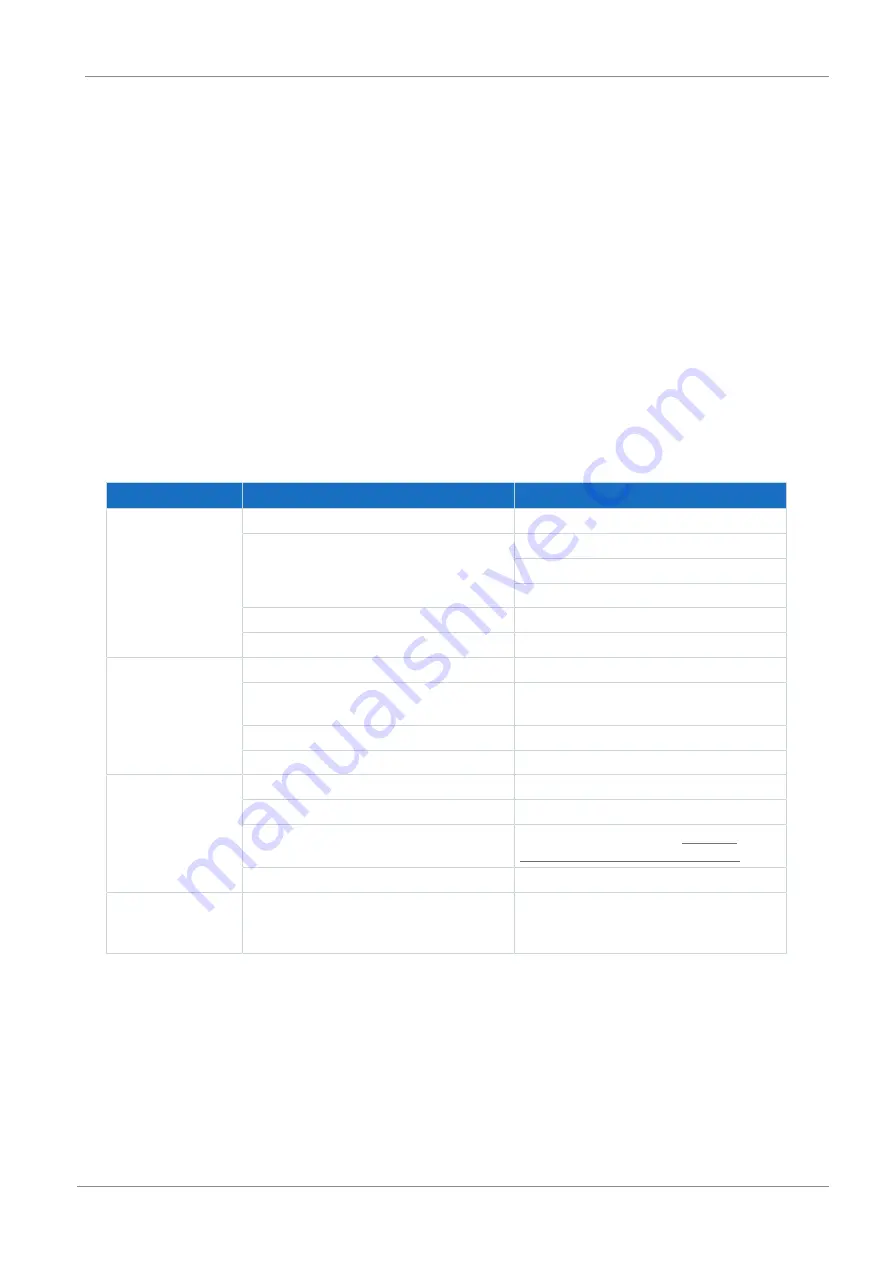
7 | Servicing
10/2019 | ID 443149_en.00
31
7.3
Remedying faults
WARNING! Moving machine parts can cause serious injuries or even death!
Before performing work, switch
off the machine with the main switch and secure the switch from being turned on again.
Notify all personnel working on the machine or the drive of deviations from normal operation. These deviations indicate
that the function of the drive is impaired. These include:
§
Higher operating temperatures or increased vibrations
§
Unusual noises or smells
§
Triggering of monitoring systems
§
Leaks on the housing of the gear unit
In such an event, shut down the drive and notify the responsible service personnel immediately.
7.3.1
Troubleshooting faults
The following table describes faults that can occur during the operation of the gear unit. Read through the table from top to
bottom when troubleshooting faults.
Faults
Possible causes
Actions
Operating
temperature is higher
or exceeds the
permitted
temperature of the
gear unit
Speed or torque is too high
Check the design of the gear unit
Motor heats the gear unit (too much)
Cool the motor sufficiently
Check the wiring of the motor
Replace the motor
Surrounding temperature is too high
Provide sufficient cooling for the gear unit
Bearing damage
Contact STOBER Service
Increased or different
noises or vibrations in
operation
Motor is mounted with too much tension
Check the assembly of the motor
Gear unit is mounted incorrectly or with too
much tension
Check the assembly of the gear unit
Bearing damage
Contact STOBER Service
Gear damage
Contact STOBER Service
Leaks
Radial shaft seal ring leaks
Contact STOBER Service
Output shaft damaged at the sealing point
Contact STOBER Service
Increased inner pressure due to operating
temperature that is too high
See measures in case of fault
Operating
temperature is higher … of the gear unit
Gear unit housing leaks
Contact STOBER Service
Output shaft does not
turn although motor is
running
Clamp coupling is defective or tightened
incorrectly
Check the clamp coupling
7.4
Servicing
Have the necessary servicing work carried out on the drive by the STOBER Service department or by STOBER service
partners. Be aware that improper servicing may cause material damage and may void the manufacturer's warranty.
Only use replacement parts delivered by STOBER. Specify the type designation and serial number of the drive when
ordering replacement parts. These can be found on the nameplate of the drive.