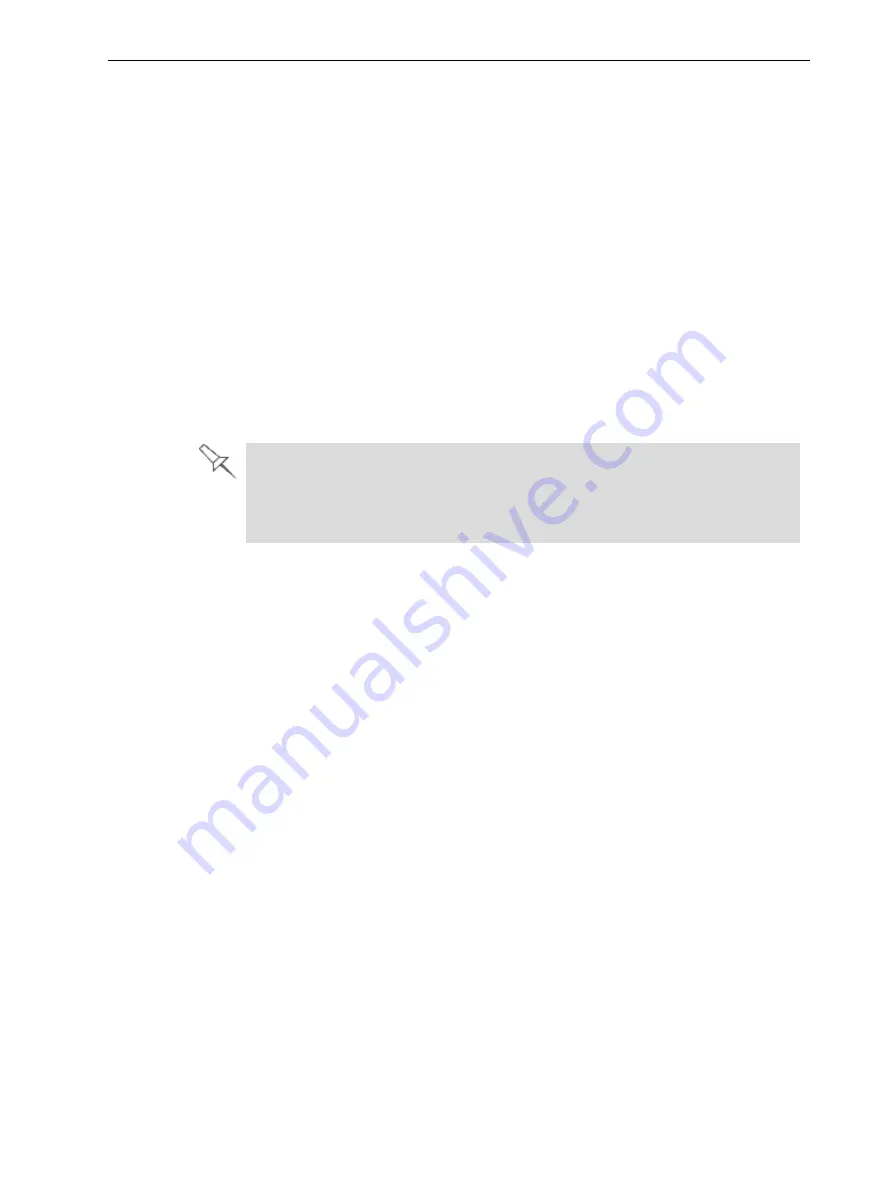
Stratasys J4100 User Guide
4 Operating and Maintaining the Printer
DOC-26000 Rev. C
4-56
Optimizing (Calibrating) Print Heads
The condition of the print heads directly affects the quality of printed models. To
maintain optimum printing, you should routinely test the print heads, and calibrate
them to the best working configuration possible by running the Head
Optimization wizard every 300 hours of printing.
You also need to calibrate the print heads in these cases:
• after changing the printing mode
• after replacing Vero with Digital ABS or Agilus30 Model materials (and the
reverse)
• after replacing the Support material with cleaning fluid (and the reverse)
If, during the optimization process, the wizard determines that a print head is
faulty—or that it is negatively affecting layer uniformity with the current head
configuration—the wizard instructs you to replace it. If this happens, you can
continue the wizard to replace the print head, or abort the wizard, to replace the
head at another time.
Run the Head Optimization wizard every 300 hours of printing or whenever
the condition of print heads is negatively affecting the quality of printed
models, or if you suspect that there is a problem with one or more of the print
heads.
Note:
To accurately test and calibrate print heads, they must be clean. If
necessary, run the Cleaning wizard before beginning this procedure.
To test and calibrate the print heads:
1. Prepare—
❒
disposable cleaning gloves (any clean, powder-free protective gloves)
❒
pink paper
❒
the Missing Nozzles ruler
❒
the scale supplied for use in the Head Optimization wizard
Important:
Before beginning this procedure, ensure that the scale is
calibrated and at least partially charged.