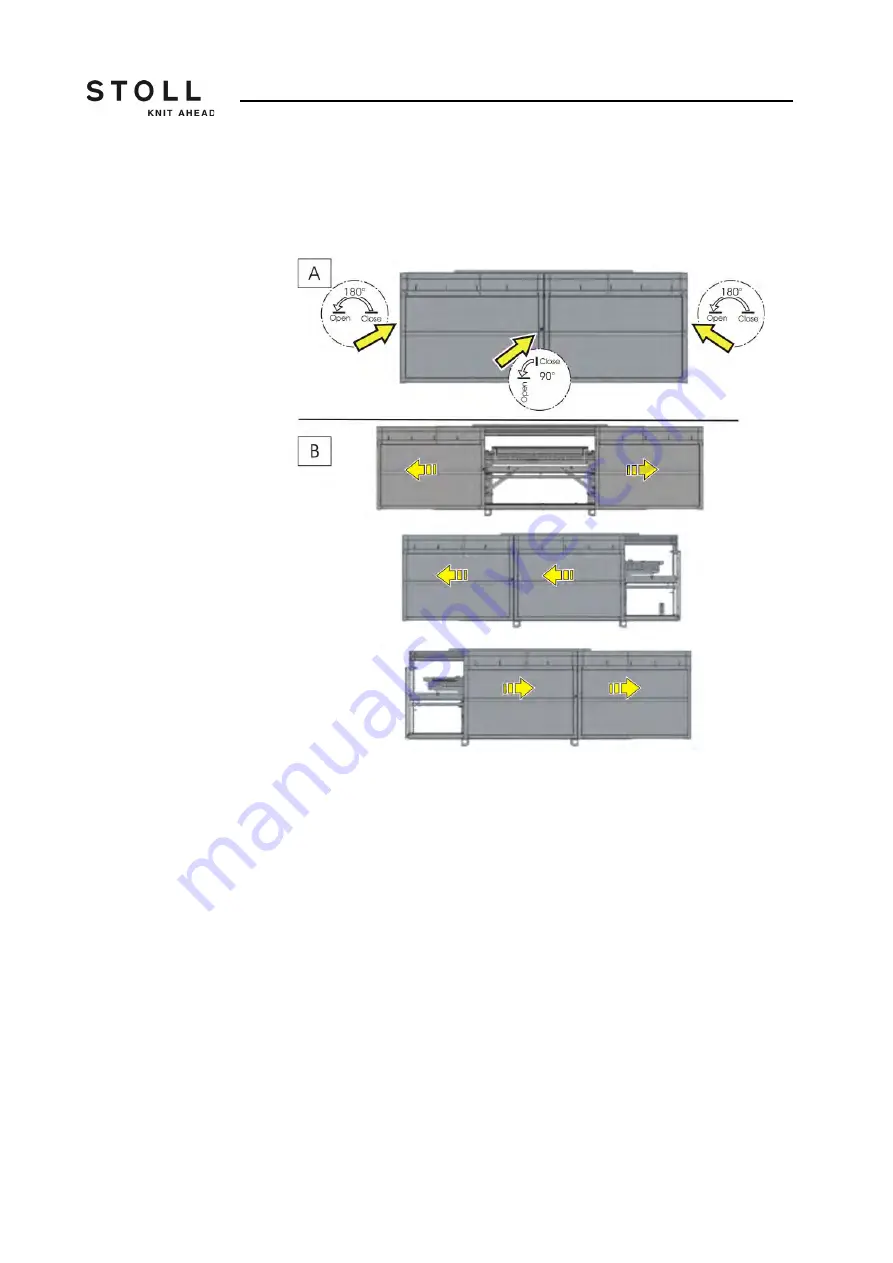
Repairing the knitting machine
7
Supplementary activities during maintenance 7.1
302
7.1.5
Sliding board
The sliding board consists of two individual boards. Each sliding board can
be pushed to the left or to the right.
A
The sliding boards are secured at three points. Use the square spanner from
the accessories for opening.
B
Each sliding board can be pushed to the left or to the right.
To be able to remove rear carriage part from the machine, push both sliding
boards into the same direction.
Summary of Contents for CMS ADF-3
Page 16: ...About this document 1 Warnings in the documentation 1 5 16...
Page 232: ...Adjusting knitting machine 4 Defining user profile 4 6 232...
Page 270: ...Setup Data 5 Setup1 Editing the setup file 5 5 270...
Page 296: ...Maintenance of the knitting machine 6 Lubricate knitting machine 6 3 296...
Page 410: ...Software Installation and basic settings 8 Diagnose Control 8 5 410...
Page 436: ...Machine Management Tools 10 Send email directly from the machine 10 4 436...
Page 444: ...Key word directory 11 444...