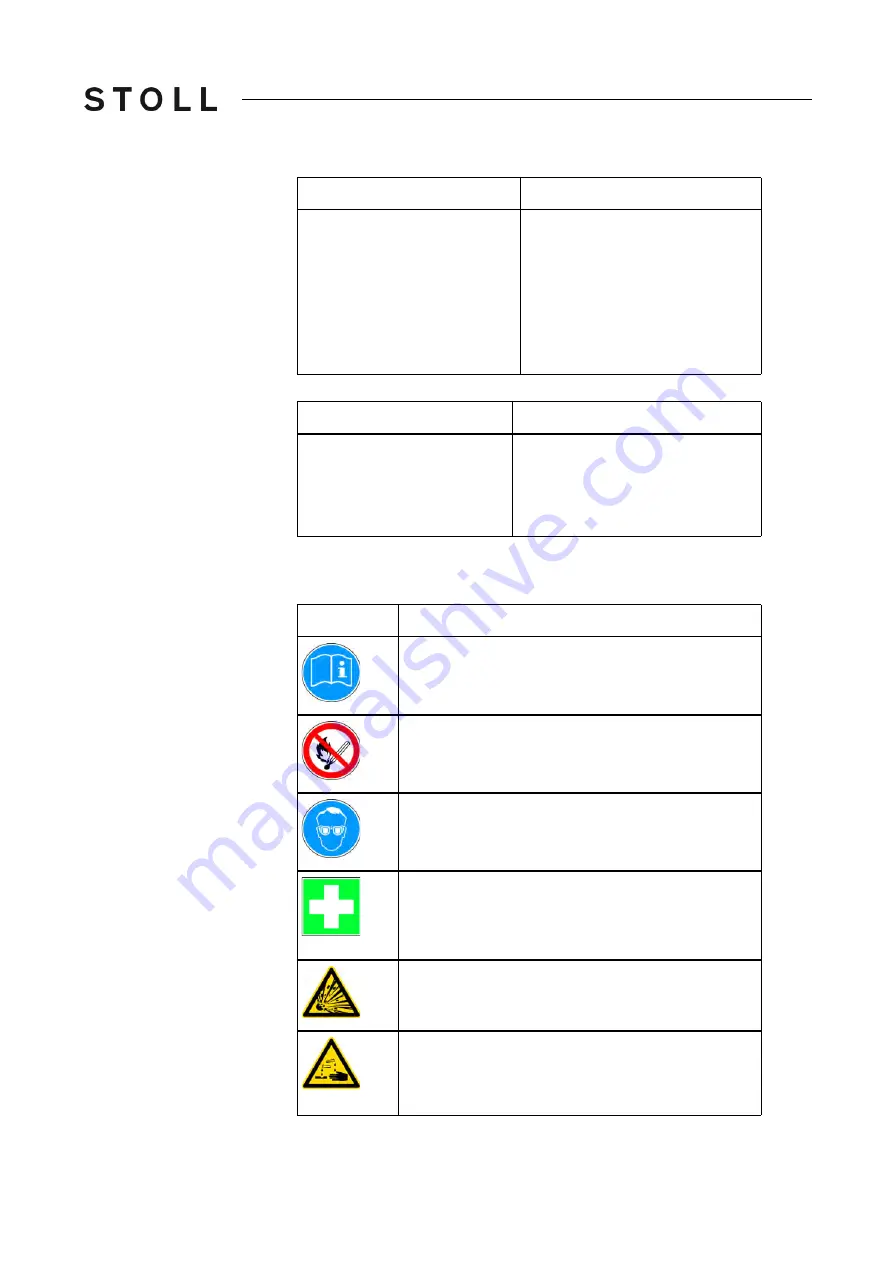
23
Safety instructions
2
Safety precautions regarding the machine's life phases
Other dangers
Other dangers
Reason
Measures
Danger of damage by usage of
unsuitable cleaning materials.
Only cleaning materials that have been
mentioned in the Operating Instructions
for e.g. Alcohol are to be used. Do not
use cleansing materials that can cause
health hazards or are corrosive.
Safety precautions for the battery
Safety precautions for the
battery
The following safety instructions and protective measures must always be
observed when handling the battery.
Environment pollution is caused if
the disposal of replaced parts and of
consumables is not done
professionally.
Ensure that all consumables and
replaced parts are disposed of safely
and with minimum environmental
impact!
Observe the country-specific laws and
regulations.
Observe the manufacturer's
specifications (safety data sheet).
Reason
Measures
Pictograph
Safety precautions and protective measures
Observe the safety precautions and protective measures.
No smoking.
Do not allow open flame, glow or sparks in the vicinity of the
battery because of explosion and fire hazards.
Wear safety glasses as battery acid is highly corrosive.
In case of acid splashes in the eye or on the skin flood with
clear, cool running water. Afterwards, immediately see a
doctor.
Wash the clothing with water.
Explosion and fire hazards, avoid short circuits.
Charge the battery only in assembled state within the
knitting machine.
Battery acid is highly corrosive.
During normal operation the contact with the battery acid is
excluded. In case of destruction of the housing, the battery
acid can escape. Danger of acid burns.