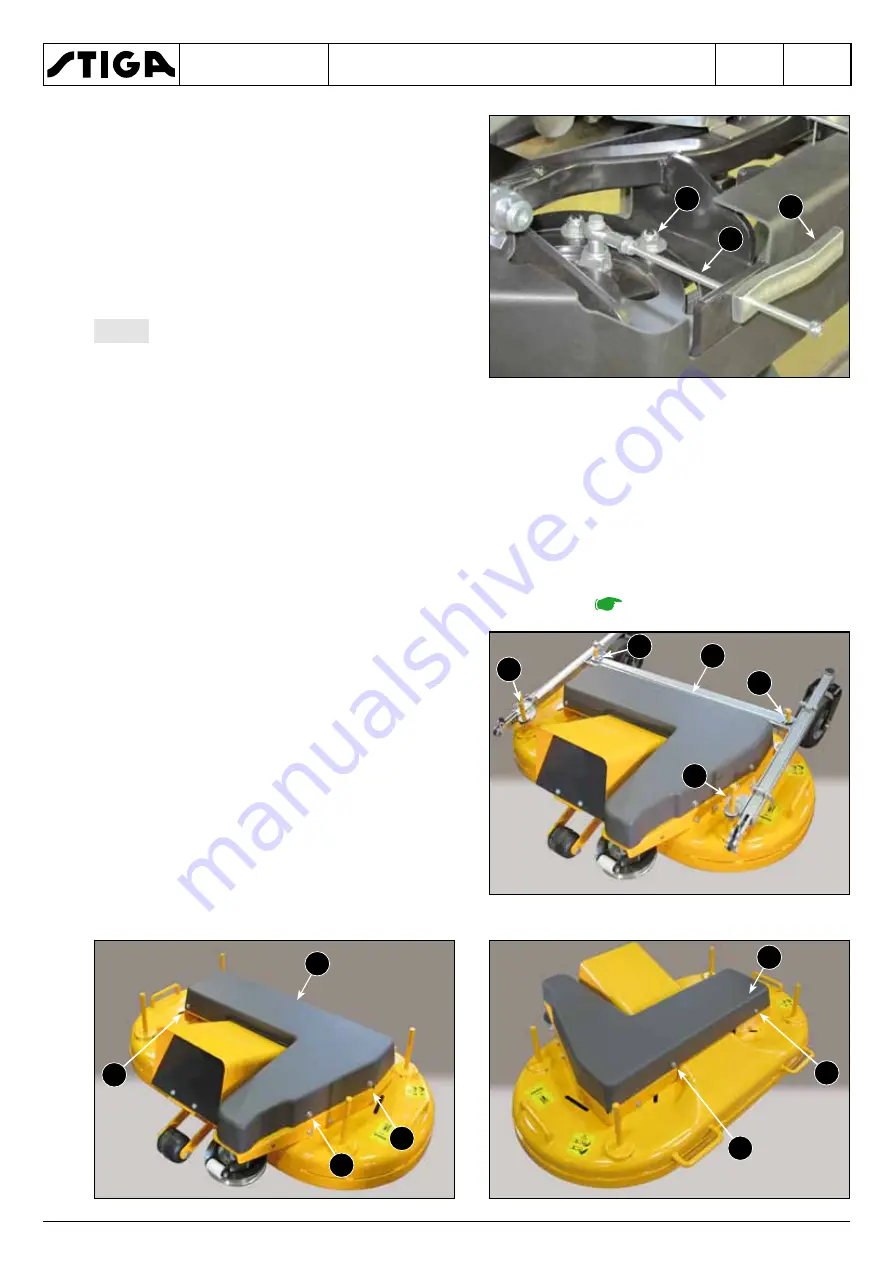
WORKSHOP MANUAL
MPV 320W / 520W
Chapter
6 - CUTTING DECK AND COLLECTION
EDITION
2017
PAGE
39 /
64
4. In different values are detected, loosen the
nut (8) and turn the handle (9) screwing or
unscrewing it on the bolt (10) until the correct
value is reached.
5. When the adjustment has been made, tighten
the nut (8).
NOTE
If the correct value cannot be reached, it
is necessary to adjust the spring (6) nut (4) again.
6.2.4 Replacing and adjusting the blade connection belt
• Follow all steps of the "Removing the cutting deck” procedure
[
.
1. Release the four split pins (1) and remove the
pivot arm carriage (2).
2. Remove the protective cover (3) fixed by the
five screws (4).
8
10
9
2
1
1
1
1
3
4
4
4
3
4
4