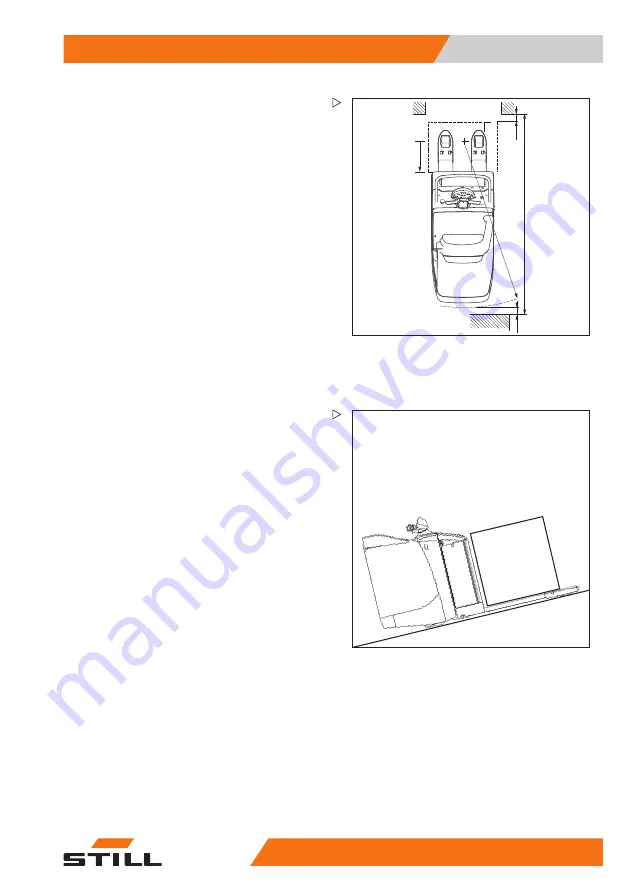
Application
4
Driving
X
100
Ast 3
Wa
100
0148_003-014
Dimensions of roads and working
aisles
The dimensions specified in the description
section apply under established conditions
and should ensure safe manoeuvring. Check
in each case whether a wider aisle is required
when, for example, the load dimensions
deviate.
The required aisle widths (Ast) depend on
the dimensions of the load and are calculated
according to the following formula: Ast = Wa -
X + length of 200 mm.
Observe your local and national regulations.
Please see ⇒ Chapter "VDI data sheet for
standard EXU-S 22", P. 6-101.
The truck may only be used on roadways
without any tight curves, excessive slopes or
passages that are too narrow or too low.
0148_003-015
The following inclines or slopes may be driven
on with the truck:
The slopes must not exceed the above
gradients and should have a rough surface.
Smooth passages at the top and lower end
should prevent the load from touching the
ground or damage to the truck.
Condition of roadways
Roadways must be solid enough, free of
debris and fallen objects. Drainage ducts,
tracks and the like must be level and, if
necessary, provided with ramps so that they
can be crossed without jolts, if possible.
There must be sufficient clearance between
the highest parts of the truck or the load and
the surrounding fixtures. The height depends
on the lift height and the load dimension.
Check the datasheet for the truck.
Rules for roadways and working area
Only roadways made available by the operator
or his representative may be driven on. The
roadways must be free of obstacles. The
load may only be stacked and stored in the
appropriate places. The operator and his
50018043464 EN - 10/2017
55
Summary of Contents for EXU-S 22
Page 2: ......
Page 4: ......
Page 9: ...1 Introduction ...
Page 19: ...2 Safety ...
Page 28: ...2 Safety Safety tests 20 50018043464 EN 10 2017 ...
Page 29: ...3 Overview ...
Page 44: ...3 Overview Options 36 50018043464 EN 10 2017 ...
Page 45: ...4 Application ...
Page 98: ...4 Application Storage 90 50018043464 EN 10 2017 ...
Page 99: ...5 Maintenance ...
Page 107: ...6 Technical data ...
Page 108: ...6 Technical data Dimensions Dimensions 100 50018043464 EN 10 2017 ...
Page 121: ......
Page 122: ...STILL GmbH 50018043464 EN 10 2017 ...