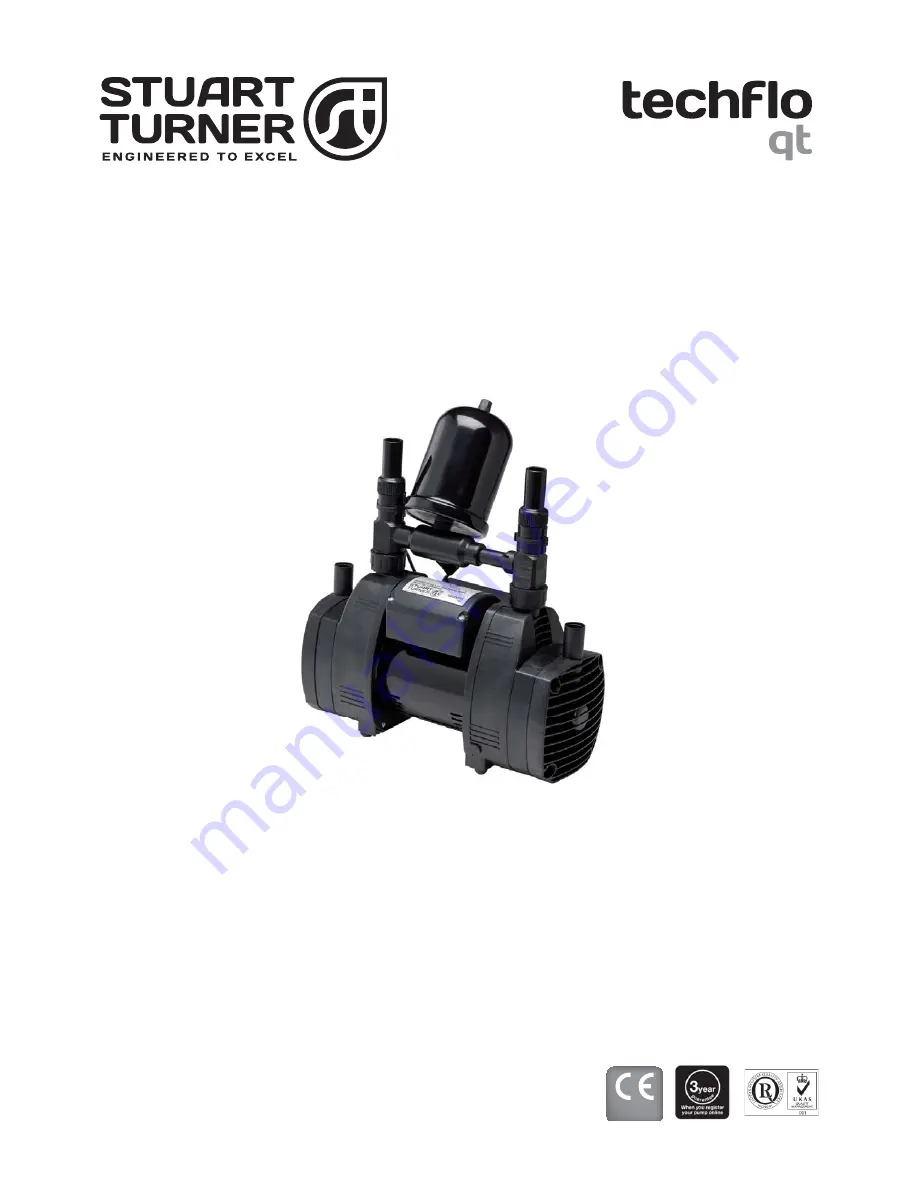
Installation, Operation & Maintenance
Instructions
Please leave this instruction booklet with the owner as
it contains important guarantee, maintenance and safety
information
Read this manual carefully before commencing installation.
This manual covers the following products:
U2.3 bar Single
Pt. No. 49082
U2.3 bar Twin
Pt. No. 49080
U3.3 bar Single
Pt. No. 49083
U3.3 bar Twin
Pt. No. 49081
FOR POSITIVE OR NEGATIVE HEAD APPLICATIONS
CE compliant product