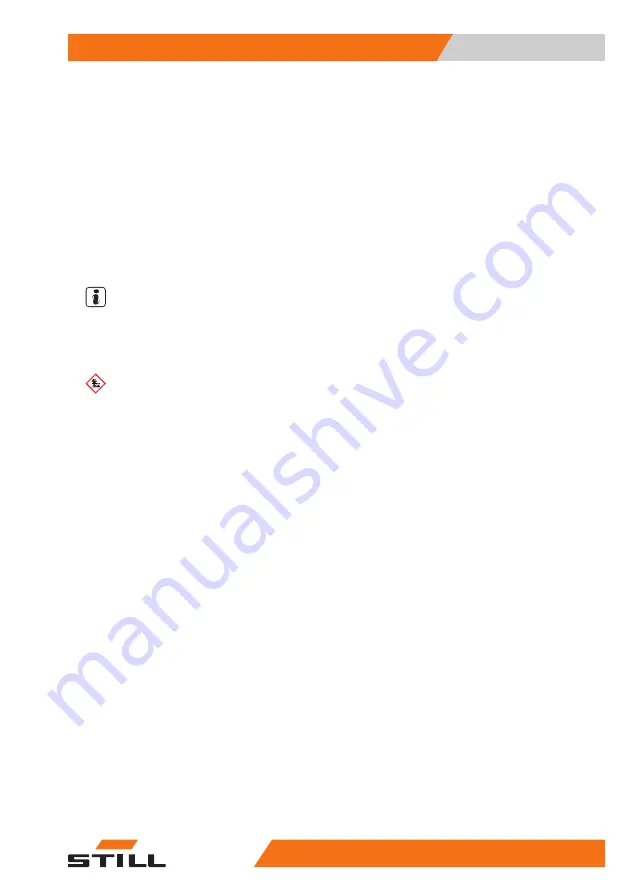
Environmental considerations
Disposal of components and batter-
ies
The truck is composed of different materials. If
components or batteries need to be replaced
and disposed of, they must be:
●
disposed of,
●
treated or
●
recycled in accordance with regional and
national regulations.
NOTE
The documentation provided by the battery
manufacturer must be observed when dispos-
ing of batteries.
ENVIRONMENT NOTE
We recommend working with a waste man-
agement company for disposal purposes.
Safety
2
Environmental considerations
21
60128011601 EN - 03/2020
Summary of Contents for RCD40
Page 1: ...Diesel forklift truck RCD40 50 Original instructions 4231 4233 60128011601 EN 03 2020 ...
Page 2: ......
Page 4: ......
Page 10: ......
Page 11: ...1 Introduction ...
Page 19: ...2 Safety ...
Page 34: ...Safety 2 Emissions 24 60128011601 EN 03 2020 ...
Page 35: ...3 Overview ...
Page 43: ...Location of the decals Overview 3 Location of the decals 33 60128011601 EN 03 2020 ...
Page 46: ...Overview 3 Location of the decals 36 60128011601 EN 03 2020 ...
Page 47: ...4 Use and operation ...
Page 110: ...Use and operation 4 Decommissioning 100 60128011601 EN 03 2020 ...
Page 111: ...5 Maintenance ...
Page 149: ...6 Technical datasheet ...
Page 150: ...Dimensions Technical datasheet 6 Dimensions 140 60128011601 EN 03 2020 ...
Page 160: ......
Page 161: ......
Page 162: ...STILL GmbH 60128011601 EN 03 2020 ...
Page 163: ...Diesel forklift truck RCD40 50 Original instructions 4231 4233 60128011601 EN 03 2020 ...
Page 164: ......
Page 165: ...7 Diagrams ...
Page 166: ...Electric schematic diagram Diagrams 7 Electric schematic diagram 156 60128011601 EN 03 2020 ...
Page 167: ...Hydraulic diagram Diagrams 7 Hydraulic diagram 157 60128011601 EN 03 2020 ...
Page 168: ...Diagrams 7 Hydraulic diagram 158 60128011601 EN 03 2020 ...
Page 169: ......
Page 170: ...STILL GmbH 60128011601 EN 03 2020 ...