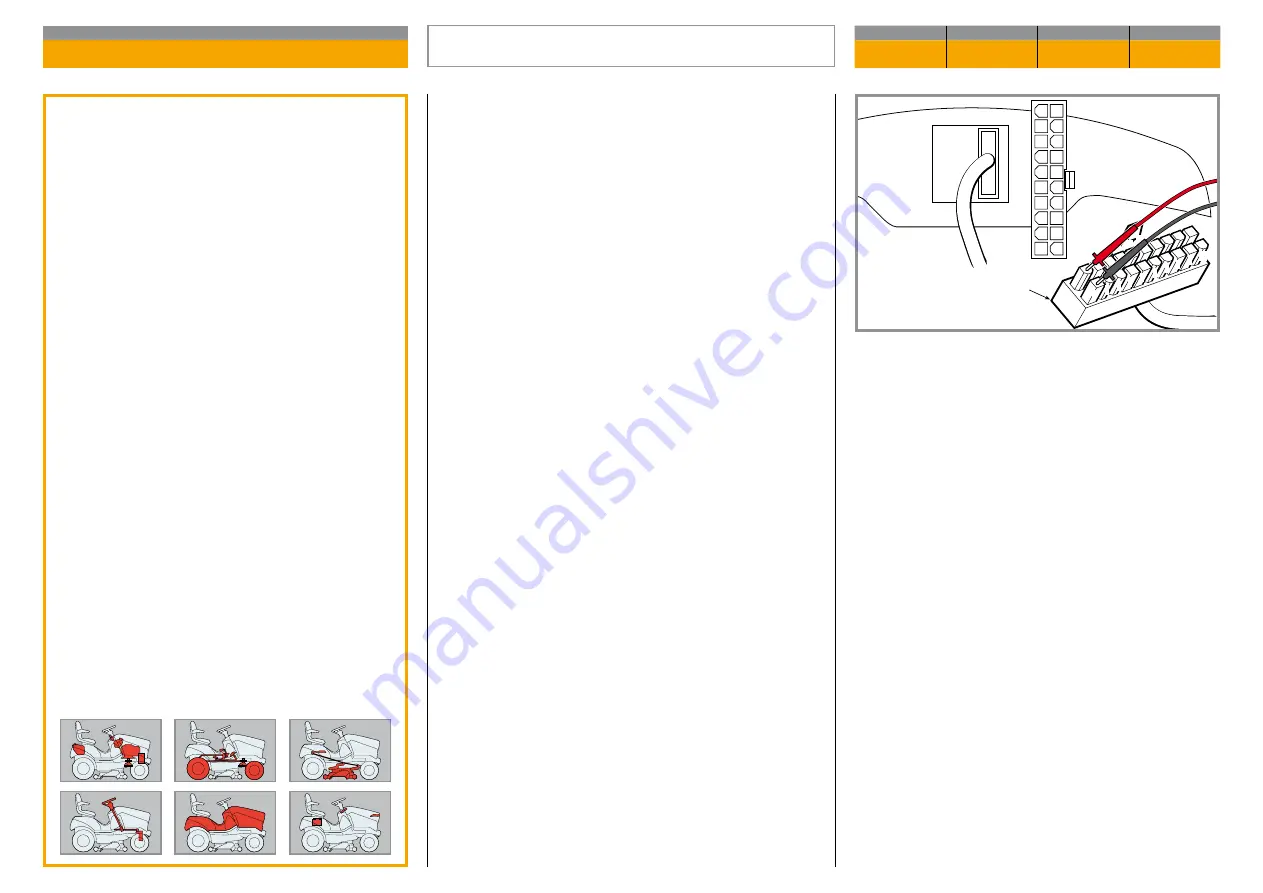
WORKSHOP MANUAL
Map of functional units
TC 108 SD - TC 118 SD
This check is made with the tester operating as a
Voltmeter (Volts DC 0 ÷ 20), with the black ferrule on
terminal 1 and the red one on terminal 11of the con-
nector (1) of the wiring.
– The key in the «ON» position
The reading shows the battery voltage, which should
never go below 11 Volts.
General informations
Related topics
---
TERMINAL BOARD SUPPLY CHECK
CHAPTER
REVISION
FROM ...
PAGE
7.4
0
2018
1 of 1
1
2
3
4
12 13
14 15
16 17
18 19
20
11
3 4
5 6
7 8
9 10
1 2
CN2
CN1
1 11
2 12
3 13
4 14
5 15
6 16
7 17
8 18
9 19
10 20