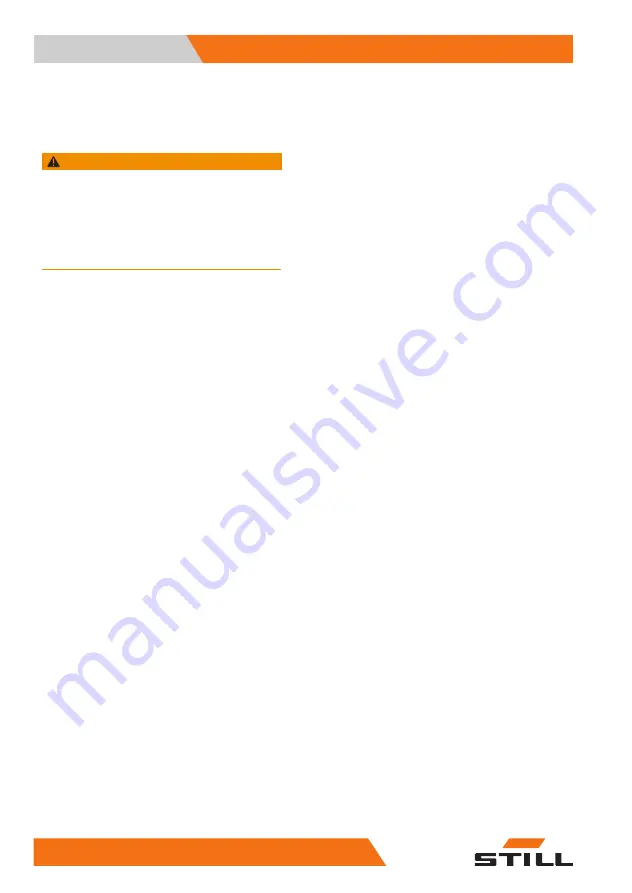
5
Operation
Checks and operations prior to commissioning
Checks and operations prior to commissioning
Visual inspections
WARNING
Damage or other defects on the industrial truck can
result in accidents.
If damage or other defects are identified on the
industrial truck during the following inspections, do
not use the industrial truck until it has been repaired
properly. Do not remove or disable safety systems
and controls. Do not change predefined set values.
Prior to start-up, ensure that the truck is safe
to be operated:
– Fork arms or other load-carrying equipment
should not show any noticeable damage
(e.g. bends, cracks, significant wear).
– Check the area under the industrial truck for
leaking consumables.
– Check whether all decal information is
present and legible. Damaged or missing
adhesive labels must be replaced according
to the overview of identification points, see
⇒ Chapter "Identification points", P. 32.
– Check the visible areas of the hydraulic sys-
tem for damage and leakages. Damaged
components must be changed.
– Report defects to the supervisory person-
nel.
36
50988046052 EN - 10/2018
Summary of Contents for HPT 10 XE
Page 2: ......
Page 4: ......
Page 9: ...1 Foreword ...
Page 17: ...2 Introduction ...
Page 25: ...3 Safety ...
Page 36: ...3 Safety Safety regulations for handling consumables 28 50988046052 EN 10 2018 ...
Page 37: ...4 Overviews ...
Page 43: ...5 Operation ...
Page 64: ...5 Operation Cleaning 56 50988046052 EN 10 2018 ...
Page 65: ...6 Maintenance ...
Page 82: ...6 Maintenance Maintenance after 3 months 74 50988046052 EN 10 2018 ...
Page 88: ...6 Maintenance Maintenance after 12 months 80 50988046052 EN 10 2018 ...
Page 89: ...7 Technical data ...
Page 94: ...7 Technical data Technical datasheet 86 50988046052 EN 10 2018 ...
Page 98: ......
Page 99: ......
Page 100: ...STILL GmbH 50988046052 EN 10 2018 ...