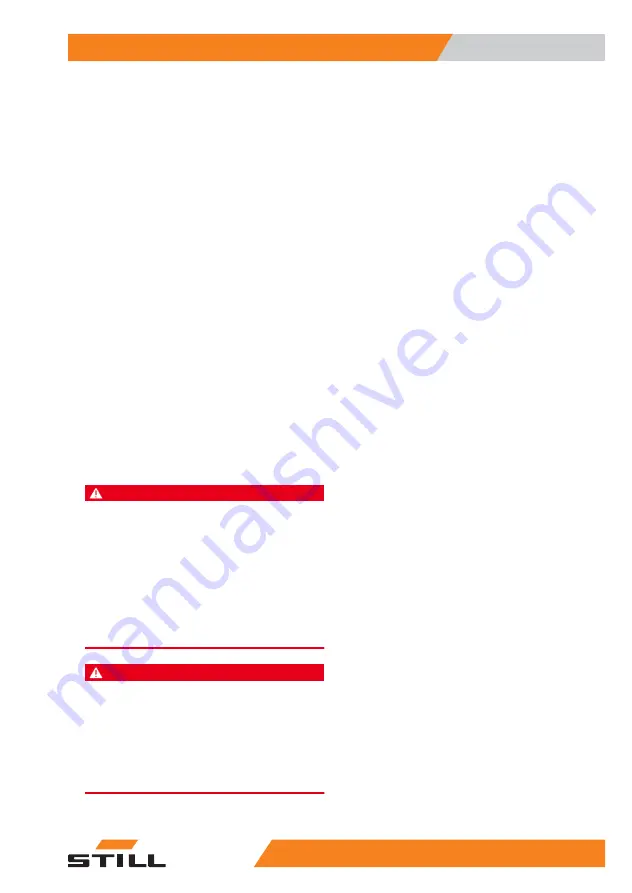
Attachments
Fitting attachments
If the truck is equipped with an integrated at-
tachment (variant) at the factory, the specifica-
tions in the STILL operating instructions for in-
tegrated attachments must be observed.
If attachments are fitted at the place of use,
the specifications in the operating instructions
from the attachment manufacturer must be ob-
served.
If an attachment is not delivered together with
the truck, the specifications from the manufac-
turer and the operating instructions from the
attachment manufacturer must be observed.
Before initial commissioning, the function of
the attachment and the visibility from the driv-
er's position with and without a load must be
checked by a competent person. If the visibili-
ty is deemed insufficient, visual aids must be
used, such as mirrors, a camera, a monitor
system etc.
–
Observe the following warning notices.
DANGER
Risk of fatal injury from falling load!
If attachments that hold the load by clamping it or ex-
erting pressure on it do not have a second method of
operating the function (lock), the load can work loose
and fall off.
–
Ensure that the second method of operating the
function (lock) is available.
–
When retrofitting such attachments, a second
method of operating the function (lock) must also
be retrofitted.
DANGER
Risk of fatal injury from falling load!
When installing a clamp with an integrated sideshift
function, ensure that the clamp does not open when
the sideshift is actuated.
–
Notify your authorised service centre before instal-
lation.
–
Never grab or climb on moving parts of the truck.
Operating
4
Attachments
159
50988078001 EN - 11/2021 - 10
Summary of Contents for FM-X 10 N
Page 2: ......
Page 4: ......
Page 13: ...1 Foreword ...
Page 33: ...2 Safety ...
Page 51: ...Safety 2 Residual risk 39 50988078001 EN 11 2021 10 ...
Page 67: ...3 Overviews ...
Page 84: ...Overviews 3 Operating devices and display elements 72 50988078001 EN 11 2021 10 ...
Page 85: ...4 Operating ...
Page 311: ...5 Maintenance ...
Page 318: ...Maintenance 5 General maintenance information 306 50988078001 EN 11 2021 10 ...
Page 324: ...Maintenance 5 General maintenance information 312 50988078001 EN 11 2021 10 ...
Page 337: ...6 Technical data ...
Page 378: ......
Page 379: ......