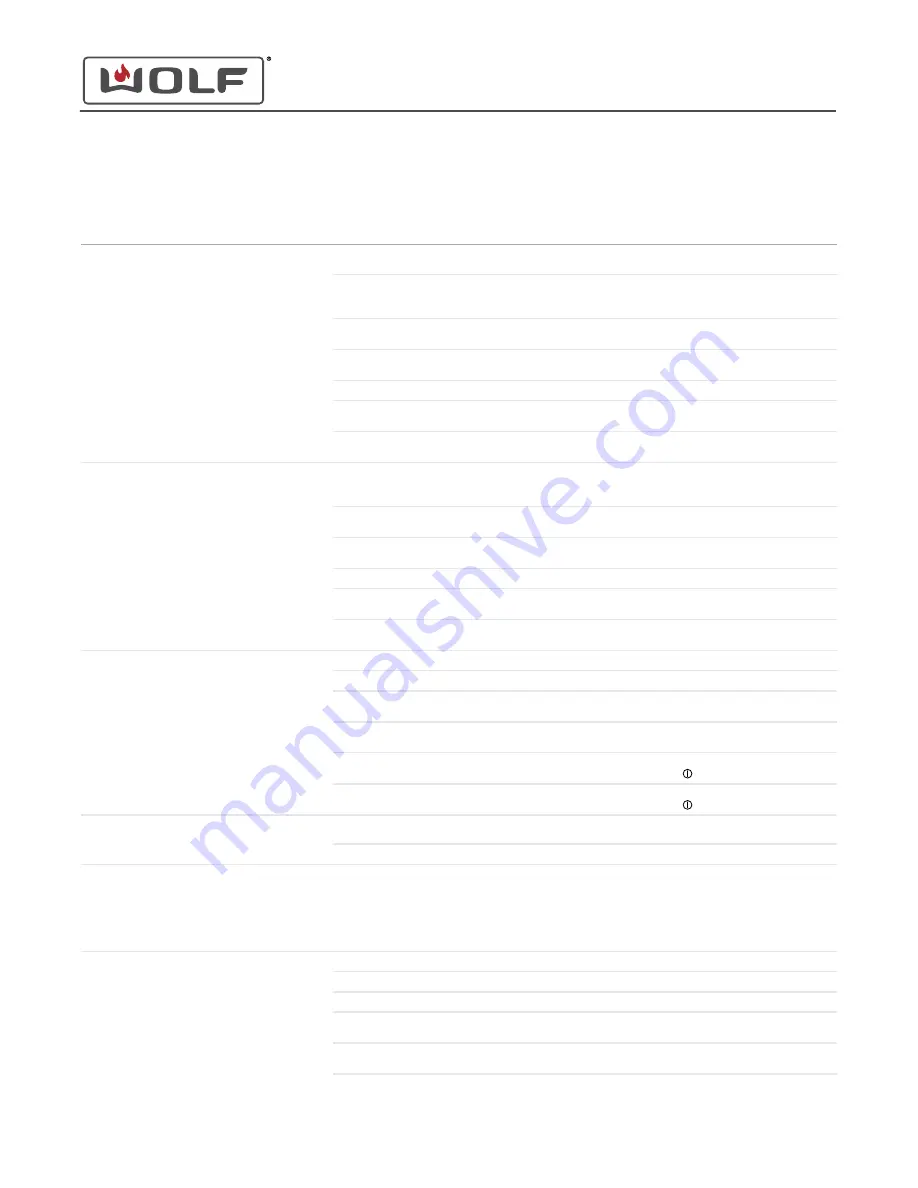
Page 25
GENERAL TROUBLESHOOTING
Error
Possible Cause
Solution
Appliance will not start.
Fuse is defective.
Verify the fuse is not blown, damaged, or
improperly seated.
Mains cable (external) is defective.
Check the mains cable for visible damage or
pinches. Make sure the connections are
connected and tight.
Mains cable (internal) is defective.
Make sure the connections are connected
and tight.
Control panel is defective.
Check for visible damage to the control
panel.
Control board is defective.
Check.
Ribbon cable between the control board and
control panel electronics is defective.
Check the ribbon cable for twists, tears, or
pinches.
Ribbon cable between the control board and
control panel electronics is loose.
Check the ribbon cable for proper connector
seating.
Appliance is not being ventilated.
Mains cable (external) is defective.
Check the mains cable for visible damage or
pinches. Make sure the connections are
connected and tight.
Mains cable (internal) is defective.
Make sure the connections are connected
and tight.
Control panel is defective.
Check for visible damage to the control
panel.
Control board is defective.
Check.
Ribbon cable between the control board and
control panel electronics is defective.
Check the ribbon cable for twists, tears, or
pinches.
Ribbon cable between the control board and
control panel electronics is loose.
Check the ribbon cable for proper connector
seating.
Appliance is not being ventilated. Lid will not
open.
Power failure.
Check the electrical supply.
Relay on control board is defective.
Replace the control board.
Valve block cable/plug connector is
defective.
Check the cable for proper seating and
continuity.
Valve is defective.
Test the valve in the Service menu. If it does
not respond, replace the valve.
Sharp change in air pressure (range hood,
slammed door)
Unplug the power cable. Plug in the power
cable, and touch .
Lid pressed in too much
Unplug the power cable. Plug in the power
cable, and touch .
Stand-by (ON/OFF) is in order, but buttons
are unresponsive.
Automatic button calibration fault.
Wait 5 seconds.
Control panel is defective.
Replace the control panel.
Button does not function despite being
repeatedly selected.
When the appliance is turned on, verify there
are no damp cloths/objects/hands on the
operating panel. The buttons can short-
circuit each other.
1
Make sure the control panel is dry.
2
Remove any objects, and dry the control
panel.
3
Switch the appliance off and then back
on again.
Stand-by (ON/OFF) is in order—pump not
starting—display on control panel
electronics, as no significant detectable fall
in pressure after 5 seconds.
Vacuum pump is defective.
Test vacuum pump function.
Control board is defective.
Check and replace if necessary.
Control board relay is not switching.
Check and replace if necessary.
Control board to vacuum pump cabling is
defective/loose.
Check and replace if necessary.
Capacitor is defective (humming) or is not
connected.
Check and replace if necessary.
ICB Vacuum Seal Drawer
Troubleshooting Guide
TROUBLESHOOTING GUIDE
service.subzero.com
826148 REV. A 01/2019
24